There are different ways to categorize a process. They can be categorized on the basis of orientation, e.g. market orientation or manufacturing process; they may also be categorized on the basis of the production methodology or customer involvement. The various typeset processes are given below:
Processes by Market Orientation: There are four types of processes based on market orientation:
- Make to stock-The goods usually are standard, mature products. As a general rule make to stock products compete primarily on the basis of cost and availability. Example of such products includes most retail goods.
- Assemble to order-products are standard items that are assembled from in stock subassemblies. This allows customers to specify a wide range of options.
- Make to order- are made from previously designs, but are made only after an order has been received. Make to order products are used when the standard product is too costly to stock, have too uncertain demand, or will deteriorate if stocked on shelf.
- Engineer to order-This market orientation is used to make unique products that have not been previously engineered, Extensive customization to suite the customers’ need is possible but only if customer is willing to wait for this addition stage in the value creation process.
Processes as production systems: A production system refers to how an organization organizes material flow using different process technologies. There are five types of production systems:
- Projects: These are one-off projects. It is based on extensive customization that is suited to the customer’s ‘need. Many construction projects, project management contract, shipbuilding and civil engineering projects fall in this category.
- Job shop: Construction is characterized by processing of small batched of a large number of products, most of which require a different set or sequence of processing steps. Production equipment is mostly general purpose to meet the specific customer orders.
- Batch production: Production is in discrete parts that are repeated at regular intervals. Such a structure is generally employed for relatively stable lines of products, each of which is produced in medium volume.
- Assembly Line: It is a mass production process. On assembly line, production follows in a predetermined sequence of steps which are continuous rather than discreet. The product moves from work station to workstation at a controlled rate following the sequence needed to build the product.
- Continuous flow: It is common in the food processing industry, and in industries involving undifferentiated materials. Most bulk products are manufactured using continuous flow production; generally, on-line control and continuous system monitoring is needed.
Cell Manufacturing (Group Technology): A cell is a self sufficient unit, in which all operations required to make components or complete products can be carried out. It is like mini factory within the factory, which is managed by a cell team. Cell layouts can be U- shaped or s segment of a line allowing self organizing, multi-skilled group of fewer people to manage the operations
- Flexible manufacturing systems (FMS): Already explained earlier.
- Process and customer involvement: Many processes are designed keeping in mind that value is provided by involving the customer in the delivery of the final product. The involvement may range from self service to the customer by deciding the time and place where the service is to be produced. Business organizations are increasingly attempting to involve their customers in the product design by providing them different options for customization. They engage in an active dialogue with customers using new changing technologies. Customers are increasingly becoming partners in creating value. The customers can now decide the time and location where the service or product is to be delivered.
- Making Economic Decisions: Engineering economy is the discipline concerned with the economic aspects of engineering. It involves the systematic evaluation of the costs and benefits of proposed technical projects. In reality, any engineering project must be not only physically realizable but also economically feasible. For example, Maruti Udyog has decided that the weight of the Maruti 800 was a critical requirement of the design. How do you choose between plastic composite and steel sheet stock for the auto body panels? The choice of material will dictate the manufacturing process for the body panels as well as manufacturing costs. Some may argue that because the composite body panels will be stronger and was looking for a car that would be low cost so that it could tap the higher end of the two-wheeler users.
It also had to take into account that:
- The customer may not believe that plastics will provide a stronger body option than steel panels, and may not be willing to pay more, and
- A maintenance man may not believe that it is easy to repair composites, and therefore repair and maintenance will cost more.
One might suggest that the above arguments are ridiculously simplistic and that common sense would dictate choosing steel sheets for the framing material. Although the scenario is an exaggeration, it reinforces the idea that the economic factors of a design weight heavily in the design process, and that engineering economy is an integral part of that process, regardless of the engineering discipline.
