With the help of information retrieved from the bill of materials, master schedule and inventory records file, the MRP system indicates the total requirement for raw materials, parts and components, and subassemblies against each period on the planning sphere. At first, MRP processing determines gross material requirements, then deducts the inventory in hand, and adds it back to the safety stock, for the computation of net requirements.
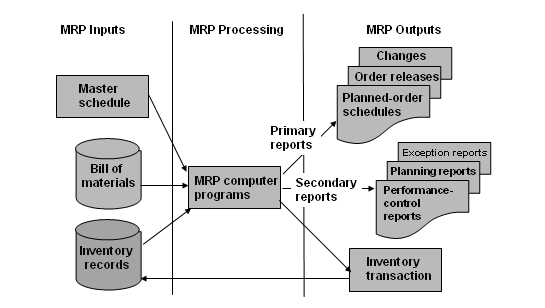
The MRP outputs can be in the form of primary reports as well as secondary reports. There are three kinds of primary reports, viz. planned order schedules, order releases and changes to planned orders. Planned order schedules delineate the quantity as well as timing of future material orders. Order releases give authorizations on orders to be made. Changes to planned orders may include revisions or cancellations of the time frame or quantity. On the other hand, secondary reports of MRP can also be of three kinds, viz. performance control reports, planning reports and exception reports. Performance control reports are used to keep a track of problems, such as delivery dates and stock outs that have been missed out, in order to assess system performance. Planning reports are used to forecast future inventory requirements. Exception reports are used to divert the attention of managers toward key issues such as late orders, excessive scrap rates, etc. Though working on a backward direction from the production plan to get a finished product to understand the component requirements appears a simple process, it can indeed be extremely complex, particularly in the event of raw materials being used for a variety of different products. Matters can become further complicated in product design, order quantities and production schedule. The significance of computer power is apparent when the number of material schedules that need to be tracked is considered.
Understanding MRP II
During the 80s era, the MRP technology was enhanced to formulate a new approach, known as MRP (Manufacturing Resource Planning) II that encompassed techniques to facilitate providing valid production schedules that further enables better planning and control of other resources. Often the areas of finance, marketing and human resources get affected by any improvements in customer delivery commitments, HR management projections and cash flow projects. The invention of MRP II has not replaced MRP, or is an improved version of MRP, but it does expand the scope of production resource planning and engages other functional areas, such as finance, marketing, purchase, HR and engineering, in the planning stage of an organization. In MRP II, the functional areas are inputs to the master production schedule. With this, MRP generates material requirements through which production managers plan the capacity. MRP II systems generally consist of simulation capabilities for the managers to be able to assess alternate options.
Computer Application to MRP Process
MRP II refers to computer-based planning and scheduling designed such that it can enhance the management control over manufacturing and its ancillary functions. Some of the key terminologies associated with MRP (computerized) planning forms are:
Gross requirements: These represent futuristic needs for raw materials, part components, subassemblies and finished products by the end of the specified period. These requirements are either derived from the master schedule for end items or from the combined requirements of other items.
Scheduled receipts: These represent ordered materials from a vendor or outstanding in-house shop to be received at the onset of the period. MRP forms indicate quantity and projected time of receipt, and include planned receipts as well.
On hand: On hand is the quantity of a product expected to exist at the end of the specified time period. This includes amount retrieved from earlier period plus planned – scheduled receipts and ordered receipts minus gross requirements.
Net requirements: These represent net amount required in a specified period, equivalent to the gross requirements minus projected inventory from the earlier period coupled with scheduled receipts.
Planned order receipt: These represent to-be-ordered materials from a vendor or in-house shop to-be-received at the onset of the period, or are similar to a scheduled receipt.
Planned order release: These represent the planned amount to be ordered in the adjusted time period through the lead time offset such that the materials can be received on time. Upon the actual release of orders, the planned order releases are removed from the form, and the receipts generated by them are altered to scheduled receipts. The MPS determines gross or projected requirements for finished items to the MRP system, which do not consider inventory on hand or on order.
The MRP computer program subsequently explodes the demands for finished items into requirements for part components and materials by processing all major bills of materials on every single level. Thereafter, net requirements are measured by adjusting for current inventory and items ordered and recorded in the inventory status file.
Net requirements = Gross requirements – [On hand product quantity + Scheduled receipts]
MRP Reports
Database maintenance is evident in MRP II that involves constant focus on the databases influencing the planning process, including inventory reorder levels, standard costs, lead times, time standards and accuracy in inventory stock status.
