As stated earlier, Operations Management is concerned with the conversion of inputs into outputs using physical resources so as to provide the desired utilities to the customers. It involves a number of well planned activities.
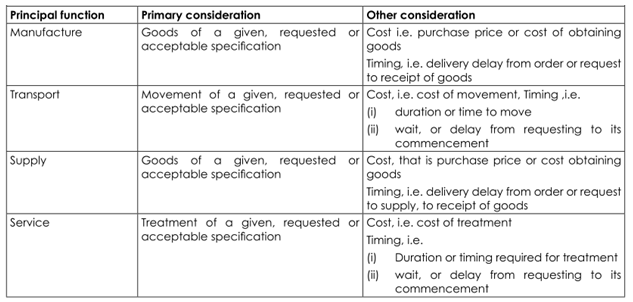
Following are the activities that come under production and operations management functions
- Location of facilities.
- Plant layouts and Material Handling.
- Product Design.
- Process Design.
- Production and Planning Control.
- Quality Control.
- Materials Management.
- Maintenance Management
Location facilities
Location of the proposed factory building is an important consideration in operation management. It is an important strategic level decision-making for an organisation. It deals with the questions such as ‘where our main operations should be based?’ The selection of location is a key-decision because large amount of investment is required in building plant and machinery. An improper location of plant may lead to waste of all the investments made in plant and machinery. Hence, location of plant should be based on the company’s future plan about expansion, diversification, nature of sources of raw materials and many other factors. The very purpose of the location study is to identify the optimal location facility that will results in the greatest advantage to the organization.
Plant layout and material handling
Plant layout refers to the physical arrangement of facilities. It is the configuration of departments, work centres and equipment’s in the inputs conversion process. The objective of the plant layout is to design a physical arrangement that meets the required output quality and quantity most economically. According to James More ‘Plant layout is a plan of an optimum arrangement of facilities including personnel, operating equipment, storage space, material handling equipment and all other supporting services along with the design of best structure to contain all these facilities’.
Material Handling refers to the moving of materials from the store room to the machine and from one machine to the next machine during the production process. It is the art and science of moving, packing and storing of products in any form. Material cost can be reduced by judicious selection of materials and its proper storage. Material handling devices increases the output, improves quality, speeds up the deliveries and decreases the cost of production. Hence, material handling should be a prime task in the designing of new projects.
Product design
Product design deals with conversion of ideas into reality. Every business organisation has to design, develop and introduce new products as a commercial strategy. Developing the new products and launching them in the market are the biggest problems faced by the organizations. The entire process of need identification to physical manufactures of product involves three functions— Design, Product Development, and manufacturing. Operation management has the responsibility of selecting the processes by which the product can be produced.
Process design
Designing of manufacturing process is another functional area of operation management. It deals with how the process required to produce a product is selected. These decisions encompass the selection of a process, choice of technology, process flow analysis and layout of the facilities. The major consideration in process design is to analyse the workflow for converting raw materials into final products.
Production Planning and Control
Production planning and control can be defined as the process of planning the production in advance, setting the exact route of each item, fixing the starting and finishing dates for each item, to give production orders to shops and to follow-up the progress of products according to orders. The principle of production planning and control lies in the statement ‘First Plan Your Work and then Work on Your Plan’. Main functions of production planning and control include Planning, Routing, Scheduling, Dispatching and Follow-up. Planning is deciding in advance what to do, how to do it, when to do it and who is to do it. Planning bridges the gap from where we are and to where we want to go. It makes it possible for things to occur which would not otherwise happen. Routing is the process of selection of path, which each part of the product will follow. Routing determines the most advantageous path to be followed for department to department and machine to machine till raw material gets its final shape.
Scheduling determines the time programme for the operations. Scheduling may be defined as the fixation of time and date for each operation as well as it determines the sequence of operations to be followed. Dispatching is concerned with the starting the processes. It gives authority so as to start a particular work, which has been already been planned under Routing and Scheduling. Therefore, dispatching is the release of orders and instruction for the starting of production. Follow-up is the process of reporting daily progress of work in each shop in a prescribed proforma and to investigate the causes of deviations from the planned performance and to take necessary actions.
Quality control
Quality Control may be defined as a system that is used to maintain desired level of quality in a product or service. It is a systematic control of various factors that affect the quality of the product. Quality Control aims at prevention of defects at the source, relies on effective feedback system and corrective action procedure. Quality Control ensures that the product of uniform acceptable quality is manufactured. It is the entire collection of activities, which ensures that the operation will produce the optimum quality products at minimum cost.
The main objectives of Quality Control are:
- To produce qualitative items
- To reduce companies cost through reduction of losses due to defects.
- To produce optimal quality at reduced price.
- To ensure satisfaction of customers with productions or services or high quality level, to build customer good will, confidence and reputation of manufacturer.
- To make inspection prompt to ensure quality control.
- To check the variation during manufacturing.
Materials management
Materials Management is that aspect of operation management function, which is concerned with the acquisition, control, and use of materials needed and flow of goods and services connected with the production process. The main objectives of Material Management are given below:
- To minimise material cost.
- To purchase, receive, transport and store materials efficiently.
- To reduce costs through simplification, standardisation, value analysis etc.
- To identify new sources of supply and to develop better relations with the suppliers.
- To reduce investment made in the inventories and to develop high inventory turnover ratios.
Maintenance management
Equipment and machinery are very important parts of the total production system. Therefore, their efficient usage is very mandatory. It is very important to see that the organisation maintains plant and machinery properly. The main objectives of Maintenance Management are
- To reduce breakdown of machineries
- To keep the machines and other facilities in a good condition.
- To ensure the availability of the machines, buildings and services required by other sections of the factory also.
- To keep the plant in good working condition.
Main areas of operations management, are
- strategic operations management – Strategic operations management is concerned with creating value for customers and gaining a competitive advantage for the organization. The goal of strategic operations management is to provide competitive advantage by aligning the transformation process, supply chain, inventory, capacity, and human resources to the organization’s overall business strategy.
- product design – The product design component of operations management focuses on the specific good or service provided. Operations managers in this area will decide on the unique aspects of the product or service.
- supply chain management – Supply chain management enables a company to effectively manage, monitor, and control all the activities along the supply chain – from supply and internal logistics to production and distribution of final products and services to customers.
- inventory management – Inventory management can be defined as the placement and control of stocked goods. Operations managers in this area will decide on such things as how much stock to keep on hand and when to replenish stock.
- forecasting – Forecasting is concerned with estimating customer demand for production planning. Operations managers in this area must predict this demand in order to produce what and when customers need.
- scheduling – Scheduling is concerned with the organization of the tasks necessary for completing the work. Operations managers decide when the staff will work and on what tasks.
- quality management – The quality management area is concerned with the process of ensuring product quality and identifying quality problems. Operations managers must decide on systems to measure quality and maintain it.
- facilities management – Facilities management is about the location and layout of premises used in the production of goods and services. Operations managers must decide on where to operate from, how big the facility needs to be, how it will be laid out, and so on.