The focus on economic cost and engineering costs of new product development has great importance. Each different technical solution to a problem constitutes an alternative. Each alternative requires different level of resources to build and causes different levels of resource to be expended. Thus trade-offs must be made during the design of engineered systems. Engineering economy selects the best alternative based on design for the theme.
- Why do this at all?
- Why do this now?
- Why do it this way?
An engineering cost analysis, in its simplest form, may be no more than a spreadsheet listing the phases found in the product concept through product realization cycles on one axis and identifying the many functional areas, costs, or even software tools on the other.
- In its second generation form, engineering cost analysis software will approximate the costs associated with each phase of the product development realization cycle.
In its ultimate form, the engineering cost analysis will include and improve upon all of systems engineering’s current discrete event optimization functions; but, more importantly, it will extend forward in time to include accurate estimates for various design, material, and process selection options. In some instances, it may also include the determination of the optimum product concept to satisfy the intended customer’s needs and cost constraints. Figure 3.1 provides a glimpse into the various inter-connections within the operations function that need to be taken into account in a properly designed engineering cost analysis.
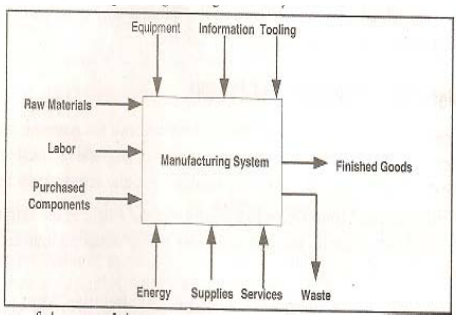
Figure 3.1 Second Generation Engineering Cost Analysis
As a rule of thumb, 70 per cent of the cost of the product or service is firmed up by the time the conceptual design has been completed. By the time the system definition is completed, 80 percent of the cost is finalized and 90 percent of the cost is firmed up before production. For example, the geometrical shape of a part or assembly determines the subsequent manufacturing processes by which it may be manufactured. This, in turn, limits the materials to just those few that are suitable for those processes.
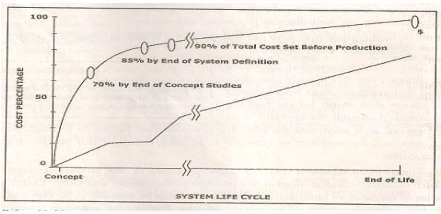
Figure 3.2 Locking of Product Costs and Design
The impact of the design process on costs shows how costs are firmed up and it will be seen that the majority of cost reduction opportunities are lost prior to the actual production.”
These decisions are difficult because there is no guarantee for success. Two out of three new products fail after launch. Therefore, the key observations on product development recommended by the expert committee on Bridging Design and Manufacturing set up by the National Research Council, U.S.A., after a series of hearings from industry, in February 2003, should be of great interest:
- Continue the early collaborative exploration of the lifecycle, including manufacturing, logistics, time-phased requirements, and technology insertion.
- Perform assessments based on modeling and simulation early in the development cycle alternative system designs built, tested and operated in the computer before critical decisions are locked in and manufacturing begins.
- Wait to develop designs until requirements are understood.
- Requirements are the key. Balance them early!
- Once the design is drawn, the cost and weight are set.
- No amount of analysis can help a bad design get stronger or cheaper.
- Remember that 80percent of a product’s cost is determined by the number of parts, assembly technique, manufacturing processes, tooling approach, materials and tolerances.
Measuring Costs and Identifying Waste: Operations Management is interested in enhancing value. Cost reductions often translate directly into increases in value if they out weight changes in performance. Like the other inputs to the value equation, the costs are composed of a variety of different elements. For example, the costs relevant to the purchase decision could include one or more of several categories.
- Acquisition cost : The purchase price of a car, for instance.
- Repair costs : The cost of replacing a broken part.
- Maintenance costs : The cost of oil changes and tune-ups.
- Operating costs : The cost of gas & tyres.
- Salvage/resale costs : The cost recovered on selling a car.
