Standardization or standardisation is the process of developing and implementing technical standards. Standardization can help to maximize compatibility, interoperability, safety, repeatability, or quality. It can also facilitate commoditization of formerly custom processes.
Standards can be:
- de facto standards which means they are followed by informal convention or dominant usage.
- de jure standards which are part of legally binding contracts, laws or regulations.
- Voluntary standards which are published and available for people to consider for use.
The existence of a published standard does not necessarily imply that it is useful or correct. Just because an item is stamped with a standard number does not, by itself, indicate that the item is fit for any particular use. The people who use the item or service (engineers, trade unions, etc.) or specify it (building codes, government, industry, etc.) have the responsibility to consider the available standards, specify the correct one, enforce compliance, and use the item correctly: validation and verification.
Standardization is implemented greatly when companies release new products to market. Compatibility is important for products to be successful; this allows consumers to use their new items along with what they already own.
Standardization supports the fundamental precepts of build-to-order and mass customization: All parts must be available at all points of use, not just “somewhere in the plant,” which eliminates the setup to find, load, or kit parts. As a stand-alone program, standardization can reduce cost and improve flexibility.
Standardization makes it easier for parts to be pulled into assembly (instead of ordering and waiting) by reducing the number of part types to the point where the remaining few standard parts can receive the focus to arrange demand-pull just-in-time deliveries. Fewer types of parts ordered in larger quantities reduces part cost and material overhead cost.
Parts Selection
Using same parts is multiple finished good is done by parts standardization which is usually the norm in the automotive industry amongst various similar automobile models differing on size, are also called as parallel models. Parts standardization not only reduces cost but organization can allocate more resources to improve reliability of the component. Similarly, parts reduction effort focuses on reducing number of components needed to perform a function.
The raw as possible (RAP) principle is applied, which focuses on keeping a component in raw form so that it usable in different assemblies as per requirement. RAP is illustrated in figure below.
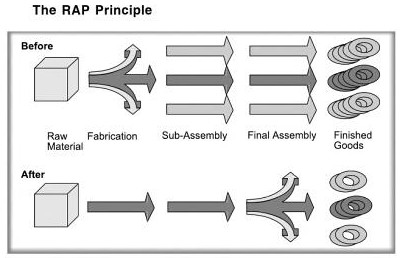
Material Selection
Technologies continue to evolve, improve and provide more options to design teams. Some of these changes optimize cost, performance or quality to meet specific needs in the market. Design teams need to select materials to meet many competing requirements; reliability is often a difficult criterion to judge. The material performance may be dependant on the design, interactions with other nearby materials or manufacturing processes, or the intended use environment. Vendors are often unable to fully judge the suitability of materials in a specific situation. Distribution models allow variation in materials during design phase so as produce products which are tolerant to such variation.
Based on desired goals and expected usage & environment, the team should build a robust design that will perform as predicted. FMEA helps to focus on high risk areas and provide input to cost reduction or reliability improvement opportunities.
Methodology
Starting with a combination of discussions and component reviews, focus is placed on material properties and common failure mechanisms. Other tools are added as per need to provide details to the analysis; these may include stress/strength analysis, derating, and FMEA, resulting in a set of recommendations to select materials.
Derating
Derating is a technique usually employed in electrical power and electronic devices, wherein the devices are operated at less than their rated maximum power dissipation, taking into account the case/body temperature, the ambient temperature and the type of cooling mechanism used. In this article, we will briefly explain the theoretical background of derating and how it is applied.
Derating increases the margin of safety between part design limits and applied stresses, thereby providing extra protection for the part. By applying derating in an electrical or electronic component, its degradation rate is reduced. The reliability and life expectancy are improved.
Intuitively, if a component or system is operated under its design limit, it will be more reliable than if it is operated at or above the design limit. Theoretically, the benefit of derating can be explained using load-strength interference theory.
Derating is defined as ‘a policy of deliberately under stressing components in order to provide increased reliability’. The selection of components of higher stress capability than is required for normal operation is an empirical but effective and well established method of reducing their failure rate; e.g. the use of a half watt resistor in circuit conditions demanding a quarter watt dissipation.
Stress rating is defined as the ratio of applied stress to rated stress, for example, the ratio of applied voltage to rated voltage in capacitor applications. Generally as stress increases failure rate also increases, usually exponentially; conversely as stress reduces failure rate reduces. However, care must be taken when applying derating as a method of improving reliability because at very low stress ratios failure rate may again increase.
Typically the components to which derating is applicable include transistors, resistors, transformers, integrated circuits, micro-electronic devices, and other passive electronic devices with stress dependent failure rates, such as capacitors and inductors.
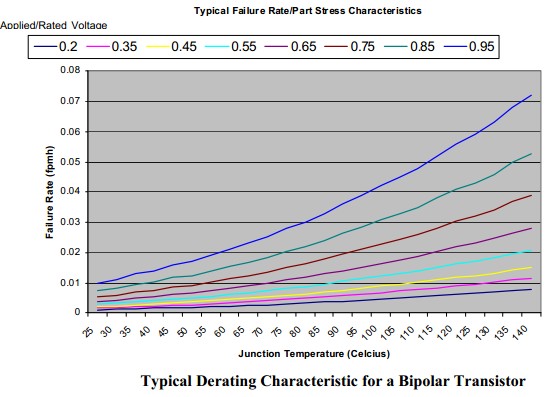
Load-Strength Interference – Usually, failure happens when the applied load exceeds the strength. Load and strength should be considered in a general way. For electronic parts, “load” might refer to voltage, power or an internal stress such as junction temperature. “Strength” might refer to any resisting physical properties.
Electronic components of a given type are not identical. They have strength variability. This variability results from the differences between raw materials and between manufacturing processes. Even for components made from the same materials and by the same processes, differences still exist due to noise factors such as microscopic material defects or variations within a single manufacturing process. Therefore, the strength of a component is considered to be a random variable. The load applied to electronic parts, such as power, temperature or humidity, is also a random variable. Thus, statistical distributions are usually used to describe the load and strength.
Two factors are used to analyze the interference of load and strength distributions. These factors are safety margin (SM) and loading roughness (LR). Safety margin is defined by:
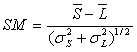
where L and S are the mean values of the load and strength distributions, and σL and σS are the standard deviations of the load and strength distributions. SM is the relative separation of the mean values of load and strength. Loading roughness is defined in terms of the standard deviation of the load by:
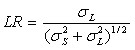
Derating Standards – Several derating guidelines have been issued by military or other agencies, and the following are some examples:
- MIL-STD-975, published by NASA, focuses on selection of parts used in the design and construction of space flight hardware as well as mission-essential ground support equipment.
- MIL-STD-1547, published by the Department of Defense, is targeted to aid in the design, development and fabrication of electronic systems with long life and/or high reliability requirements while operating under the extreme conditions of space and launch vehicles.
- AS4613, published by the U.S. Navy, sets forth derating requirements for the reliable application of electronic and electromechanical parts.
- NAVSEA TE000-AB-GTP-010, published by the U.S. Navy, contains derating requirements and part selection and application information on the ten most commonly used electrical and electronic parts.
- ECSS-Q-30-11A, prepared and maintained under the authority of the Space Components Steering Board in partnership with the European Space Agency, contains derating requirements applicable to electronic, electrical and electromechanical components.
- MSFC-STD-3012, prepared by NASA’s Marshall Space Flight Center, sets requirements for electrical, electronic and electromechanical parts selection, management and control for space flight and mission-essential ground support equipment for Marshall Space Flight Center programs.