A core definition of total quality management (TQM) describes a management approach to long–term success through customer satisfaction. In a TQM effort, all member of an organization participate in improving processes, products, services, and the culture in which they work.
Early TQM frameworks
In the early 1980s when organizations in the West started to be seriously interested in quality and its management there were many attempts to construct lists and frameworks to help this process.
In the West the famous American ‘gurus’ of quality management, such as W. Edwards Deming, Joseph M. Juran and Philip B. Crosby, started to try to make sense of the labyrinth of issues involved, including the tremendous competitive performance of Japan’s manufacturing industry. Deming and Juran had contributed to building Japan’s success in the 1950s and 1960s and it was appropriate that they should set down their ideas for how organizations could achieve success.
Deming had 14 points to help management as follows:
- Create constancy of purpose towards improvement of product and service.
- Adopt the new philosophy. We can no longer live with commonly accepted levels of delays, mistakes, defective workmanship.
- Cease dependence on mass inspection. Require instead statistical evidence that quality is built in.
- End the practice of awarding business on the basis of price tag.
- Find problems. It is management’s job to work continually on the system.
- Institute modern methods of training on the job.
- Institute modern methods of supervision of production workers. The responsibility of foremen must be changed from numbers to quality.
- Drive out fear, so that everyone may work effectively for the company.
- Break down barriers between departments.
- Eliminate numerical goals, posters, and slogans for the workforce asking for new levels of productivity without providing methods.
- Eliminate work standards that prescribe numerical quotas.
- Remove barriers that stand between the hourly worker and his right to pride of workmanship.
- Models and frameworks for total quality management
- Institute a vigorous program of education and retraining.
- Create a structure in top management that will push every day on the above 13 points.
Juran’s ten steps to quality improvement were:
- Build awareness of the need and opportunity for improvement.
- Set goals for improvement.
- Organize to reach the goals (establish a quality council, identify problems, select projects, appoint teams, designate facilitators).
- Provide training.
- Carry out projects to solve problems.
- Report progress.
- Give recognition.
- Communicate results.
- Keep score.
- Maintain momentum by making annual improvement part of the regular systems and processes of the company.
Phil Crosby, who spent time as Quality Director of ITT, had four absolutes:
- Definition – conformance to requirements.
- System – prevention.
- Performance standard – zero defects.
- Measurement – price of non-conformance.
He also offered management 14 steps to improvement:
- Make it clear that management is committed to quality.
- Form quality improvement teams with representatives from each department.
- Determine where current and potential quality problems lie.
- Evaluate the cost of quality and explain its use as a management tool.
- Raise the quality awareness and personal concern of all employees.
- Take actions to correct problems identified through previous steps.
- Establish a committee for the zero defects program.
- Train supervisors to actively carry out their part of the quality improvement program.
- Hold a ‘zero defects day’ to let all employees realize that there has been a change.
- Encourage individuals to establish improvement goals for themselves and their groups.
- Encourage employees to communicate to management the obstacles they face in attaining their improvement goals.
- Recognize and appreciate those who participate.
- Establish quality councils to communicate on a regular basis.
- Do it all over again to emphasize that the quality improvement program never ends.
A comparison
Our understanding of ‘total quality management’ developed through the 1980s. One way to compare directly the various approaches of the three American gurus is in table below, which shows the differences and similarities against different factors.