- Disposal costs : The cost of disposing of a wrecked car.
Furthermore, managers can breakdown cost to express them quantitatively or qualitatively. A major problem in much corporate accounting system has been that the overhead costs are precisely applied to the products that they support. Effective performance measurement requires such products to bear its fair share of all costs incurred to create, make, sell, and service. Direct costs pose no major problem; managers simply record all the labor, material and other resources used by a product. However, assigning overhead costs become more difficult. Unlike direct costs, these costs seldom vary with changes in output. “Marketers know well that people like to buy things cheaply, but do not like cheap things,”
This statement describes both major attractions and the problem of emphasizing cost vas the firm’s major source of value. Customers want at least the same performance for lower cost; not simply less for less. A cost driven approach to value treats performance as a given and focuses on reducing cost. For example, this approach has been successful in Bajaj Auto. It has been successful in inculcating a concept in its workforce of lower costs means better quality. The firm should be able to measure customer satisfaction, to evaluate customer service costs.
It is cheaper to keep a good customer happy than to win one of your competitor’s good customer. Customer satisfaction can be measured by the use of the concept of lifetime value of a customer, which is an estimate of the stream of income a firm can expect to receive from a satisfied good customer. This is a useful concept in that, like value, it forces all within a system to focus on keeping customers satisfied and coming back. Operations management system must examine both the product it is selling and the processes it uses to deliver and service the product, to achieve this objective. It should identify product features that customers do not value highly or processes or parts of processes that contribute unnecessarily to cost. Activities that do not add value are waste, if they don’t support activities. Unnecessary product features they don’t add value are waste these need to be eliminated.
Using a waste reduction approach helps reduce the excessive emphasis on cost reduction. Cost reduction programs that ignore the negative effects on lead time, flexibility and quality will not enhance a firm’s competitiveness in the long run. For example, affirm that uses cheaper material that reduce the quality to lower costs may save money in the short ten. However, over the long haul, they reduce the ability of the firm to deliver a product consumer value. They may buy the product once, but not thereafter.
New Product Development and Economic Cost: The design of a system or product involves the principal task of evolving a form that can support the functions required by the system or product. The design must be optimized with regard to cost, technical requirements and value consideration of the customer. The challenge is to use resources wisely. This has given rise to a number of techniques and created a number of tools that are being practiced in industries , focused to provide the greatest value of the product to the consumers and optimize the production process and capacity, Of the various techniques developed , the best known are the following;
Design for Manufacturability /Design for ‘X’
Value Engineering /Value Analysis
Both these techniques have been discussed elsewhere in this course pack, but to make the concept clear in the new product development both the techniques are discussed here;
Design for Manufacturability (DFM)
- DFM is the process of designing a product for efficient production while maintaining the higher level of quality
- It is intended to avoid more complex and expensive product design to simplify assembly operations.
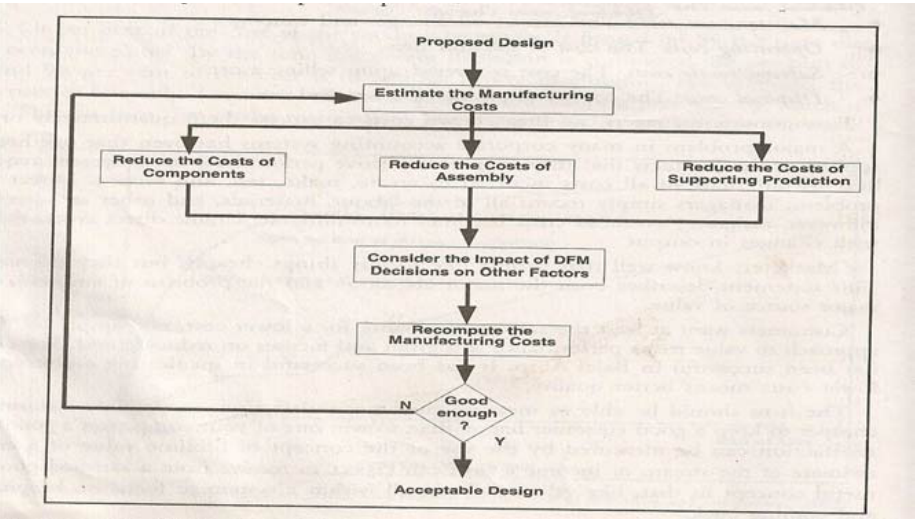
Figure 3.3: The DFM process
The flow chart for DLM process is given in Figure 3.3. Some guidelines to determine whether the design is good enough are given below;
- Minimize the number of parts.
