Inventory management continues to play a critical role in the success of an organization. However, because of the domino effect businesses have on the overall economy, recently “unsold inventory created a big drag on the economy”.
Although excess inventory is an undesirable scenario, product shortages are equally as undesirable, as out-of-stock inventory is troublesome for both the business and the customer. Finding balance then becomes pivotal in the success of a business. In a recent study by the Aberdeen Group, the Best-in-Class businesses were able to “right size” their inventory by assessing products, down to the SKU level. Inventory management systems are a great way to be able to look at product information, including detailed information about each SKU.
Few inventory tools in inventory management software, along with a description of what they are, and the benefits of each.
Reorder alerts
Reorder alerts, or low inventory alerts, will appear in your inventory management system to alert the user(s) of when it’s time to reorder a certain item. The alert will appear when the product level reaches the predetermined reorder level. The inventory management system is able to do this because it is able to see the amount of each product (even if they are in multiple locations, warehouses, etc.), and see when the overall product level has become “low”.
By considering certain inventory information, such as previous sales history and expected demand, you can determine the necessary amount of buffer or safety stock for each specific item. Then, you can set the reorder alert based on this amount.
Benefits of reorder alerts are:
- reduction in time spent looking up inventory levels and purchasing
- reduction in manual efforts to look up inventory levels
- increased accuracy of inventory levels through automation.
Additionally, inventory management software may be able to make the purchasing component of reordering products even easier and quicker.
Reports
Reports can be created using the report function in an inventory management system. The data and information is pulled from the system’s database to create a report with all of the pertinent information necessary. Examples of categories of the types of reports and documents available include:
- inventory reports
- sales reports
- purchasing reports
Reports can be standard, meaning they are already available in the inventory management system. Alternatively, reports can be customized, meaning they are a modified or altered version of a standard report or personalized for a business in order to display specific information desired.
There are many reports and documents available that can all be used in a variety of ways. Depending on the exact inventory management software system, both standard and custom reports may be available.
The reports can be used to determine optimum inventory amounts down to the product level by displaying information such as:
- inventory analysis by product
- sales history by a specific customer
- inventory information by lot or serial number
- inventory reorder reports that display all products needing to be reordered
The benefit of reporting is that you are able to see a comprehensive and detailed amount of information at once. This is a time and effort-saving alternative to manually looking up all the data and/or information separately. Additionally, because reports are an automated way of collecting information, potential for error is greatly reduced.
You can check out a gallery of custom reports and documents in our previous blog article that explains how to track inventory with inventory management software.
MRP and ERP
Materials Requirement Planning (MRP) is an important concept and is increasingly becoming popular because of increasing role of computer based planning and control systems. MRP is useful for situations having products with inverted tree like structure so that the demand for parts and sub-assemblies is dependent upon the master production schedule of the end product. The MRP concept provided a very basic and different way of looking at the management of production inventories. MRP inputs are master production schedule; bill of materials and inventory status. MRP software package computes the parts requirement, and prepares production and procurement schedules. This indicates the increasing role of computers in inventory planning.
An MRP inventory management system involves four steps:
- creating a production schedule – This enables you to see what your expected output will be for the production period.
- creating a bill of materials – This bill of materials breaks a product down into its parts and indicates how many of each part is needed to meet the targets in the production schedule. This enables the company to then see how many materials it needs to build each finished part, and then categorizes the materials according to levels – from 0 to 3.
- working out how many materials are needed – In this step you compare your production needs against the current inventory levels. You can then work out how much of each material you need to order.
- determining when your suppliers can deliver the materials – To do this, you must know the supplier lead time, which is the time it takes your suppliers to deliver the materials. If you know the lead time, you can work out when is the optimum time to order.
MRP doesn’t cope very well with unexpected bottlenecks or sudden changes to the schedule. As a result, a more reliable form of MRP, called MRP II, was developed. It takes into account other factors such as routing procedures, capacity availability, and work hours. Enterprise resource planning (ERP) typically uses computer-based systems to monitor the data flow between different areas of a company. Because it uses real-time data, ERP enables inventory managers to make supply decisions based on the most up-to-date information. Inventory managers can then push supplies into the production system based on this information.
JIT System
The basis of Just-In-Time (JIT) is the concept of ideal production. It centers on the elimination of waste in the whole manufacturing environment, from raw materials through shipping. Just-In-Time is defined as “the production of the minimum number of different units, in the smallest possible quantities, at the latest possible time, thereby eliminating the need for inventory.