The American quality gurus compared
Crosby | Deming | Juran | ||
Definition of quality | Conformance to requirements | A predictable degree of uniformity and dependability at low cost and suited to the market | Fitness for use | |
Degree of senior management responsibility | Responsible for quality | Responsible for 94% of quality problems | Less than 20% of quality problems are due to workers | |
Performance standard/ motivation | Zero defects | Quality has many scales. Use statistics to measure performance in all areas. Critical of zero defects. | Avoid campaigns to do perfect work | |
General approach | Prevention, not inspection | Reduce variability by continuous improvement. Cease mass inspection | General management approach to quality –especially ‘human’ elements | |
Structure | Fourteen steps to quality improvement | Fourteen points for management | Ten steps to quality improvement | |
Statistical process control (SPC) | Rejects statistically acceptable levels of quality | Statistical methods of quality control must be used | Recommends SPLC but warns that it can lead to too- driven approach | |
Improvement basis | A ‘process’, not a program. Improvement goals | Continuous to reduce variation. Eliminate goals without methods | Project-by-project team approach. Set goals | |
Teamwork | Quality improvement teams. Quality councils | Quality improvement teams. Quality councils | Team and quality circle approach | |
Costs of quality | Cost of non-conformance. Quality is free | No optimum – continuous improvement | Quality is not free – there is an optimum | |
Purchasing and goods received | State requirements. Supplier is extension of business. Most faults due to purchasers themselves | Inspection too late – allows defects to enter system through AQLs. Statistical evidence and control charts required | Problems are complex. Carry out formal surveys | |
Vendor rating | Yes and buyers. Quality audits useless | No – critical of most systems | Yes, but help supplier improve | |
Single sources of supply | Yes | No – can neglect to sharpen competitive edge | ||
TQM approaches to the direction, policies and strategies of the business or organization. These ideas were captured in a basic framework – the TQM model which was widely promoted in the UK through the activities of the Department of Trade and Industry (DTI) programs. The customer/supplier or ‘quality chains’ and the processes that lived within them was the core of this TQM model.
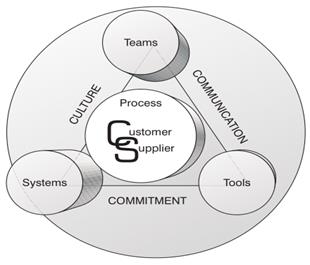
This simple framework was useful and it helped groups of senior managers throughout the world get started with TQM. The key was to integrate the TQM activities, based on the framework, into the business or organization strategy
The four Ps and three Cs of TQM
Processes are the key to delivering quality of products and services to customers. Processes are a key linkage between the enablers of planning (leadership driving policy and strategy, partnerships and resources), through people into the performance (measured by people, society, customers, and key outcomes).
Any business venture should go through the “3Cs and 4Ps” exercise. It is incredibly valuable and insightful exercise. It may seem simple, but the “3Cs and 4Ps” exercise really allows you to think about a business venture in a structured way. Once you force yourself to really go through this exercise, you’ll realize how much you didn’t know about the business idea you had in mind.
The 3 Cs are – Company, Customer and Competition. The 4 Ps are Product, Price, Promotion and Place (distribution). They are explained as
Company – You first need to think about what type of company you plan to operate. What will it look like? What values will you aspire to? What is your company’s mission? Will it be a corporation, an LLC or a sole proprietorship? Where will it be located? What will you name it? Basically, you need to think about anything that that defines the type of company you plan to run.
Customer – Next, you need to think about your target audience. What type of customer will most likely be interested in your product or service? What are the demographics? Where will they live? To what income brackets will they belong?
Competition – Last but not least, you really need to consider your competition. Believe me, if you leave this part out, you’ll get eaten alive. There’s a famous poker saying that sums this up nicely. It basically says that if you don’t know who the sucker is on the table, then it’s probably you. The same holds true in the business world. You need to know your competition very well. You need to learn how they operate, what marketing tactics they use, who their supplier’s are, what financial position they are in and anything else you can dig up.
Product – This is where you define your product or service. If you’re selling something, then define exactly what it will do. But equally important, you need to define exactly what it won’t do. What will it look like? How will it be packaged? Will it need special certifications such as a UL listing?
If you’re offering a service, then the same applies. Your service needs to be really well defined. You need to clearly articulate what you do offer and what you don’t offer. If this is not clear, then you may fall victim to “scope creep” where customers will keep expanding the scope of what you had originally promised them.
Price – How will you price your product or service? If you are selling a product, what price can your target market pay? Do you have any pricing power? That is, if you’re a famous coffee house, then you may be able to sell coffee at higher prices than a local coffee shop.
