It refers to the concept of moving one work piece at a time between operations within a work cell uninterrupted in time, sequence, substance or extent. One-piece flow is the method of production in which operators or machines work on single units and pass them along to the next process when requested. The most common example of one-piece flow is the assembly line. An operator at each station works on a unit. All of this work-in process (one unit per operator or automatic machine) moves in synchronization to the next station.
One-Piece Flow is also known by other names as Make-one, Move-one or Single-piece Flow or Continuous Flow and Flow Manufacturing.
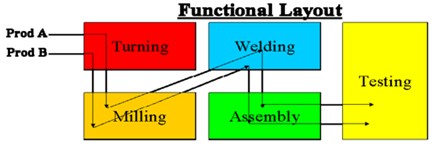
In a typical MRP batch-and-queue manufacturing environment as illustrated above, parts move from functional area to functional area in batches, and each processing step or set of processing steps is controlled independently by a schedule. There is little relationship between each manufacturing step and the steps immediately upstream or downstream. This result in
- Large amounts of scrap when a defect is found because of large batches of WIP
- Long manufacturing lead time
- Poor on-time delivery and/or lots of finished goods inventory to compensate
- Large amounts of WIP
When we achieve connected flow, there is a relationship between processing steps: That relationship is either a pull system such as a supermarket or FIFO lane or a direct link (one-piece flow). As illustrated below, one-piece flow is the ideal method for creating connected flow because product is moved from step to step with essentially no waiting (zero WIP).
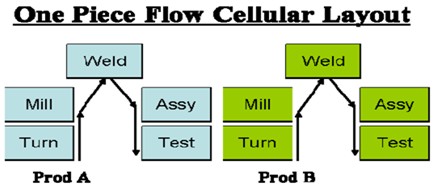