By basing the control system on a microprocessor, the control scheme can be changed by a1tering the control program. This will enable thorough testing of many control schemes and also provide the ability to simulate various types of blade pitch, generator field current, and yaw direction control1ers.
The wind turbine is designed to be a fully automatic piece of power production equipment for use on a utility grid. In order to meet these requirements the control system has to be capable of
- Monitoring wind conditions, Maintaining alignment with the wind
- Controlling the rotor speed and power level., Starting and stopping wind turbine safely.
- Monitoring key parameters throughout to assure that critical items are operating within specified tolerances.
- Providing capability for remote starting and stopping the machine.
The following control systems are provided to accomplish these tasks.
- Rotor blade pitch controller, Yaw system.
- Microprocessor , Safety system
- Remote control and monitor system
Based on performance requirement certain parameters are needed to be controlled for the desired operation of the system. Every system is designed to give maximum output at its designed condition only, but if the parameters governing maximum output are controlled in some manner, desired output can be obtained under different operating conditions. Apart from this control systems are needed for safer system operation. Further the designers of wind turbines feel the need for control as large variation of wind gives stresses to component like blade, generator system and tower. By suitable controls stresses can be relieved.
A possible system block diagram of a wind energy conversion system as shown in figure – 1. In this system, the microcomputer accepts inputs such as wind speed, direction, turbine speed, and load requirements, amount of energy, and voltage and frequency being delivered to the load. The microcomputer sends signals to the turbine to establish proper yaw (direction control), blade pitch and to set the brakes in high winds. It sends signal to the generator to change the output voltage if the generator has a separate field. It may turn off non-critical loads in times of light loads and it may turn on optimal loads in strong winds. It may adjust the power conditioner to change the load voltage and frequency.
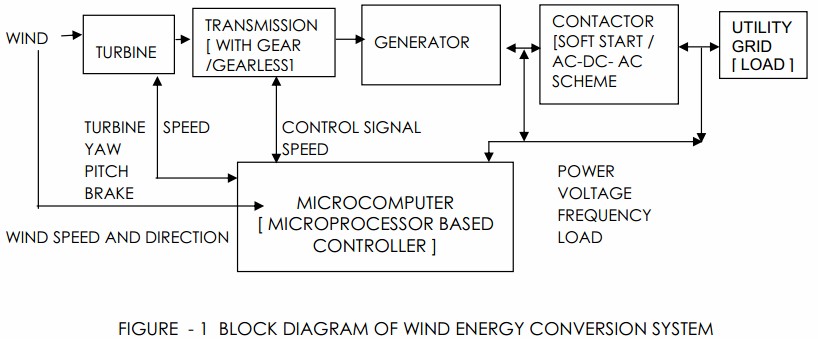
The above system is called as asynchronous system and it has special mode of operation that electric utilities do not have. The turbine speed can be controlled by the load rather than by adjusting the turbine. Electric utilities do have some load management capability, but most of their load is not controllable by the utilities. The utilities therefore adjust the prime mover input (by a valve in a streamline, for example) to follow the variation in load. That is, supply and demand. In case of wind turbines, the turbine-input power is just the power in the wind and is not subject to control. Turbine speed still needs to be controlled for optimum performance, and an electrical load with the proper characteristics can accomplish this. A microcomputer is not essential to this mode of operation, but does allow more flexibility in the choice of load. The basic rule is to not go to any higher form of work than is necessary to do the job. Fixed frequency and fixed voltage system represents a higher form of work than variable – frequency, Variable – voltage systems, so the actual needs of the load need to be examined to determine just how sophisticated the system really needs to be. If a simple system will accomplish the task at less cost, it should be used.
Based on performance requirement mentioned in the last section it is clear that certain parameters are needed to be control for the desired operation of the system. The term control is widely used to describe variety of control functions to obtain automated operation of industrial systems. The necessity for automated operation can be attributed to various factors mentioned above. Every system is designed to give maximum output at its designed condition only, but if the parameters governing maximum output are controlled in some manner, desired output can be obtained under different operating conditions.
Apart from this control systems are needed for safer system operation. Further the designers of wind turbines feel the need for control as large variation of wind gives stresses to component like blade, generator system and tower. By suitable controls stresses can be relieved. The block diagram of various control systems and functions as shown in the figure – 2 and brief description of control systems as
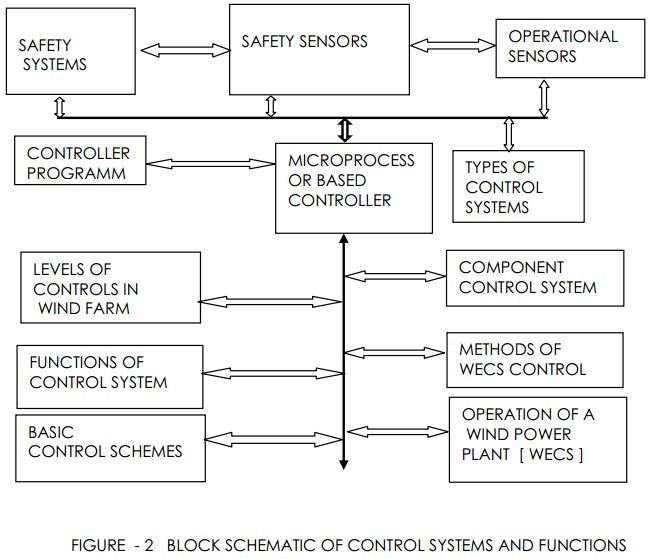