- Develop a modular design
- Design parts for multi use
- Avoid separate fasteners
- Eliminate adjustments
- Design for top down s\assembly
- Design for minimum handling
- Avoid tools
- Minimize subassemblies
- Use standard parts when possible
- Simplify operations
- Design for efficient and adequate testing
- Use repeatable and understood processes.
- Analyze failures
- Rigorously assess value
DFM is a team based approach that involves everyone associated with the development process. DFX—Design for ‘X ‘DFX is a special case of DFM, where a certain area say X is selected for attention. Improvement in ‘X’ are proposed after detailed analysis of the process by a team of cross functional experts. The performance measures are established and items are identified that will simplify the process and at the same time provide value to the customer.
An example is of Escorts Ltd. a company that was making heating elements for electrical kettles. The holder that screwed on the element to the kettle was made of casting. The casting had to be pre-machined, sized, cut and turned before it was ready for threading. The technical requirements were not critical, as the function of the part was to protect the consumer from the contact with electrical contacts and guide the external socket to the corresponding part of the heating element. Standard tube was found that met the dimensional requirements for the component. This greatly simplified the process, avoided a number of operations. Reduced the number of parts, and also reduced costs
Value Analysis / Value Engineering: What provides value to the product? A way to consider the customer’s view in designing products is by analyzing the value they see in the end product. It is important that the value is designed into the products. Value Engineering is an organized creative technique directed at analyzing for the functions of a product, service or system with all the requirements, which comprises its value. Such as performance, reliability, maintainability, appearance etc. Value, in general, is defined as the ratio of the function and cost. It reflects what the product, service or system accomplishes and at what cost. Thus;
Value = Function / Cost
Where ‘function’ is expressed as units of performance and ‘Cost’ is expressed as a monetary unit. Value engineering is used as a generic term and generally includes value analysis. The purpose of both value analyses (VA) and value engineering (VE) is to simplify products and processes. VA specifically deals with products already in production and is a cost reduction technique. It is used to analyze product specifications as shown in production documents to achieve similar or better performance at a lower cost while maintaining all functional requirements defined by the customer. Value engineering is performed before the production stage and is considered a cost avoidance method.
Value engineering starts with the classification and identification of a product, service or system. The function of a product, service or system is identified. Each function is evaluated and compared. The process involved in value engineering is as follows:
Step 1: Identify each of the functions of the product or service and list them down.
Step 2: Give a weight to the importance of each function, such that the total of the weights come to step 1, rearrange the functions on the basis of their importance.
Step 3: Identify each of the components in the product or service and list its function
Step 4: The functions of components have to be related to the product and the function of the product. Each component will have to give weight to show how it contributes to the function of the product or service. There may be some components that have more than one function. This should be taken into account
Step 5: Identify the cost of each component and convert it to a weight corresponding to the total cost so that the total of the weights does not exceed ‘1’, just as in step 2.
Step 6: Compare the weights of the functions with the weights of the costs of each component
Step 7: Identify those components where the ratio of Function / Cost is low.
The VA/VE analysis approach involves taking these identified components and brainstorming with such question as;
- Does the item have any design features that are not necessary?
- Can two or more parts be combined into one?
- How can we cut down the weight?
- Are there nonstandard parts that can be eliminated?