HALT tests as discussed earlier, is a stress testing methodology for accelerating product reliability. HALT testing is currently in use by most major manufacturing organizations to improve product reliability in a variety of industries, including electronics, computer, medical and military.
It is a reliability test program used in the early stages of product development. HALT testing grew out of the step-stress or overstress testing programs. It involves increasing stress on a unit until failure occurs.
HALT subjects a product to a series of overstresses, effectively forcing product weak links to emerge by accelerating fatigue. Unlike traditional single axis vibration test methods or thermal only methods, HALT requires specialized equipment to render the required stresses – random six-degree-of-freedom vibration and rapid thermal change rates – in the combined environment necessary to drive out latent failure modes.
Stresses are applied in a controlled, incremental fashion while the unit under test is continuously monitored for failures. Once the weaknesses of the product are uncovered and corrective actions taken, the limits of the product are clearly understood and the operating margins have been extended as far as possible. Result? A much more mature product can be introduced much more quickly with a higher degree of reliability.
In HALT, every stimulus of potential value (temperature, all-axis vibration, humidity, UV, radiation, etc.) can be used under accelerated test conditions during the development phase of a product to find the weak links in the design and fabrication processes. Accelerated stresses in combination (e.g. high-temperature ramp rates and all-axis vibration levels together) are necessary to compress or minimize the time to failure.
HALT process can be split in three phases as-
- Pre-HALT – Reliability engineers prepare to execute the HALT. Resource allocation, availability of fixtures, test suites is outlined and finalized. Meeting are also conducted by all stakeholders so as to finalize HALT
- HALT – HALT is conducted as per plans finalized during the pre-HALT phase. Tests are monitored and results logged for review and analysis.
- Post-HALT – HALT reports are distributed and meeting for review and root cause analysis.
Highly accelerated stress screening (HASS) is an extension of the HALT principle, that makes use of very high combined stresses. No ‘guidelines’ are published to recommend particular stresses and durations. Instead, the stresses, cycles and durations are determined separately for each product by applying HALT during development. HALT shows up the product weak points, which are then strengthened as far as practicable
The stresses that are then applied during HASS are higher than the operating limit, and extend into the lower tail of the distribution of the permanent failure limit. The stresses applied in HASS, are designed to precipitate failures which would otherwise occur in service.
The determination of this stress–time combination cannot be exact, because of the uncertainty inherent in the distribution of strength. However, by exploring the product’s behaviour on test, we can determine appropriate stress levels and durations. The durations will be short, since the stress application rates are very high and there is usually no benefit to be gained by, operating at constant high or low temperatures for longer than it takes for them to stabilize.
When stresses above the operating limit are applied, it will not be possible to perform functional tests. Therefore the stresses must then be reduced to levels below the operating limit. The functional test will then show which items have been caused to fail, and which have survived. The screening process is therefore in two stages: the precipitation screen followed by the detection screen, as shown in figure.
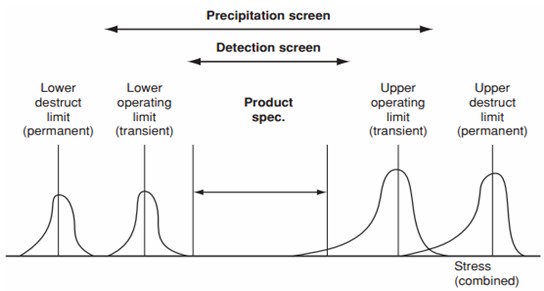