Reverse logistics deals with the flow of goods that go back up the supply chain for a number of reasons, including: product returns, repairs, maintenance and end-of-life returns for recycling or dismantling. Reverse logistics has both a service (repair, recalls, etc.) and an environmental component.
Reasons why reverse logistics is often only partially incorporated into international network design include:
- no infrastructure: companies often try to use the same outbound distribution system to handle returns without considering if it is fit for purpose;
- reverse logistics is often a ‘corner-of-the-desk concern’, and does not receive sufficient resources;
- much attention on the subject is driven by legislation, not yet by recognized business value;
- focal firms see reverse logistics as a cost of doing business;
- the subject is intuitively not popular: it means something has gone wrong, so people are tempted to ignore it or hide it;
- it is hard to forecast the reverse flow and composition – what is going to come back.
Reverse logistics stands for all operations related to the reuse of products and materials. It is “the process of planning, implementing, and controlling the efficient, cost effective flow of raw materials, in-process inventory, finished goods and related information from the point of consumption to the point of origin for the purpose of recapturing value or proper disposal. More precisely, reverse logistics is the process of moving goods from their typical final destination for the purpose of capturing value, or proper disposal. Remanufacturing and refurbishing activities also may be included in the definition of reverse logistics.” The reverse logistics process includes the management and the sale of surplus as well as returned equipment and machines from the hardware leasing business. Normally, logistics deal with events that bring the product towards the customer. In the case of reverse logistics, the resource goes at least one step back in the supply chain. For instance, goods move from the customer to the distributor or to the manufacturer.
When a manufacturer’s product normally moves through the supply chain network, it is to reach the distributor or customer. Any process or management after the sale of the product involves reverse logistics. If the product is defective, the customer would return the product. The manufacturing firm would then have to organise shipping of the defective product, testing the product, dismantling, repairing, recycling or disposing the product. The product would travel in reverse through the supply chain network in order to retain any use from the defective product. The logistics for such matters is reverse logistics.
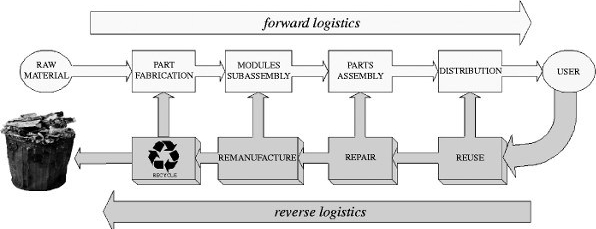
Definition
“The process of planning, implementing, and controlling the efficient, cost effective flow of raw materials, in-process inventory, finished goods (in the humanitarian context) and related information from the point of customer receipt to the point of origin to recapture value or appropriate disposal.” -Wikipedia
“Reverse logistics is the management of all the activities involved in the flow of goods, demand information and money in the opposite direction of the primary logistics flow, a reduction in the generation of waste, and the management of the collection, transport, disposal, and recycling of hazardous as well as non-hazardous waste in a way that maximises the long term profitability of the business.”
Types of Reverse Logistics
Reverse logistics covers a broad range of items and activities and can include:
- Movement of capital items and equipment to the next emergency response.
- Removal of containers and packaging from response area.
- Destruction of spoiled food commodities and out of date pharmaceuticals.
- Return of rejected goods to the suppliers.
- Movement of excess or over-supplied goods to other programs or organisations.
Aspects of Reverse Logistics
Packaging – Where possible, packaging materials could serve dual purposes as in the case of large bladders, wooden pallets, cooking drums, fuel drums, etc. Some examples include:
Pillows/bladders – As goods are mobilised through various modes of transport in response to emergencies, the bracing in ship and rail containers can be done with “pillows” which are basically large bladders filled with air.
- The bracings can then be further used at distribution sites for water storage (or fuel storage if they are correctly lined).
- These “pillows” filled with air also weigh less than traditional wood bracing and thus lower the weight of the shipment and the cost.
- Environmentally the lower weight means less fuel is used which is good for the environment.
Wooden pallets vs. plastic pallets
- Wooden pallets, though less expensive, may contain pests which can devastate indigenous agricultural industries.
- Developed countries are therefore required to treat wooden pallets with chemicals making the burning of these for firewood toxic and less environmental friendly.
- Many countries have now restricted the clearance for wooden pallets from many areas to combat the pest issue.
- Plastic pallets can be reused as the local population will not be tempted to burn them for firewood.
Cooking oil drums and fuel drums
- These can usually be converted into barbecues or water storage containers on site.
- Agencies that plan for this will look more efficient.
Plan to Back Ship
- Most of the goods in the humanitarian world are consumable and thus are on a one-way trip.
- Packaging may be able to be disposed, recycled or reused in the capital city while it may not be possible in remote field locations.
- Return shipping will not be expensive, as trucks and aircraft have to return empty anyway. But to capitalise on such opportunities the program is required to plan in advance so as not to cause unnecessary delays to transporters.
