Quality management ensures that an organization, product or service is consistent. It has four main components: quality planning, quality control, quality assurance and quality improvement. Quality management is focused not only on product and service quality, but also the means to achieve it. Quality management therefore uses quality assurance and control of processes as well as products to achieve more consistent quality.
History of Quality Movement
The quality movement can trace its roots back to medieval Europe, where craftsmen began organizing into unions called guilds in the late 13th century. Until the early 19th century, manufacturing in the industrialized world tended to follow this craftsmanship model. The factory system, with its emphasis on product inspection, started in Great Britain in the mid-1750s and grew into the Industrial Revolution in the early 1800s. In the early 20th century, manufacturers began to include quality processes in quality practices. After the United States entered World War II, quality became a critical component of the war effort: Bullets manufactured in one state, for example, had to work consistently in rifles made in another. The armed forces initially inspected virtually every unit of product; then to simplify and speed up this process without compromising safety, the military began to use sampling techniques for inspection, aided by the publication of military-specification standards and training courses in Walter Shepherd’s statistical process control techniques.
In the few years since the turn of the century, the quality movement seems to have matured beyond Total Quality. New quality systems have evolved from the foundations of Deming, Juran and the early Japanese practitioners of quality, and quality has moved beyond manufacturing into service, healthcare, education and government sectors.
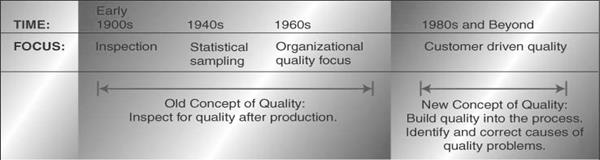
Continuous Improvement
Continuous improvement involves constantly identifying and eliminating the causes that prevent a system or process from functioning at its optimum level. The concept of continuous improvement originated in Japan in the 1970s. It was adopted in many countries, including U.S.A., in the early 1980s. Continuous improvement—and consequent customer satisfaction—is the principle on which the concept of Lean manufacturing is developed. When this principle is combined with just-in-time technique, it results to Lean manufacturing. Continuous improvement helps an organization to add value to its products and services by reducing defects, mistakes, etc. and to maximize its potential. As continuous improvement requires constant ongoing efforts, it is essential that the top management takes a long term view and commits itself for its implementation.
Continuous improvement enables organizations identify and rectify problems as and when they occur. Thus, it ensures smooth functioning of the processes. Many modern quality improvement models or tools like control charts, sampling methods, process capability measures, value analysis, design of experiments, etc. have been influenced by the concept of continuous improvement.
The transformation model enables companies to structure their quality management approach. The transformation model divides operations into small, manageable phases: Input, Processing, and Output.
The first phase in the transformation model is the Input phase. This phase addresses quality issues with raw materials, resources, design, and supplies. It ensures that quality is a key consideration during the planning and design stages of any project. This enables companies to build quality into their products and services from the very beginning and uses QFD and FMEA tools.
The second phase in the transformation model is the Processing phase. In this phase, companies can try to make their production processes more efficient and effective. Often, the cause of poor-quality products is poor-quality production processes, so by improving their processes, companies can improve their products. This is known as process control and SPC is used.
The last phase in the transformation model is the Output phase. Quality management in this phase requires companies to check the quality of finished goods and services. Using quality control methods, companies can evaluate their products before they’re made available to customers. The two tools used in this phase are inspection and sampling.