It is a top down, deductive failure analysis in which an undesired state of a system is analyzed using Boolean logic to combine a series of lower-level events. This analysis method is mainly used in the fields of safety engineering and reliability engineering to understand how systems can fail, to identify the best ways to reduce risk or to determine (or get a feeling for) event rates of a safety accident or a particular system level (functional) failure.
Fault trees are built using gates and events (blocks). The two most commonly used gates in a fault tree are the AND and OR gates. As an example, consider two events (or blocks) comprising a Top Event (or a system). If occurrence of either event causes the top event to occur, then these events (blocks) are connected using an OR gate. Alternatively, if both events need to occur to cause the top event to occur, they are connected by an AND gate. As a visualization example, consider the simple case of a system comprised of two components, A and B, and where a failure of either component causes system failure. The system RBD is made up of two blocks in series
Name of Gate | Classic FTA Symbol | Description |
AND | ![]() | The output event occurs if all input events occur. |
OR | ![]() | The output event occurs if at least one of the input events occurs. |
Taking an example, an inspection of a system reveals that any of the following failures will cause the system to fail
- Failure of components 1 and 2.
- Failure of components 3 and 4.
- Failure of components 1 and 5 and 4.
- Failure of components 2 and 5 and 3.
In probability terminology it can be denoted as (1 And 2) Or (3 And 4) Or (1 And 5 And 4) Or (2 And 5 And 3). The consecutive fault tree as
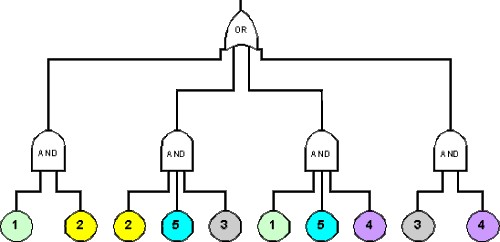
Fault tree analysis (FTA) is a top down, deductive failure analysis in which an undesired state of a system is analyzed using Boolean logic to combine a series of lower-level events. This analysis method is mainly used in the fields of safety engineering and reliability engineering to understand how systems can fail, to identify the best ways to reduce risk or to determine (or get a feeling for) event rates of a safety accident or a particular system level (functional) failure. FTA is used in the aerospace, nuclear power, chemical and process, pharmaceutical, petrochemical and other high-hazard industries; but is also used in fields as diverse as risk factor identification relating to social service system failure. FTA is also used in software engineering for debugging purposes and is closely related to cause-elimination technique used to detect bugs.
In aerospace, the more general term “system Failure Condition” is used for the “undesired state” / Top event of the fault tree. These conditions are classified by the severity of their effects. The most severe conditions require the most extensive fault tree analysis. These “system Failure Conditions” and their classification are often previously determined in the functional Hazard analysis.
FTA can be used to:
- understand the logic leading to the top event / undesired state.
- show compliance with the (input) system safety / reliability requirements.
- prioritize the contributors leading to the top event – Creating the Critical Equipment/Parts/Events lists for different importance measures.
- monitor and control the safety performance of the complex system (e.g., is a particular aircraft safe to fly when fuel valve x malfunctions? For how long is it allowed to fly with the valve malfunction?).
- minimize and optimize resources.
- assist in designing a system. The FTA can be used as a design tool that helps to create (output / lower level) requirements.
- function as a diagnostic tool to identify and correct causes of the top event. It can help with the creation of diagnostic manuals / processes.