Enterprises Resource Planning (ERP) is software based production planning and inventory control system used to manage manufacturing processes. Although it is not common nowadays, it is possible to conduct ERP by hand as well.
An ERP system is intended to simultaneously meet three objectives:
- Ensure materials and products are available for production and delivery to customers.
- Maintain the lowest possible level of inventory.
- Plan manufacturing activities, delivery schedules and purchasing activities.
The scope of ERP in manufacturing
Manufacturing organizations, whatever their products, face the same daily practical problem – that customers want products to be available in a shorter time than it takes to make them. This means that some level of planning is required.
Companies need to control the types and quantities of materials they purchase, plan which products are to be produced and in what quantities and ensure that they are able to meet current and future customer demand, all at the lowest possible cost. Making a bad decision in any of these areas will make the company lose money. A few examples are given below:
- If a company purchases insufficient quantities of an item used in manufacturing, or the wrong item, they may be unable to meet contracts to supply products by the agreed date.
- If a company purchases excessive quantities of an item, money is being wasted – the excess quantity ties up cash while it remains as stock and may never even be used at all. However, some purchased items will have a minimum quantity that must be met, therefore, purchasing excess is necessary.
- Beginning production of an order at the wrong time can cause customer deadlines to be missed.
ERP is a tool to deal with these problems. It provides answers for several questions:
- What items are required?
- How many are required?
- When are they required?
ERP can be applied both to items that are purchased from outside suppliers and to sub-assemblies, produced internally, that are components of more complex items.
The data that must be considered include:
- The end item (or items) being created. This is sometimes called Independent Demand, or Level “0” on BOM (Bill Of Material).
- How much is required at a time.
- When the quantities are required to meet demand.
- Shelf life of stored materials.
- Inventory status records. Records of net materials available for use already in stock (on hand) and materials on order from suppliers.
- Bills of materials. Details of the materials, components and subassemblies required to make each product.
- Planning Data: This includes all the restraints and directions to produce the end items. This includes such items as: Routings, Labor and Machine Standards, Quality and Testing Standards, Pull/Work Cell and Push commands, Lot sizing techniques (i.e. Fixed Lot Size, Lot-For-Lot, Economic Order Quantity), Scrap Percentages, and other inputs.
Outputs
There are two outputs and a variety of messages/reports:
- Output 1 is the “Recommended Production Schedule” which lays out a detailed schedule of the required minimum start and completion dates, with quantities, for each step of the Routing and Bill of Material required to satisfy the demand from the MPS.
- Output 2 is the “Recommended Purchasing Schedule”. This lays out both the dates that the purchased items should be received into the facility AND the dates that the Purchase order , or Blanket Order Release should occur to match the production schedules.
Messages and Reports
- Purchase orders . An order to a supplier to provide materials.
- Reschedule notices. These recommend canceling, increasing, delaying or speeding up existing orders.
Note that the outputs are recommended. Due to a variety of changing conditions in companies, since the last ERP / ERP system Re-Generation, the recommended outputs need to be reviewed by trained people to group orders for benefits in set-up or freight savings. These actions are beyond the linear calculations of the ERP computer software.
Problems with ERP systems
The major problem with ERP systems is the integrity of the data. If there are any errors in the inventory data, the bill of material (commonly referred to as ‘BOM’) data, or the master production schedule, then the outputted data will also be incorrect. Most vendors of this type of system recommend at least 99% data integrity for the system to give useful results.
Another major problem with ERP systems is the requirement that the user specify how long it will take a factory to make a product (NOTE: IRRESPECTIVE OF CONSIDERING PRODUCTION CAPACITY, BREAK DOWN WORKER AVAILABILITY WHICH ERP2 INCLUDES, AND PRODUCE OUTPUTS CONSIDERING ALL THESE FACTORS) from its component parts (assuming they are all available). Additionally, the system design also assumes that this “lead time” in manufacturing will be the same each time the item is made, without regard to quantity being made, or other items being made simultaneously in the factory.
A manufacturer may have factories in different cities or even countries. It is no good for an ERP system to say that we do not need to order some material because we have plenty thousands of miles away. The overall ERP system needs to be able to organize inventory and needs by individual factory, and intercommunicate needs in order to enable each factory to redistribute components in order to serve the overall enterprise.
