Historically, MRP systems typically were developed on a segregated basis, rather than as part of highly integrated information system. More recently, however, companies are beginning to logically relate many of their information subsystems to the MRP system. Bills of materials data, for example, can be shared with an engineering information system data base; order release and order receipts data can be shared by the order billing and accounts payable information systems; and inventory status data from MRP can be part of marketing or purchasing information system. This type of information integration, in fact, is exactly the impetus for a new generation of manufacturing planning and control systems.
Manufacturing resource planning (MRP II, or “closed loop” MRP) is an integrated information system that steps beyond first generation MRP to synchronize all aspects (not just manufacturing) of the business. The MRP II system coordinates sales, purchasing, manufacturing, finance, and engineering by adopting a focal production plan and by using one unified data base to plan and update the activities in all the systems. As shown in figure 8.3 the process involves developing a production plan from the business plan to specify monthly levels of production for each product line over the next one to five years. Since the production plan affects all the functional departments, it is developed by the consensus of executives and becomes their “game plan” for operations. The production department then is expected to produce at the committed levels, the sales department to sell at these levels, and the finance department to ensure adequate financial resource for these levels. Guided by the production plan, the master production schedule specifies the weekly quantities of specific products to be built. At this point a check is made to determine whether the capacity available is roughly adequate to sustain the proposed master schedule. If not, either the capacity or the master schedule must be changed. Once settled, the master schedule is used in the MRP logic, as previously described, to create material requirements and priority schedules for production. Then, an analysis of detailed capacity requirements determines whether capacity is sufficient for producing the specific components at each work center during the scheduled time periods. If not, the master schedule is revised to reflect the limited available capacity. After a realistic, capacity feasible schedule is developed, the emphasis shifts to execution of plan: purchase schedules and shop schedules are generated. From these schedules, work center loadings, shop floor control, and vendor follow-up activities can be determined to ensure that the master schedule is met.
One use of the MRP II system is to evaluate various business proposals.
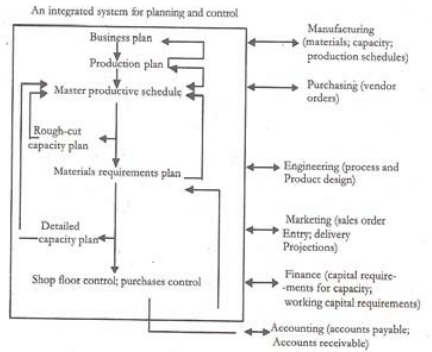
Figure 8.3