A principle is a concept or value that is a guide for behavior or evaluation. In law, it is a rule that has to be, or usually is to be followed, or can be desirably followed.
Six Sigma is also based on core principles which are centered around customer satisfaction and are discussed below.
Customer Focus
Six Sigma is about improving quality. The first step in that process is defining what “quality” means, from the perspective of the people whose opinions matter most: the customers. A business needs to measure quality the same way its customers do. By focusing on the customer, a business can improve its products’ quality.
Identify Root Causes
To correctly identify a root cause, a complete understanding of the process is necessary. This does not mean just understanding how a process was designed to work. It means understanding how the process is actually working. To accomplish this you need to:
- Have clearly defined goals for data collection
- Identify the data that needs to be collected
- Have a defined reason for the data being collected
- Establish what insights are expected from the data
- Ensure accurate communication by clearly defining terms
- Ensure that measurements are accurate and repeatable
- Establish a standardized data collection system/process
Once the data is collected, determine whether it is providing the required insight and is meeting the goals that were established. If not, refine the data collection plan and collect additional information.
Six Sigma data collection involves interviewing people, making observations, and asking questions until the answers are found. Ask the questions such as:
- “Why do we do things this way?”
- “What would make your job easier?”
- “What things do you do that seem to be a waste of time?”
Once the data is collected, use it to look for ways to improve or optimize the process by identifying the root cause of variation.
Eliminate Variation
After identifying root causes, make changes to the process that will eliminate variation, and thus eliminate defects from the process. Also look for ways to eliminate steps that do not add value for the customer. This will eliminate waste.
Be proactive in identifying variation and eliminating it. Don’t wait for signs of variation to become obvious. Collect data, talk with people, and study the data to find variations in the process that may have become accepted because “that’s the way we’ve always done things.”
Teamwork
Six Sigma involves teams and leaders who take responsibility for the Six Sigma processes. The people on the teams need to be trained in Six Sigma’s methods, including the Six Sigma measurement methods and improvement tools that will be used. In addition, they need communication skills so that they can involve, serve, and communicate clearly with both coworkers and customers.
Putting together teams that have members with a variety of skills and backgrounds related to a process will help the team spot variations. For a manufacturing process for example, people from operations, maintenance, engineering, and purchasing should be included.
Be Flexible and Thorough
Six Sigma requires flexibility in many ways. The business’s management system needs to accept positive changes as well as empower change. Employees should be motivated to adapt to change. In the beginning, the benefits of the changes should be made clear to workers. This will help to create an environment where change is more readily accepted.
Key to Six Sigma is the ability to change or adapt procedures as needed. In short, the process required for change should not be so complex that workers and management would rather work with a broken process than fix it.
Six Sigma also requires problem-solving to be thorough. Making sure to understand every aspect of a process—the steps, people, and departments involved—will help to ensure that any new or updated process works.
Clear, Effective Visual Communications
Six Sigma involves change, and change requires effective on-going communication. Old habits need to be broken and new habits established. Graphic Products offers an array of supplies that can help make Six Sigma successful in your business including printers and labels.
Other lean methodologies can also be used to support Six Sigma. Lean tools like Kaizen can be used to help create an environment where changes are accepted and business practices are continuously improved upon, while 5S can be used to make problems easier to spot as well as create standardized processes.
The Six Sigma methodology is conceptually based a five phase project. Each phase has a specific purpose and specific tools and techniques which aid in achieving the phase objectives as well as lead the Six Sigma professional to significant conclusions. The 5 Phases of the Six Sigma Methodology is called as DMAIC or the Define Phase, Measure Phase, Analyze Phase, Improve Phase and the Control Phase. All the five phases are discussed below.
Define Phase – The goal of Define is to establish the projects foundation and is the most important aspect of the Six Sigma project. Projects start with a current state challenge which is articulated in a quantifiable manner as well as the goal to achieve, is also determined.
After specification of problems and goals the remaining tasks of valuation, team, scope, project planning, time line, stakeholders, VOC/ VOB etc. are to be completed. Various tools used by the Define Phase are
- Project Charter
- Problem Statement
- Business Case
- Objective
- High level time line
- Project Scope
- Project Team
- Stakeholder Assessment
- Pareto Charts
- SIPOC
- VOC/VOB and CTQ’s
- High Level Process Map
Measure Phase – In this phase baseline information is gathered about the process or product and achieve the following objectives
- Gather All possible x’s
- Analyze measurement system and Data Collection Requirements
- Validate Assumptions and Improvement Goals
- Determine COPQ
- Refine Process Understanding
- Determine Process Capability
- Process Stability
This Phase involves the usage of following tools
- Process Maps, Value Stream Mapping
- Failure Modes and Effects Analysis (FMEA)
- Cause and Effect Diagram
- XY Matrix
- Basic Control Charts
- Six Sigma Statistics
- Basic Statistics
- Descriptive Statistics
- Normal Distributions
- Graphical Analysis
- Measurement Systems Analysis
- Variable Gage R&R
- Attribute Gage R&R
- Gage Linearity and Accuracy
- Gage Stability
- Process Capability (Cpk, Ppk) and Sigma
- Data collection plan
Analyze Phase – It entails establishing verified drivers by using statistics and higher order analytics to discover the fact-based relationship between the process performance and the x’s or the root causes or drivers of improvement effort. Thus, resulting in establishment of hypothesis for improvements. This phase establishes transfer function Y=f(x) and validates list of critical X’s and their impacts. The analyze phase also results in a beta improvement plan like pilot plan. This phase utilizes various tools like
- Hypothesis Testing
- Simple Linear Regression
- Multiple Regression
Improve Phase – This phase is aimed only on making the improvement like improving the designing, testing and implementing of the solution. It involves enlisting statistically proven results from active study or pilot, creating the improvement plan, updating the stakeholder assessment, revising the business case with investment ROI, risk assessment and adding new process capability.
This phase uses tools like
- Design of Experiment (DOE)
- Implementation Plan
- Change Plan
- Communication Plan
Control Phase – It is the last phases of the Six Sigma methodology which establishes automated and managed mechanisms to maintain and sustain improvements in the process. A successful control plan also results in a reaction and mitigation plan with an accountability structure. It involves tools like control plan, training plans, poka-yoke and/or audit plans. The Six Sigma methodology is a complete system with tools and techniques built-in which ensures the Six Sigma practitioner to achieve success.
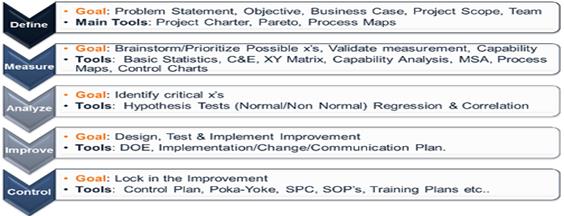