Details on the three principal forms of hydrogen storage (gas, liquid, and solid) are discussed.
Gaseous Hydrogen
The most common method to store hydrogen in gaseous form is in steel tanks, although lightweight composite tanks designed to endure higher pressures are also becoming more and more common. Cryogas, gaseous hydrogen cooled to near cryogenic temperatures, is another alternative that can be used to increase the volumetric energy density of gaseous hydrogen. A more novel method to store hydrogen gas at high pressures is to use glass microspheres.
Composite tanks – A schematic of a typical high-pressure, C-fibre-wrapped H2 storage composite tank is shown in figure below.
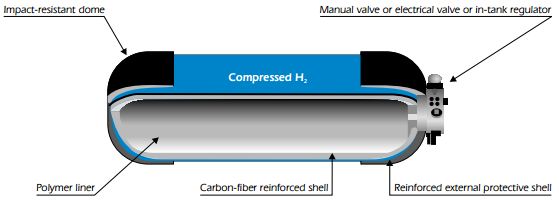
The are several advantages with such composite tanks. Their low weight meets key targets, and the tanks are already commercially available, well-engineered and safety-tested, since extensive prototyping experience exists. They also meet codes that are accepted in several countries for pressures in the range of 350-700 bar. Composite tanks require no internal heat exchange and may be usable for cryogas. Their main disadvantages are the large physical volume required (which does not meet targets), the fact that the ideal cylindrical shape makes it difficult to conform storage to available space, their high cost (500-600 USD/kg H2), and the energy penalties associated with compressing the gas to very high pressures. There are also some safety issues that still have not been resolved, such as the problem of rapid loss of H2 in an accident.
Glass microspheres – The basic concept for how glass microspheres can be used to store hydrogen gas onboard a vehicle can be described by three steps: charging, filling and discharging. First, hollow glass spheres are filled with H2 at high pressure (350-700 bar) and high temperature (ca. 300 °C) by permeation in a high-pressure vessel. Next, the microspheres are cooled down to room temperature and transferred to the low-pressure vehicle tank. Finally, the microspheres are heated to ca. 200-300 °C for controlled release of H2 to run the vehicle.
The main problem with glass microspheres is the inherently low volumetric density that can be achieved and the high pressure required for filling. The glass microspheres slowly leak hydrogen at ambient temperatures. Another practical challenge is that there is too much breakage during cycling. The main operational challenge is the need to supply heat at temperatures higher than are available from the PEM fuel cell (ca. 70-80 °C). The high temperature required (ca. 300 °C) also makes rapid response-control difficult. However, there do exist some clear advantages. Glass microspheres have the potential to be inherently safe as they store H2 at a relatively low pressure onboard and are suitable for conformable tanks. This allows for low container costs. The significant technical advantage is the demonstrated storage density of 5.4 wt.% H2.
Liquid Hydrogen
The most common way to store hydrogen in a liquid form is to cool it down to cryogenic temperatures (–253 °C). Other options include storing hydrogen as a constituent in other liquids, such as NaBH4 solutions, rechargeable organic liquids, or anhydrous ammonia NH3.
Cryogenic liquid hydrogen (LH2) – Cryogenic hydrogen, usually simply referred to as liquid hydrogen (LH2), has a density of 70.8 kg/m3 at normal boiling point (–253 °C). (Critical pressure is 13 bar and critical temperature is –240 °C.) The theoretical gravimetric density of LH2 is 100%, but only 20 wt. % H2 of this can be achieved in practical hydrogen systems today. On a volumetric basis, the respective values are 80 kg/m3 and 30 kg/m3. This means that liquid hydrogen has a much better energy density than the pressurised gas solutions mentioned above. However, it is important to recall that about 30-40% of the energy is lost when LH2 is produced. The other main disadvantage with LH2 is the boil-off loss during dormancy, plus the fact that super-insulated cryogenic containers are needed. The general public’s perception of LH2 as an unsafe and very high-tech system should not be underestimated. The main advantage with LH2 is the high storage density that can be reached at relatively low pressures.
Liquid hydrogen has been demonstrated in commercial vehicles (particularly by BMW), and in the future it could also be co-utilized as aircraft fuel.
