It is the difference between the standard variable overhead cost allowed for the actual output achieved and the actual variable overheads. Normally this variance is represented by expenditure (cost) variance only because variable overhead cost will vary in proportion to production so that only a change in expenditure can cause such variance.
It is calculated as:
Variable Overhead Variance =
(Standard Variable Overhead Rate × Actual Output) – Actual Variable Overheads
OR
(Standard Hours for Actual Output × Standard Variable Overhead Rate) – Actual Variable Overheads
OR
(Standard Rate × Actual output) – (Actual Rate × Actual output)
The variable overhead cost variance is usually calculated in total only since variable overheads vary according to output and not according to time, hence, there is only one variance. However, some accountants argue that certain variable overhead may vary according to time also, hence variable overhead efficiency variance arise just like labour efficiency variance and it can be calculated if information relating to actual time taken and allowed is given. In such case variable overhead variance can be segregated into two parts.
Classification of labour variances as under:
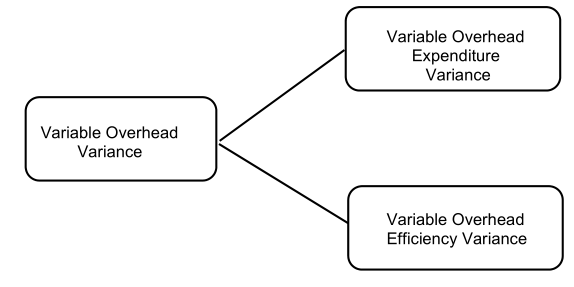
Variable Overhead Expenditure Variance (VOExV) =
(Actual Hours × Standard Variable Overhead Rate per Hour) – Actual Variable Overhead OR
Actual Hours (Standard Variable Overhead Rate per Hour – Actual Variable Overhead Rate per Hour)
Variable Overhead Efficiency Variance (VOEfV) =
(Standard Time for Actual Production × Standard Variable Overhead Rate per Hour) – Actual Hours Worked × Standard Variable Overhead Rate per Hour).
OR
Standard Variable Overhead on Actual Production – Standard Variable Overhead for actual time. OR
Recovered Overheads – Standard Overheads
It is better to compute variance related to variable overhead on the basis of hours rather then on the basis of units.
Illustration 4
The following data is obtained from the books of a manufacturing company regarding variable overheads:
Budgeted production for January 300 units
Budgeted variable overhead 7,800
Standard time for one unit 20 hours
Actual production for January 250 units
Actual hours worked 4,500 hours
Actual variable overhead 7,000
Solution
Variable Overhead Variance = Standard Cost – Actual Cost
= 6,500 – 7,000 = 500 (A)
Workings:
(a) Standard variable overhead cost of actual output
= 250 units × 26 per unit = 6,500
(b) Standard variable cost per unit
= 7800 or 26 per unit
Sometimes, a little refinement is introduced in the calculation of variable overhead variance and, therefore, the computation is as follows:
(i) Variable Overhead Expenditure Variance
= Actual Cost – Standard overheads on hours worked
7,000 – 5,850 = 1,150 (A)
(a) Standard variable overhead on hours worked is—
4,500 hours × 1.30 per hour = 5,850
(b) Standard variable overhead per hour
=7800 = 1.3
20 x300
(ii) Variable Overhead Efficiency Variance
= Standard variable overhead on hours worked – Standard variable overhead on actual output.
5,850 – 6,500 = 650 (F)
(iii) Variable Overhead Total Variance
= Expenditure Variance + Efficiency Variance
1,150 (A) + 650 (F) = 500 (A)
This is the same as variable overhead variance already arrived at.