Reliability and maintainability management is the management of failure. By using specific approaches and tools, one can obtain optimized, cost-effective solutions to the design, assembly and use of a product.
Systems referred to as repairable systems can be returned to service if they fail. Prescribed maintenance actions will maintain a system in operating condition and reduce the probability of failure due to wear. Maintained systems may be subject to corrective and preventive maintenance (CM and PM).
Corrective maintenance includes all action to return a system from a failed to an operating or available state. The amount of corrective maintenance is therefore determined by reliability. Corrective maintenance action usually cannot be planned; we must repair failures when they occur, though sometimes repairs can be deferred. Corrective maintenance can be quantified as the mean time to repair (MTTR). The time to repair, however, includes several activities, usually divided into three groups
- Preparation time: finding the person for the job, travel, obtaining tools and test equipment, etc
- Active maintenance time: actually doing the job.
- Delay time (logistics time): waiting for spares, and so on, once the job has been started.
Active maintenance time includes time for studying repair charts, and so on, before the actual repair is started, and time spent in verifying that the repair is satisfactory. It might also include time for post-repair documentation when this must be completed before the equipment can be made available. Corrective maintenance is also specified as a mean active repair time (MART) or mean active corrective maintenance time (MACMT), since it is only the active time (excluding documentation) that the designer can influence.
Preventive maintenance seeks to retain the system in an operational or available state by preventing failures from occurring. This can be by servicing, such as cleaning and lubrication, or by inspection to find and rectify incipient failures, for example by crack detection or calibration. Preventive maintenance affects reliability directly. It is planned and should be performed when we want it to be. PM does not reduce the constant failure rate that is inherent to the system but tends to maintain the system at that level of failure probability. PM is measured by the time taken to perform the specified maintenance tasks and their specified frequency.
System’s availability can be expressed in several different ways, depending on the available data and the objectives of the analysis availability. Availability is a measure of the likelihood that a system will be ready to operate (system is up) when it is called on to operate. Availability, is a function of the number of maintenance actions necessary and the time it takes to complete the actions. Inherent availability is the steady state availability which considers only the corrective maintenance. Assuming that CM actions occur at a constant rate, it can be estimated as
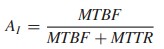
MTBF is the mean time between failure and MTTR is the mean time to repair which is the same as mean corrective maintenance time. If the preventive maintenance actions can be planned and performed when there will be no demand to use the system, the time to perform these actions will not affect the availability. Availability is uptime divided by total time during which there could be a demand to use the system.
Systems referred to as repairable systems can be returned to service if they fail. Prescribed maintenance actions will maintain a system in operating condition and reduce the probability of failure due to wear. Maintained systems may be subject to corrective and preventive maintenance (CM and PM).
Corrective maintenance includes all action to return a system from a failed to an operating or available state. The amount of corrective maintenance is therefore determined by reliability. Corrective maintenance action usually cannot be planned; we must repair failures when they occur, though sometimes repairs can be deferred. Corrective maintenance can be quantified as the mean time to repair (MTTR). The time to repair, however, includes several activities, usually divided into three groups
- Preparation time: finding the person for the job, travel, obtaining tools and test equipment, etc
- Active maintenance time: actually doing the job.
- Delay time (logistics time): waiting for spares, and so on, once the job has been started.
Active maintenance time includes time for studying repair charts, and so on, before the actual repair is started, and time spent in verifying that the repair is satisfactory. It might also include time for post-repair documentation when this must be completed before the equipment can be made available. Corrective maintenance is also specified as a mean active repair time (MART) or mean active corrective maintenance time (MACMT), since it is only the active time (excluding documentation) that the designer can influence.
Preventive maintenance seeks to retain the system in an operational or available state by preventing failures from occurring. This can be by servicing, such as cleaning and lubrication, or by inspection to find and rectify incipient failures, for example by crack detection or calibration. Preventive maintenance affects reliability directly. It is planned and should be performed when we want it to be. PM does not reduce the constant failure rate that is inherent to the system but tends to maintain the system at that level of failure probability. PM is measured by the time taken to perform the specified maintenance tasks and their specified frequency.
System’s availability can be expressed in several different ways, depending on the available data and the objectives of the analysis availability. Availability is a measure of the likelihood that a system will be ready to operate (system is up) when it is called on to operate. Availability, is a function of the number of maintenance actions necessary and the time it takes to complete the actions. Inherent availability is the steady state availability which considers only the corrective maintenance. Assuming that CM actions occur at a constant rate, it can be estimated as
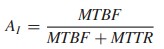
MTBF is the mean time between failure and MTTR is the mean time to repair which is the same as mean corrective maintenance time. If the preventive maintenance actions can be planned and performed when there will be no demand to use the system, the time to perform these actions will not affect the availability. Availability is uptime divided by total time during which there could be a demand to use the system.