It is not always easy to identify good suppliers. Records maintained or procured from some other, sources about the vendors help in their evaluation and rating. Usually a combination of price, quality, quantity, delivery time, service etc. giving relevant weight ages to these factors is used to rate the vendors. In addition, a checklist can be used to facilitate rating from department standpoints. Some of the points are mentioned below:
Reliability
- Is the supplier reputable, stable and financially strong? ,
- Are the supplier’s integrity and ability above doubt?
- Is the supplier going along with product improvement?
- Is the supplier’s competitive strength as to price, quality, etc. proved by past experience?
Technical Capabilities
- Can the supplier provide assistance as to application engineering?
- Can the supplier provide assistance as to analytical engineering?
- Can the supplier provide design assistance?
- Can the supplier handle special needs? And contribute to improve product efficiency/basic processes?
Convenience
- Can the supplier help reducing acquisition costs through personal visits, telephone calls, incoming inspections, rejection of defects, spoilage, etc?
- Can he offer other related products?
- Is he qualified to help in solving difficult problems?
- Does the supplier package his product conveniently?
Availability
- Does the supplier assure delivery in time?
- Are his stocks locally available, and or at short notice?
- Is the supplier’s location advantageous?
- Can he plan his supply to minimize inventory?
- Can he be depended on for a steady flow of materials?
After-sales Service
- Does the supplier have a service organization?
- Is an emergency service available?
- Are parts available, when needed?
Sales Assistance
- Can the supplier help building mutual markets?
- Will he recommend our products?
- Does the use of supplier’s product enhance appearance of our products?
Vendor Evaluation
Recognizing that there is a need for having good vendor, it is essential that supplies, are obtained from vendors after an evaluation of his capabilities. The buyer, who has to do the evaluation, is faced with two different situations;
- Evaluating the performance before the vendor has delivered anything.
- Evaluating the performance of vendor after the deliveries have been made.
The latter one is normally called Vendor Monitoring and the former Vendor Evaluation.
In case of Vendor Evaluation the buyer lacks the direct evidence on the results achieved by the vendor and must get his information in other ways. This includes (1) general reputation of vendor, (2) data from other buyers, (3) vendor surveys.
Vendor Rating
Product quality submitted by vendors has always been evaluated and used as a factor in making purchasing decisions. Recently, the evaluation has been formalized by the use of vendor rating formulas which provide a quantitative measure of vendor quality. These ratings are primarily meant to provide an overall quality rating of a vendor for use in reviewing, comparing, and selecting vendors. Vendor rating is not a tool for making decisions on submitted lots.
To create a single numerical quality score is difficult because there are several inputs, each involving its own unit of measure:
- The lot quality, expressed as lots rejected versus lots inspected.
- The parts qualities, expressed as per cent defective.
- The characteristic qualities, expressed in numerous natural units, e.g., rupees per square cm., per cent active ingredient, MTBF, etc.
- The economic consequences of bad quality, expressed in rupees
The National Association of Purchasing Agents, New York, has published three alternative vendor rating plans:
Categorical Plan: This is a non-quantitative system in which buyers hold a monthly meeting to discuss vendors and rate each as plus, minus, or neutral.
Weighted-point Plan: Each vendor is scored on various factors like quality, price, service etc. These factors are weighted and a composite rating is then calculated for each vendor. The details of this performance evaluation scheme are as follows:
Quality Rating: Quality Rating for a consignment
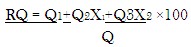
Where, Q
Q = Quantity supplied
Q1. = Quantity accepted
Q2 = Quantity accepted with concession
Q3 = Quantity accepted with rectification
Q4 = Quantity rejected
and
Q = Q1 +Q2+Q3-+Q4 20
X1 and X2 are weight age factors each less than 1.
Price Rating: Price rating for a consignment:
Rp = P ×100
PPL = Lowest price quoted
Where, P = Price agreed by supplier
Delivery Rating: Delivery rating for a consignment:

Rating in excess of 100 shall be equated to 100.
Quantity Rating: Quantity rating for a consignment:
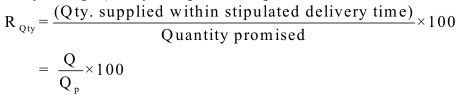
Service Rating: Service rating, RS, is to be assigned by Purchase Department as per the following table for each consignment.
SL. No. | Service Factor | Max. Score |
1 | Cooperativeness and readiness to help in emergencies | a1 |
2 | Readiness to replace rejected material | a2 |
3 | Providing support documents in time | a3 |
4 | Promptness in reply | a4 |
5 | Acceptance of terms without complaints | as |
Where a1 + a2 + a3 + a4 + a5 = 100
Composite Vendor Performance Rating:
VPR = f1RQ + f2RP + f3RD + f4RQty + f5RS
Where, fi+f2+f3+f4+f5=1
Fixing of Weight age Factors: In order to implement this scheme, it is necessary to fix the weight age factors X1, X2, a1, a2, a3, a4, a5, f1 f2, f3, f 4and f5 as suited to the organization
Cost-ratio Plan: This plan compares vendors on the total rupee cost for a specific purchase. Total cost includes price quotation, quality costs, delivery costs, and service costs. The final rating is in rupees of net value cost. The net value cost is the product of the adjusted unit price and the number of units. The adjusted unit price incorporates three cost ratios.
- The quality cost ratio reflects the relative cost of quality.
- The delivery cost ratio reflects the relative cost of placing and receiving an order. It also includes a promises-kept penalty based on a ranking of past performance of vendors.
- The service cost-ratio reflects the technical, managerial, and field service competence of the vendor.
All three of these plans recognize quality in the rating of vendors but the rating is not restricted to product quality.
Vendor Relations
The ultimate objective in vendor quality assurance is the production of materials which so adequately conform to the buyers, requirements that there is no need for extensive acceptance or corrective procedures by the buyer. The activities needed to achieve this objective include:
Communication of essential and helpful information, design, specifications, standards, practices etc.
- Communication of engineering changes, changes in specifications etc.
- Developing methods for detecting deviations from standards promptly
- Helping the vendor in resolving quality problems In case of vendors like sub-contractors and ancillaries, rendering necessary technical assistance as well
- Providing for use of vendor quality data in lieu of incoming inspection
- Using multiple vendors for major procurements of items
- Developing methods for identifying the qualified vendors, and for eliminating those who are unable to meet the quality requirements
- Reviewing the performance of the vendor through vendor rating or other plans and following up on the chronically poor vendors.
The guiding principle in vendor relations is the spirit of what is best for the partnership. The supplier must be made to realize that it is not sufficient to accept the returns willingly or to negotiate the disposition of materials not delivered to the specifications. The supplier should view such instances objectively and work constructively with the buyer to correct the conditions that brought about the. Delivery of unsatisfactory material or service.