Details | Key Reports | |
Inventory Management | Establishes reorder values, amounts, and lead times, as may be required. For manufactured items, it runs lead time generator, if needed. Corroborate on-hand quantities via selective counting or physical inventory. | MRP parameters, physical check, inventory value, bills of material, routings report, material costs, work centers. |
Work Orders | Comprises all activities related to physically formulating and processing production orders at the factory, such as generating orders, printing documents, processing labour and materials, outside processing, reporting end production. | Work order schedule, work centre backlog, work centre schedule, work order status, work order shortages. |
Purchase Orders | Comprises activities associated with coordination of purchases and receipts of materials and services from external vendors, such as entering purchase orders manually, vendor invoices and transferring inspected items from quality check to inventory. | PO listing, PO receipts for buying history |
Sales Orders | Consists of activities related to receiving, scheduling and shipping of client orders. | Sales Order listing, backorder listing, shipping schedule |
Independent and Dependent MRP system
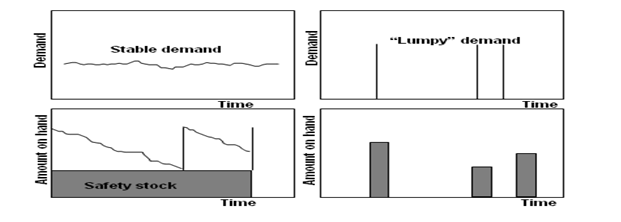
Independent MRP System is referred to as the demand for finished items, whereas, Dependent MRP System is referred to as the demand for subassemblies or part components required for the production of the finished items. Dependent demand is the function of independent demand. The total quantity of part components and raw materials required at a specified time period is the function of the dependent demand. Independent demand is steady when allowances for seasonal variations are executed, but tend to be “lumpy”. Large amounts are used at specific stages in time with no or little usage at other times.
Some of the independent demand items need to be carried on continuously, while some of the dependent demand items need only be stored just before the time they are required in the manufacturing process. The expectedness of dependent demand items indicates there is less or no safety stock requirement.
Demand driven MRP is a multi-echelon formal planning and execution technique with five distinct components:
- Strategic inventory positioning – The first question of effective inventory management is not, “how much inventory should we have?” Nor is it, “when should we make or buy something?” The most fundamental question to ask in today’s manufacturing environments is, “given our system and environment, where should we place inventory to have the best protection?” Inventory is like a break wall to protect boats in a marina from the roughness of incoming waves. Out on the open ocean the break walls have to be 50–100 feet tall, but in a small lake the break walls are only a couple feet tall. In a glassy smooth pond no break wall is necessary.
- Buffer profiles and level – Once the strategically replenished positions are determined, the actual levels of those buffers have to be initially set. Based on several factors, different materials and parts behave differently (but many also behave nearly the same). DDMRP calls for the grouping of parts and materials chosen for strategic replenishment and that behave similarly into “buffer profiles.” Buffer profiles take into account important factors including lead time (relative to the environment), variability (demand or supply), whether the part is made or bought or distributed and whether there are significant order multiples involved. These buffer profiles are made up of “zones” that produce a unique buffer picture for each part as their respective individual part traits are applied to the group traits.
- Dynamic adjustments – Over the course of time, group and individual traits can and will change as new suppliers and materials are used, new markets are opened and/or old markets deteriorate and manufacturing capacities and methods change. Dynamic buffer levels allow the company to adapt buffers to group and individual part trait changes over time through the use of several types of adjustments. Thus, as more or less variability is encountered or as a company’s strategy changes these buffers adapt and change to fit the environment.
- Demand-driven planning – takes advantage of the sheer computational power of today’s hardware and software. It also takes advantage of the new demand-driven or pull-based approaches. When these two elements are combined then there is the best of both worlds; relevant approaches and tools for the way the world works today and a system of routine that promotes better and quicker decisions and actions at the planning and execution level.
- Highly visible and collaborative execution – Simply launching purchase orders (POs), manufacturing orders (MOs) and transfer orders (TOs) from any planning system does not end the materials and order management challenge. These POs, MOs and TOs have to be effectively managed to synchronize with the changes that often occur within the “execution horizon.” The execution horizon is the time from which a PO, MO or TO is opened until the time it is closed in the system of record. DDMRP defines a modern, integrated and greatly needed system of execution for all part categories in order to speed the proliferation of relevant information and priorities throughout an organization and supply chain.