Just in time (JIT) is a production strategy that strives to improve a business’ return on investment by reducing in-process inventory and associated carrying costs. To meet JIT objectives, the process relies on signals or Kanban between different points, which are involved in the process, which tell production when to make the next part. Kanban are usually ‘tickets’ but can be simple visual signals, such as the presence or absence of a part on a shelf. Implemented correctly, JIT focuses on continuous improvement and can improve a manufacturing organization’s return on investment, quality, and efficiency. To achieve continuous improvement key areas of focus could be flow, employee involvement and quality.
An important aspect of JIT, is that the production has to switch over to Pull System from Push System as
PUSH SYSTEM – In this system, production quantity is based on the demand and stock in hand. The components are made in step-by-step approach in a sequential manner using the time standards for each operation.
PULL SYSTEM – In this method, the required quantity is withdrawn by the final process centre from the previous process work centre and in turn that process work centre withdraws the required quantity from its previous centre and so on. Thus this procedure works in reverse order. This is like walking into the supermarket and trying what we want, when we want and how much we want. Another significant aspect is that apart from flow type process even the layout of machines may also undergo change. Example is as
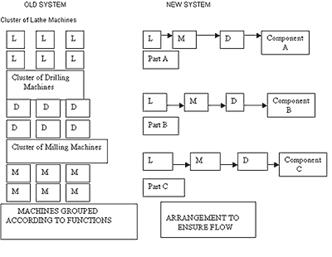
Principles of just-in-time – Just in Time (JIT) pioneered by Toyota in the 1950s and adopted successfully all over the world entails eliminating waste and improving product quality to maximize returns on investment. The basic JIT principles are to make only what is needed, when needed, and in the amount needed.
Elimination of Waste – The core principle objective of Just in Time (JIT) is to improve process efficiency by eliminating waste. Toyota’s Fujio Cho defines waste as “anything other than the minimum amount of equipment, materials, parts, and workers, which are absolutely essential to production” (Suzaki, 1987). The focus is not quick or more production but, to eliminate waste of any kind which has no value addition. JIT reduces costs and increase productivity by addressing the root of the problem by eliminating the “muda”.
Muda is a Japanese term meaning “waste” as, lean manufacturing is an Japanese management philosophy hence, Japanese terms and concepts are used extensively. There are 7 mudas or seven types of waste that are found in a manufacturing process which are
- Overproduction – An protective or “just in case” mindset usually results in overproduction. Producing more than the customer requires is waste. It causes other wastes like inventory costs, manpower and conveyance to deal with excess product, consumption of raw materials and installation of excess capacity.
- Needless Inventory – Inventory at any point is a no value-add as it ties up financial resources of the company and is exposed to the risk of damage, obsolescence, spoilage, and quality issues. It also needs space and other resources for proper management and tracking. Large inventories also cover up process deficiencies like equipment problems or poor work practices.
- Defects – Defects and broken equipment results in defective products and subsequently customer dissatisfaction, which need more resources for solving. Shipping damage is also taken as a defect. Any process, product, or service that fails to meet specifications is also a waste.
- Non-value Processing – It is also called over-processing, for which more resources are wasted in production, their wasted movement and time. Any processing that does not add value to the product is waste like in-process protective packaging. It is primarily due to extra or unnecessary manufacturing steps, using older and outdated methods or not having standard work plans.
- Excess Motion – Unnecessary motion which is also a waste occurs due to poor workflow, poor layout, housekeeping, inconsistent and undocumented work methods or lack of standardized procedures or even a deficiency in employee training. It is usually hidden as it’s not easily evident, but careful observation and worker’s communication can highlight it.
- Transport and Handling – It focus on shipping damage and includes pallets not being properly stretch wrapped (wasted material), or a truck is not loaded to use floor space efficiently or in handling, setting up or fixing a wrapping machine. Material should be shipped directly from the vendor to the location in the assembly line where it will be used also called as point-of-use-storage (POUS).
- Waiting – These are wastages in time, usually due to broken machinery, lack of trained staff, shortages of materials, inefficient planning, and waiting for material, information, equipment, tools, etc. It leads to slowed production, delayed shipments, and even missed deadlines.
The traditional approach to manufacturing management promotes a strong focus on machine and labor utilization. The view was that if managers make sure that workers and machines are always busy, then surely the factory will be productive and efficient. This approach is called the “push” system of manufacturing, where raw material and work-in-process is continuously pushed through the factory in the pursuit of high utilization. The problem with this approach is that it usually produces high levels of inventories, long lead times, overtime costs, high levels of potential rework, and workers who are competing with one another rather than working cooperatively.
