All of the four basic phases of control of manufacture are easily identified in production planning and control. The plan for the processing of materials through the plant is established by the functions of process planning, loading, and scheduling. The function of dispatching puts the plan into effect; that is, operations are started in accordance with the plant. Actual performance is then compared to the planned performance, and, when required, corrective action is taken. In some instances re-planning is necessary to ensure the effective utilization of the manufacturing facilities and personnel.
- Process Planning (Routing) – The determination of where each operation on a component part, subassembly, or assembly is to be performed results in a route for the movement of a manufacturing lot through the factory. Prior determination of these routes is the job of the manufacturing engineering function.
- Loading – Once the route has been established, the work required can be loaded against the selected machine or workstation. The total time required to perform the operation is computed by multiplying the unit operation times given on the standard process sheet by the number of parts to be processed. This total time is then added to the work already planned for the workstation. This is the function of loading, and it results in a tabulated list or chart showing the planned utilization of the machines or workstations in the plant.
- Scheduling – Scheduling is the last of the planning functions. It determines when an operation is to be performed, or when work is to be completed; the difference lies in the detail of the scheduling procedure. In a centralized control situation – where all process planning, loading, and scheduling for the plant are done in a central office- the details of the schedule may specify the starting and finishing time for an operation. On the other hand, the central schedule may simply give a completion time for the work in a given department.
- Combining Functions – While it is easy to define “where” as process planning, “how much work” as loading, and “when as scheduling, in actual operations these three functions are often combined and performed concurrently. How far in advance routes, loads, and schedules should be established always presents an interesting problem. Obviously, it is desirable that a minimum of changes be made after schedules are established. This objective can be approached if the amount of work scheduled for the factory or department is equal to or slightly greater than the manufacturing cycle. For optimum control, it should never be less than the manufacturing cycle.
- Dispatching – Authorizing the start of an operation on the shop floor is the function of dispatching. This function may be centralized or decentralized. Again using our machine-shop example, the departmental dispatcher would authorize the start of each of the three machine operations – three dispatch actions based on the foreman’s routing and scheduling of the work through his department. This is decentralized dispatching.
- Reporting or Follow – up – The manufacturing activity of a plant is said to be “in control” when the actual performance is within the objectives of the planned performance. When jobs are started and completed on schedule, there should be very little, if any, concern about the meeting of commitments. Optimum operation of the plant, however, is attained only if the original plan has been carefully prepared to utilize the manufacturing facilities fully and effectively.
- Corrective Action – This is the keystone of any production planning and control activity. A plant in which all manufacturing activity runs on schedule in all probability is not being scheduled to its optimum productive capacity. With an optimum schedule, manufacturing delays are the rule, not the exception.
- Re-planning – Re-planning is not corrective action. Re-planning revise routes, loads, and schedules; a new plan is developed. In manufacturing this is often required. Changes in market conditions, manufacturing methods, or many other factors affecting the plant will often indicate that a new manufacturing plan is needed.
Various production planning and control functions are summarized in below table
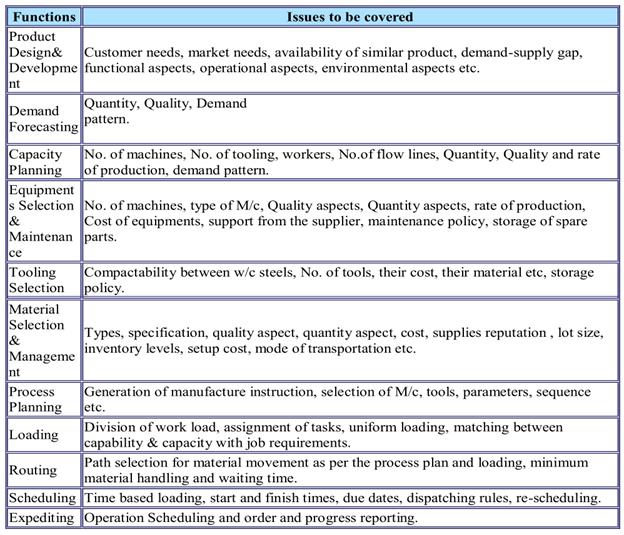