In today’s increasingly dynamic and turbulent world, one where the supply chain plays an increasingly more important role, numerous events occur each day that threaten to disrupt operations and jeopardize the ability to perform effectively and efficiently. These events include natural and man-made disasters such as equipment failures, fires, labor disputes, supplier defaults, political instability, and terrorist attacks.
Each can have devastating effects on a firm. Such disruptions reinforce the insights that not only can supply chain disruptions affect operations; they often result in financial damage well beyond the immediate operational impacts.
One approach to dealing with disruptions is the development of supply chain systems that are resilient. However, this notion of resilience, which is at the heart of so much of our current thinking about supply chain risk and management, is often not well-defined and subject to a great deal of confusion.
While many consultants, researchers, and managers agree on the importance of supply chain resilience, there is less agreement on what it is, how it operates, and how and where to invest to mitigate risk and recover from disruptions – to shape and influence resiliency. This article draws on the expertise of the authors, prior research, anecdotes, and recent events to define and further explore this concept.
Supply Chain Resilience Defined
The concept of resilience traces its roots back to the work of C.S. Holling, an ecologist who first noted the characteristics of a resilient ecological system in 1973. Since then, the notion of resilience has been applied to fields as diverse as psychology, systems thinking, disaster management, and more recently, supply chain management.
For some, resilience is a reactive capability that occurs after a disruption or shock has taken place. Others see resilience as more proactive efforts toward helping the firm prepare for a disruption. In light of these divergent observations, it is not surprising that there is confusion surrounding this key concept.
To the authors, supply chain resilience is “the ability of a supply chain to both resist disruptions and recover operational capability after disruptions occur.“ As mentioned above, viewed from this perspective, resilience consists of two critical but complementary system components: the capacity for resistance and the capacity for recovery. Let’s look more closely at those elements:
- Resistance capacity is the ability of a system to minimize the impact of a disruption by evading it entirely (avoidance) or by minimizing the time between disruption onset and the start of recovery from that disruption (containment).
- Recovery capacity is the ability of a system to return to functionality once a disruption has occurred. The process of system recovery is characterized by a (hopefully brief) stabilization phase after which a return to a steady state of performance can be pursued. The final achieved steady-state performance may or may not reacquire original performance levels, and is dependent on many disruption and competitor factors.
Exhibit 1 portrays the impact of a disruption over time, from the moment that the disruption originates somewhere in the system (at time TD) until the system has returned to some form of steady-state (TR).
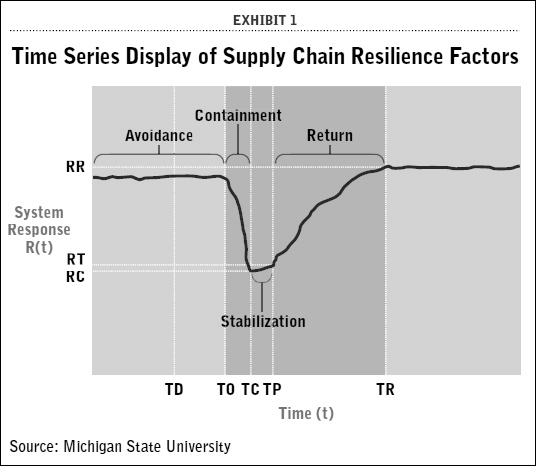
In this illustration, we can identify the four stages of resilience, which are avoidance, containment, stabilization, and return.
Exhibit 1 also defines the sequence of events, or time series signature, in a disruption as well as the typical system response for a typical disruption.
Those would include inventory levels, cash flow, and asset availability to name just a few.
Two variables are central to understanding this illustration, T and R. T denotes the time at which a specific event occurs while R denotes the relative impact of the event as measured in terms of dollars, units lost, change in fill rate, or some other metric that is important to a firm’s performance. Taken together, time (T) and response (R) are important because they define inflection points in the time series signature where a change in state can be observed.
The differences between the variance events listed in Exhibit 1 identify traits of interest to management. For example, TO-TD, or the gap between the moment at which the disruption took place (TD) and the moment that that disruption began to affect the firm (TO), tells management how long it will take for the firm’s performance to be impacted; this time interval also identifies the maximum amount of early warning that the firm can count on to begin taking action to minimize the negative effects of the disruption.
When supply chain disruptions and their traits are observed, it is interesting to compare how the policies and strategies used by the firm can affect the various events identified in Exhibit 1 and Exhibit 2 in terms of both time and impact.
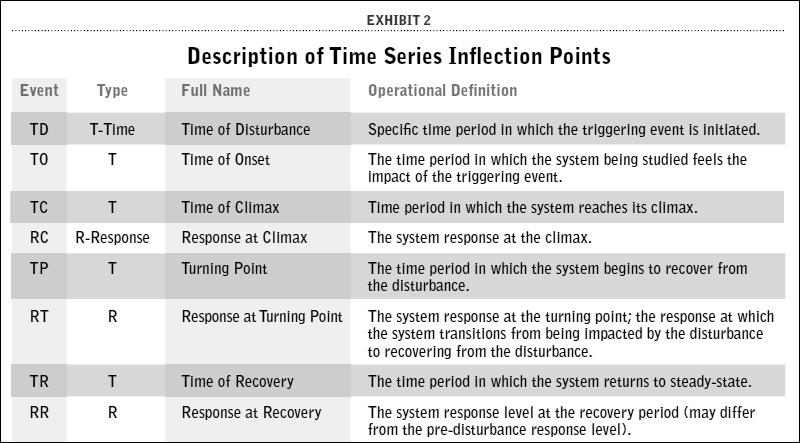
Once recovery is complete, firms often reflect upon their experience to document appropriate lessons and identify system refinements to reduce future risks. This completes a supply chain resilience cycle of: Avoidance ➝ Containment ➝ Stabilization ➝ Return ➝ Review ➝ Avoidance.