In contrast to the push system, JIT espouses a “demand-pull” system that operates on the rule that work should flow to a work center only if that work center needs more work. If a work center is already occupied with work activity, the upstream work center should stop production until the downstream work center communicates a need for more material. The emphasis on maintaining high utilization is removed in a JIT environment. The focus of a JIT environment is on addressing the challenges that affect the overall effectiveness of the factory (setup time reduction, quality improvement, enhanced production techniques, waste elimination, etc. ) in meeting its strategic goals, rather than allowing excess inventory to cover up inefficiencies that reduce the factory’s competitiveness.
Quick setups to reduce lot sizes – The longer it takes, and the more expensive it is to setup equipment and labor to produce an item, the greater the quantity of items that have to be produced in a given production run. Traditional production management philosophy promoted the notion that long production runs of the same item were the key to driving down unit costs. The problem was that large production runs created large quantities of WIP and finished goods inventory that far exceeded the demand. These items would consequently cause high levels of inventory costs, long lead times, high potential rework, low flexibility in responding to customer needs, etc.
Driving down setup costs and setup times are key to dramatically improving factory competitiveness in a JIT environment. In the 1980s, the 3M company converted a factory that made a few adhesive products in long production runs into a factory that made over 500 adhesive products in small production runs. To keep unit production costs under control, 3M studied the setups on its coating machines. Since the cost of chemical waste disposal was a major part of the cost of changing over a coating machine to make another product, 3M shortened the length of hoses that needed purging and redesigned the shape of the adhesive solution holding pan on the coating machine to be shallower. 3M also used quick-connect devices, disposable filters, and work teams to speed up setups. The result was that 3M could maintain low unit costs on its coating machines while producing small lots of hundreds of products to meet market demand quickly.
Flexible resources – The enemy of JIT is uncertainty. A JIT environment thrives on predictability in customer demand, production processes, suppliers, and workers. Of course, uncertainty cannot be completely eliminated in most organizational environments.
The defense against uncertainty that cannot be driven out is to implement flexible resources that can adapt easily to changing circumstances. General-purpose, moveable equipment that can fulfill a wide variety of production requirements is one way to improve flexibility. For example, drilling machines with quick-change bits which can be wheeled into position to form new work cells allows the factory to maximize efficiency while producing exactly what is needed to satisfy immediate demand. Another example is Toyota’s use of paint canisters that attach to paint sprayers. Any car can be painted any color without having to purge hoses in switching from one color to another.
Multifunctional workers are another way to bring flexibility to the work environment. At Honeywell’s heating and cooling controls plant, workers are trained to operate all the machines on their work line. The flexibility that comes from multifunctional workers changes the nature of how work gets done. Instead of workers being trained on one machine and working independently of one another, multifunctional workers have a “big picture” view of the production line, where every worker understands all aspects of the line and how to work together to meet quality and schedule goals regardless of the circumstances.
Dashboards
In an inventory management software system, a dashboard is an on-screen graphical display of information. Different information and data, which have been pulled from the system’s database, can be viewed from the dashboard.
Depending on the user(s) and their roles in the business, the dashboard can be used in a variety of ways to display a wide range of information. For instance, a small business owner could use their dashboard to display information such as monthly sales information, inventory levels per location, etc. On the other hand, a warehouse manager might use their dashboard to display current inventory levels in their warehouse, orders that are scheduled to be received and shipped out, etc.
Again, such as with reports, a dashboard is a great tool for compiling assorted data and information. Because the inventory management system collects and displays this multitude of information, both time and effort are saved, while accuracy is increased.
Barcoding and mobile systems
Barcoding and mobile systems are a combination of hardware and software that allow your business to assign, scan, and manage barcodes.
Barcode hardware includes items such as barcode scanners and label printers. Barcode software is the system that manages the barcoding and inventory information. To learn more about barcoding hardware and software, check out one of our previous blogs on barcoding inventory management.
For an effective inventory management system, barcoding and mobile solutions can be utilized to:
- conduct inventory counts
- verify inventory
- adjust inventory
The benefits of using barcoding and mobile systems are ease, speed, and accuracy. For instance, conducting an inventory count by using a barcode scanner is easier, quicker, and more accurate than conducting an inventory count manually.