If you’re offering a service, how will you charge for your work? Will it be hourly, fixed bid or some other combination? You will look much more professional if you can clearly define your services and your prices to a customer. You don’t want to look like you’re winging it during a sales call.
Promotion – How will you market your product? What advertising channels will you use? What social marketing strategies will you deploy? Will you consider pay-per-click advertising? Will you attend any trade shows? What is your marketing budget? What return on investment (ROI) do you want to achieve from the money you plan to invest in marketing?
Place (Distribution) – How will you store and distribute your product? Basically, you need to figure out how you’re going to get your product from your supplier to your warehouse and then to your customer. What shipping methods will these steps require? Will you have a warehouse or will you use a public warehouse? Perhaps you plan to have everything drop-shipped for you so you don’t have to carry any inventory. What distribution channels will you use? Will you sell through distributors or are you planning on sell direct to your customers?

Performance is achieved, using a business excellence approach, and by planning the involvement of people in the improvement of processes. This has to include:
- Planning – the development and deployment of policies and strategies; setting up appropriate partnerships and resources; and designing in quality.
- Performance – establishing a performance measure framework – a ‘balanced scorecard’ for the organization; carrying out self-assessment, audits, reviews and benchmarking.
- Processes – understanding, management, design and redesign; quality management systems; continuous improvement.
- People – managing the human resources; culture change; teamwork; communications; innovation and learning.
The Primary Elements of TQM
- Customer-focused: The customer ultimately determines the level of quality. No matter what an organization does to foster quality improvement—training employees, integrating quality into the design process, upgrading computers or software, or buying new measuring tools—the customer determines whether the efforts were worthwhile.
- Total employee involvement: All employees participate in working toward common goals. Total employee commitment can only be obtained after fear has been driven from the workplace, when empowerment has occurred, and management has provided the proper environment.
- Process-centred: A fundamental part of TQM is a focus on process thinking. A process is a series of steps that take inputs from suppliers (internal or external) and transforms them into outputs that are delivered to customers (again, either internal or external). The steps required to carry out the process are defined, and performance measures are continuously monitored in order to detect unexpected variation.
- Integrated system: Although an organization may consist of many different functional specialties often organized into vertically structured departments, it is the horizontal processes interconnecting these functions that are the focus of TQM.
- Everyone must understand the vision, mission, and guiding principles as well as the quality policies, objectives, and critical processes of the organization. Business performance must be monitored and communicated continuously.
- Every organization has a unique work culture, and it is virtually impossible to achieve excellence in its products and services unless a good quality culture has been fostered. Thus, an integrated system connects business improvement elements in an attempt to continually improve and exceed the expectations of customers, employees, and other stakeholders.
- Strategic and systematic approach: This process, called strategic planning or strategic management, includes the formulation of a strategic plan that integrates quality as a core component.
- Continual improvement: Continual improvement drives an organization to be both analytical and creative in finding ways to become more competitive and more effective at meeting stakeholder expectations.
- Fact-based decision making: TQM requires that an organization continually collect and analyze data in order to improve decision making accuracy, achieve consensus, and allow prediction based on past history.
- Communication: During times of organizational change, as well as part of day-to-day operation, effective communications plays a large part in maintaining morale and in motivating employees at all levels. Communications involve strategies, method, and timeliness.
Today merely SQA is not enough to achieve the quality of software product demanded by the customer. One must apply the TQM methods to the entire software development organization, not just the development processes themselves. Such practice is known as “software total quality management” (STQM). The STQM is a fundamental cultural change from the traditional quality perspective to an organizational philosophy that incorporates quality improvements in every aspect of the organization. Therefore, SQA provides a methodology to assure quality while STQM provides a framework to continually improve it. By instilling TQM’s continuous improvement strategy in every aspect of the software development, an organization never settles for the level that it has reached, no matter how good the product, continually challenging the status quo for new concepts and strategies helps to furnish the software industry with continually better products.