Resistance and Recovery
To illustrate the concepts of resistance and recovery, consider the 2011 Japanese earthquake and subsequent tsunami. In the wake of these twin disasters, it quickly became apparent that suppliers for both Nissan and Toyota facilities lacked adequate resistance capabilities when faced with an event of this magnitude.
Nissan, however, exhibited significant capacity for recovery. It resumed operations and regained lost market share more quickly than Toyota. Nissan was able to achieve this by accessing alternative suppliers, while Toyota stayed with existing suppliers.
Nissan’s supply chain thus provided a differential advantage over that of Toyota, despite their highly similar supply chain networks and locations relative to the earthquake/tsunami. Although full avoidance of a supply chain disruption is an admirable goal, accidents and disruptions will still occur. Instead, firms need to develop the ability to deal directly with events that are unavoidable.
Exhibit 3 below illustrates an alternate view of supply chain resilience, which characterizes resilience into the capacities for resistance and recovery along with the respective phases: avoidance, containment, stabilization, and return.
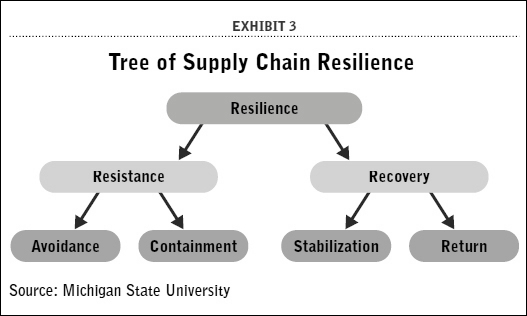
While firms would clearly prefer to possess a high capacity for both resistance and recovery, it is more likely that firms will have a mix of these qualities. In particular, given resource constraints and competitive factors, firms may need to choose where it is best for them to invest limited resources. That is, the firm may not be able to afford to invest in both improving resistance and recovery.
With this in mind, the resistance and recovery matrix (Exhibit 4) characterizes possible positions that a firm might find itself in with regard to varied levels of these attributes.
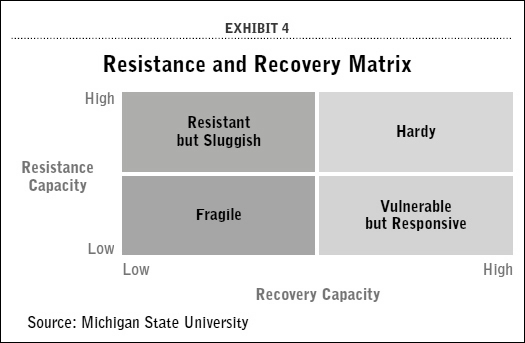
Supply chains exhibiting low capacities for both resistance and recovery would have low resistance: They would experience nearly every disruption while also having slow and weak recoveries as a result of a lack of ability to recover effectively. These supply chains are “fragile.”
Their long-term prognosis is very poor since they likely will not last and won’t grow, unless protected by unique market or regulatory conditions. For example, some industries in Sri Lanka over the past decade have suffered multiple disruptions due to civil war, theft, power outages, monsoon rains, and flooding.
Firms in these industries have survived, however, because effective competition does not exist or because competition chooses not to compete in such market or regulatory environments. As a result, fragile supply chains that provide poor quality customer service persist because the customer base is conditioned to accept low customer service.
In contrast to fragile supply chains with low resistance, those that exhibit high levels of resistance are able to alleviate potential risks more easily. When they also possess the capacity for effective recovery, they quickly rebound from those events that are unavoidable. Such supply chains are classified as “hardy.”
General Motors (GM) is an example of a hardy supply chain. According to reports, GM constantly monitors its supply chain to minimize disruptions and, when necessary, to facilitate recovery. That was the case during the Thailand floods of 2011.
Despite having plants and suppliers in the area, GM experienced limited disruptions to the flow of materials because it was able to resist the onset of problems better than its competitors. When disruptions became unavoidable, GM was robust enough to quickly work through them and recover.
Somewhere between fragile and hardy there exists two middle positions. Supply chains that are characterized by an ability to adequately minimize disruptions, but an insufficient ability to quickly recover, are ”resistant but sluggish.”
These supply chains exhibit high levels of resistance, but if the system is ultimately disrupted, the supply chain impacts are negative. These supply chains are like a heavyweight boxer who is able to take significant attacks, but who is knocked down for a significant amount of time if pushed too far.
The use of the term “sluggish” in this case does not imply ineptitude or lack of desire to restore operation, but rather insufficient capability to do so. This may arise, for example, from lack of recovery training as resources are focused toward resistance instead. The chemical industry is a case in point.
Although these firms develop relatively strong defenses against a disruption, if a spill or other event occurs it may lead to serious consequences that built-in recovery capabilities might not be sufficient to address quickly due to the nature of such spills.
The other middle position is characterized by supply chains that exhibit low resistance to disruptive events, but quickly overcome their impact. These supply chains are termed “vulnerable but responsive.” Similar to an electrical fuse in a building, these are easily knocked offline, but they have the capacity to quickly recover.