New product development (NPD) is the complete process of bringing a new product to market. New product development is described in the literature as the transformation of a market opportunity into a product available for sale and it can be tangible (that is, something physical you can touch) or intangible (like a service, experience, or belief). A good understanding of customer needs and wants, the competitive environment and the nature of the market represent the top required factors for the success of a new product.
The product development process typically consists of several activities that firms employ in the complex process of delivering new products to the market. Every new product will pass through a series of stages from ideation through design, manufacturing and market introduction. The development process basically has main phases, as
- Fuzzy front-end (FFE) is the set of activities employed before the formal and well defined requirements specification is completed. Requirements are a high-level view of what the product should do to meet the perceived market or business need. This is sometimes referred to as the “stage-gate process”.
- Product design is the development of both the high-level and detailed-level design of the product: which turns the what of the requirements into a specific how this particular product will meet those requirements. On the marketing and planning side, this phase ends at pre-commercialization analysis stage.
- Product implementation is the phase of detailed engineering design of mechanical or electrical hardware, or the software engineering of software or embedded software, or design of soft goods or other product forms, as well as of any test process that may be used to validate that the prototype objects actually meet the design specification and the requirements specification that was previously agreed to.
- Fuzzy back-end or commercialization phase represent the action steps where the production and market launch occur.
Conceptual models have been designed in order to facilitate a smooth process. The concept adopted by IDEO, a successful design and consulting firm, is one of the most researched processes in regard to new product development and is a five-step procedure. These steps are listed in chronological order
- Understand and observe the market, the client, the technology, and the limitations of the problem;
- Synthesize the information collected at the first step;
- Visualise new customers using the product;
- Prototype, evaluate and improve the concept;
- Implementation of design changes which are associated with more technologically advanced procedures and therefore this step will require more time.
The Stage-Gate model developed in the 1980s was proposed as a new tool for managing new products development processes. The 2010 APQC benchmarking study reveals that 88% of U.S. businesses employ a stage-gate system to manage new products, from idea to launch. In return, the companies that adopt this system are reported to receive benefits such as improved teamwork, shorter cycle time, improved success rates, earlier detection of failure, a better launch, and even shorter cycle times – reduced by about 30%. These findings highlight the importance of the stage-gate model, making it the single most important discovery in the area of new product development.
A variety of models have been proposed to get better insight into the new product development process and its management. The process starts with an idea to build a product that meets specific requirements (or create new requirements for radically innovative products) defined by customers and/or the manufacturer, and ends when the product is launched on the market. It involves several phases and the number of phases and descriptions of the phases vary from model to model. An illustrative sample is given in the table below.
The diversity in the number of phases, the different terminology used, and different interpretations of the same terms may best be explained by the different contexts, such as
- type of product (mechanical, electrical, electronic),
- degree of innovation (redesign vs. routine design),
- product complexity,
- production process (manual, highly automated, existing production facilities),
- type and number of suppliers/original equipment manufacturers (OEMs),
- technologies involved,
- availability of resources (e.g., manpower), and
- time and budget constraints.
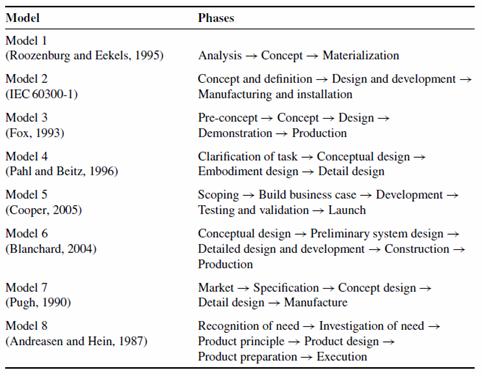
Simulation Driven Product Development
Simulation Driven Product Development, SDPD, and Simulation Driven Design, SDD, has been frequently discussed in the automotive industry for the last decade. For instance Volvo Cars Corporation designed its S80 model by great support of simulations already 2001. This was the first car where the strength the spot-welding was predicted by computerized calculation instead of conventional testing
The differences between SDPD and SDD are their implementation range. In SDD, simulation is the basis when generating the design. The design engineers make, for instance, concept choices based on simulation. In SDD, simulation still might be complementary to the physical testing which tends to be the primary way of verifying a solution. In SDPD, simulations are the basis for the entire product development process, not only decisions related to the design phase. It can for instance comprise different kinds of virtual testing, virtual factories etc. Physical testing might still be necessary to, for instance, verify legacy requirement and capture the reality in order to be able to generate accurate simulation models. However, in a SPDP environment, physical testing is a support function to virtual testing and not vice versa. By using simulation at an early phase of the product development process companies has a potential of reducing time to market, increase quality and reduce costs.
Different simulation methods are mainly used today by manufacturing companies to support the product development process. Nowadays, the whole product development and production cycle can be computerized, the three most important parts are: Computer-aided design, CAD; Computer-aided engineering, CAE and Computer-aided Manufacturing, CAM. These three areas create the different phases of a virtual prototyping environment.
In order to use any CAE tools, such as FEM or CFD, a CAD model needs to be created first. That model will then be the input to the CAE simulations. The results from the CAE simulations will then be used to redesign the previous CAD model. This is repeated in an iterative simulation driven design cycle until the CAD model has the demanded functionality. When the design objectives are reached CAM software is used to simulate the manufacturing processes, such as milling parameters and tool routes.