Why reverse logistics
Reverse logistics presents one of the biggest operational challenges in the world of e-commerce freight logistics due to the sheer volume and cost of processing returns. Effective reverse logistics is believed to result in direct benefits, including improved customer satisfaction, decreased resource investment levels, and reductions in storage and distribution costs. The amount of returned goods going backwards along the supply chain from the end point (customers) is usually much more than people normally think. As an example, the sheer volume of returns generated in many companies, ranged from 3% to as high as 50% of total shipments across all industries. Many other studies indicated the real costs of the returns take up roughly 3%-5% of total revenue. Surprisingly, for the traditional bricks-and-mortar retail operations, returns are 3 to 4 times more expensive than forward (outbound) shipments. In some industries such as book publishing, catalog retailing, and greeting card, over 20% of all products sold are eventually returned to the vendor. What’s more surprising is that some industries are estimated to have return rates in the range of 30 percent to 50 percent with other estimates are as high as 60 percent. Given the status quo of the reverse logistics, the neglect of the importance to the reverse part of the logistics flow opens an opportunity to create and manage customer relationships and build customer loyalty to the retailer.
Return of unsold goods – In certain industries, goods are distributed to downstream members in the supply chain with the understanding that the goods may be returned for credit if they are not sold e.g., newspapers and magazines. This acts as an incentive for downstream members to carry more stock, because the risk of obsolescence is borne by the upstream supply chain members. However, there is also a distinct risk attached to this logistics concept. The downstream member in the supply chain might exploit the situation by ordering more stock than is required and returning large volumes. In this way, the downstream partner is able to offer high level of service without carrying the risks associated with large inventories. The supplier effectively finances the inventory for the downstream member. It is therefore important to analyze customers’ accounts for hidden costs.
Reusable packaging – Reusable packaging systems require a closed-loop logistics system. Examples include reusable pallets, bulk boxes such as Euro containers, Reusable bottles for milk, soda, and beer, compressed gas cylinders, beer kegs, etc.
Refusal of the products in the cash on delivery (COD) – In case of e-commerce business, many websites offer the flexibility of cash on delivery (COD) to their customers. Sometimes customers refuse the product at the time of delivery, as there is no commitment to take the product. Then the logistics service provider follows the process of reverse logistics on the refused cargo. It is also known as Return to Origin (RTO). In this process, the e-commerce company adds the refused cargo to its inventory stock again, after proper quality checks as per the company’s rules.
Reverse Logistics for Demonstrations – In case of the Demonstration of Products to the client as part of Pre-Sales process, The Demonstration equipment is sent to the Customer and has to be returned to maintain Revolving Inventory.
Effective Reverse Logistics
To implement a successful Reverse Logistics process, we can follow the below points:
Have a clear visible system in place for real-time monitoring and tracking. OEMs should have a proper process for the products that customers would want to return. The first point is when the customer calls customer care to request a return. The official should be able to differentiate the queries based on different scenarios like: damaged, defective, not available and want a different product. The people in charge of the transportation can then screen the products with respect to the different reasons and ship them back to the places determined for each scenario.
Outsource your logistics to the 3PL vendors. Reverse logistics itself is a very complex process and to do it effectively one needs to have a separate department with skilled human resources. Reverse logistics requires a huge investment, and it is not possible to do it properly from Day1.OEMs tend to outsource this process instead of setting up a department. 3rd Party Logistics vendors like Blue-dart, FedEx, etc. have developed systems through which the OEMs can keep a real time track of their reverse shipments while the actual job is being performed by the outsiders. This not only helps the OEMs to reduce investments but also in attaining an effective return management process.
Figure out your distribution centers and warehouses to manage reverse logistics. This is the most important part of the reverse logistics process. To have an effective RL process in place, OEMs needs to decide strategically on the return/ collection centers. Locations will have to be based on the cost of the products and the reason for return. For example, a damaged / defective product will go to the inspection plant where it would get inspected, and actions would be taken accordingly. On the other hand, if it is in a state of re-use then it would go to the distribution centers for resale.
Communicate with customers during the return process. This helps in building a trustworthy relationship between customers and industries. Communication is one of the deciding factors for an OEMs sustainability in the long term. This era is of providing quality service. To get trustworthy, OEMs need to communicate continuously with customers. They need to listen and understand the queries placed by their customers and provide the best possible solution which will delight them. In case of returns, they need to interact with their customers and let them know the status of their returns. They should follow an interactive approach rather than a reactive approach.
After understanding the efficient ways to implement a successful reverse logistic process, the following steps can be incorporated to get the maximum value of a returned product.
- Disassemble – Once the returned product reaches to the DC/ Warehouse, try to disassemble it to view the parts that malfunctioned and the parts that can be used.
- Sort – Segregate those into two groups like the malfunctioned parts and usable parts.
- Reuse – Reuse the usable parts to manufacture new products so that the daily wastage reduces.
- Repair – In case if there is a need for small repairs, the OEMs can fix them, and the same product can be re-sold.
- Recycle – Recycle the parts that malfunctioned and cannot be re-used by taking proper safety measures towards the society.