NaBH4 solutions – Borohydride (NaBH4) solutions can be used as a liquid storage medium for hydrogen. The catalytic hydrolysis reaction is
NaBH4 (l) + 2H2 O (l) à 4H2 (g) + NaBO2(s) (ideal reaction) Eqn. 1
The theoretical maximum hydrogen energy storage density for this reaction is 10.9 wt.% H2, the ideal reaction being 4H2/(NaBH4 + 2H2O). The specific cost (USD/kg) of hydrogen storage using NaBH4 solutions is quite simple to calculate:
Cost H2= 4.69 × Cost NaBH4 (ideal reaction) Eqn. 2
The main advantage with using NaBH4 solutions is that it allows for safe and controllable onboard generation of H 2 . The main disadvantage is that the reaction product NaBO2 must be regenerated back to NaBH4 off-board. Although use of NaBH4 solutions in vehicles may be prohibitively expensive (the cost of NaBH4 regeneration must be reduced from present 50 USD/kg to less than 1 USD/kg), there do exist a few commercial companies that promote the technology (Millennium Cell in the U.S. and MERIT in Japan). The required cost reduction is unlikely because of the unfavourable thermodynamics. However, NaBH4 solutions may be usable in high-value portable and stationary applications.
Rechargeable organic liquids – Some organic liquids can also be used to indirectly store hydrogen in liquid form. The following three steps summarise the basic concept. First, an organic liquid is dehydrogenated (in a catalytic process) to produce H2 gas onboard. Second, the dehydrogenated product is transported from the vehicle tank to a central processing plant, while simultaneously refilling the tank with fresh H 2 -rich liquid. Finally, the H2 -depleted liquid needs to be re-hydrogenated, brought back to the starting compound and returned to the filling station.
Solid Hydrogen
Storage of hydrogen in solid materials has the potential to become a safe and efficient way to store energy, both for stationary and mobile applications. There are four main groups of suitable materials: carbon and other high surface area materials; H2O-reactive chemical hydrides; thermal chemical hydrides; and rechargeable hydrides.
Carbon and other high surface area materials – Carbon-based materials, such as nanotubes and graphite nanofibers, have received a lot of attention in the research community and in the public press over the last decade. The general consensus today is that the high H2-storage capacities (30-60 wt%) reported a few years ago are impossible and were the result of measurement errors. Pure H2 molecular physisorption has been clearly demonstrated, but is useful only at cryogenic temperatures (up to ca. 6 wt.% H2 ), and extremely high surface area carbons are required. Pure atomic H-chemisorption has been demonstrated to ca. 8 wt.% H 2, but the covalent-bound H is liberated only at impractically high temperatures (above ca. 400 °C). Room temperature adsorption up to a few wt.% H2 is occasionally reported, but has not been reproducible. This requires a new bonding mechanism with energies between physisorption and strong covalent chemisorption. The surface and bulk properties needed to achieve practical room temperature storage are not clearly understood, and it is far from certain that useful carbon can be economically and consistently synthesised.
Borohydrides – Borohydrides have much higher potential capacities than the alanates. However, they are also much less studied than alanates. In general borohydrides are too stable, and are not as reversible as alanates, but are at the same time considered safer than the alanates. Lately there has been some preliminary progress on LiBH4, particularly on reversibility and destabilisation.
Chemical hydrides (H2O-reactive) – Chemical hydrides can be handled in a semi-liquid form, such as mineral oil slurry. In this form, hydrides can be pumped and safely handled. Controlled injection of H2O during vehicle operation is used to generate H2 via hydrolysis reactions. The liberation of H2 is exothermic and does not require waste heat from the vehicle power source. The theoretical potential storage density is around 5-8 wt.% H2. In practical systems, one approach for NaH is to encapsulate small spheres in polymeric shells. In general, MgH2 probably offers the best combination of H2-yield and affordability. The key R&D task to be addressed is lowering the cost of processing the spent hydroxide back into the starting hydride. In all cases, this is an energy-intensive process, and it is doubtful that costs can be reduced to vehicle targets.
Chemical hydrides (thermal) – Ammonia borane is another group of chemical hydrides that potentially could be used to store hydrogen in a solid state. Results show that NH4 BH4 can be thermally decomposed in 4 steps with very high H2 yields. However, the reactions are not reversible, and off-board regeneration is required. Research has shown that nesting in mesoporous “scaffolds” greatly increases the decomposition kinetics. The possibility of gaseous boranes in the evolved H2 must be carefully studied. They are toxic and would likely contaminate the fuel cell catalysts.