This means that other systems in the enterprise need to work properly both before implementing an ERP system, and into the future. For example systems like variety reduction and engineering which makes sure that product comes out right first time (without defects) must be in place. Production may be in progress for some part, whose design gets changed, with customer orders in the system for both the old design, and the new one, concurrently. The overall ERP system needs to have a system of coding parts such that the ERP will correctly calculate needs and tracking for both versions. Parts must be booked into and out of stores more regularly than the ERP calculations take place. Note, these other systems can well be manual systems, but must interface to the ERP. For example, a ‘walk around’ stock take done just prior to the ERP calculations can be a practical solution for a small inventory (especially if it is an “open store”).
The other major drawback of ERP is that takes no account of capacity in its calculations. This means it will give results that are impossible to implement due to manpower or machine or supplier capacity constraints. However this is largely dealt with by ERP 2.
Generally, ERP II refers to a system with integrated financials. An ERP II system can include finite / infinite capacity planning. But, to be considered a true ERP II system must also include financials.
In the (or ERP2) concept, fluctuations in forecast data are taken into account by including simulation of the master production schedule, thus creating a long-term control. A more general feature of ERP2 is its extension to purchasing, to marketing and to finance (integration of all the function of the company), ERP has been the next step.
Two basic characteristics of ERP:
- ERP derives demand for components, subassemblies, materials, etc., from demand for and production schedules of parent items.
- ERP offsets replenishment orders (purchase orders or production schedules) relative to the date when replenishment is needed
Information Needed for ERP
- Demand for all products.
- Lead times for all finished goods, components, parts and raw materials
- Lot sizing policies for all parts
- Opening inventory levels
- Safety stock requirements
- Any orders previously placed but which haven’t arrived yet
Information Obtained from ERP
- Planned orders: replenishment orders to be released at a future time
- Order release notice: notices to release planned orders
- Action notices: notices to expedite, de-expedite, or cancel orders, or to change order quantities or due dates
- Priority reports: information regarding which orders should be given priority
- Inventory status information
- Performance reports such as inactive items, actual lead times, late orders, etc.
ERP Inputs
- Master Production Schedule
- Product Structure
- Inventory Levels
Lot Sizing Choices in ERP
Lot sizing:
Determining the lot size (order quantity or production quantity) of an item
Static lot sizing rule:
A decision rule that orders the same quantity each time an order is placed.
- Tend to generate higher average on-hand inventory because they create inventory remnants.
- Can provide extra safety stock.
Dynamic lot sizing rule:
- A decision rule that changes the order quantity with each order, typically so that each order is just large enough to prevent shortages over a specified time period.
- Tend to cause instability by tying lot-size to gross requirements.
- Lower-level components may not be able to respond sufficiently fast to changes in requirements.
Static Lot-sizing Rules
Fixed order quantity (FOQ)
- Order (or produce) a fixed quantity, or a multiple of that fixed quantity.
Economic Order Quantity (EOQ)
- Order (or produce) the economic order quantity, plus any additional items needed to replenish safety stock if it has fallen below its desired level.
- Yields minimum total setup/ordering plus holding costs.
- Assumes relatively constant demand.
Dynamic Lot-sizing Rules
Lot-for-Lot (L4L)
- Order (or produce) exactly the quantity required in each period to satisfy gross requirements and to maintain safety stock at its required level.
- Simple to use, and agrees with Just-In-Time philosophy of ordering/producing only when required.
- Lot size can be modified easily for purchase discounts or restrictions, scrap allowances, process constraints, etc.
- Minimizes on-hand inventory, but maximizes number of orders placed (so can be expensive if setup/ordering costs are significant).
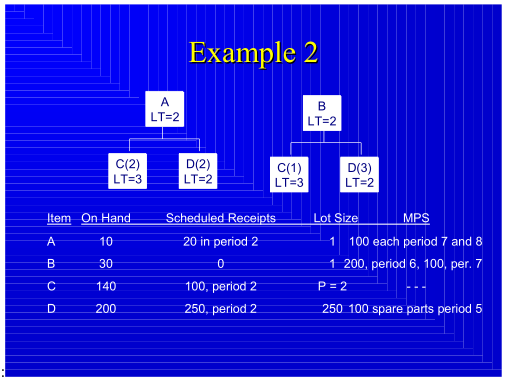
Periodic Order Quantity (POQ)
- Order/produce a quantity equal to the gross requirements for P periods minus any items in on-hand inventory plus any additional items needed to replenish safety stock if it has fallen below its desired level.
- Restores safety stock and covers exactly P periods of gross requirements.
- Reduces on-hand inventory by attempting to match the quantity ordered to the quantity required.
Example 1:
Completing ERP Tables
Objective:
The purpose of ERP is to schedule orders for end items and the components of those end items. We wish to determine when to release orders and how much to order.
Step 1
Begin with the end items. Complete one table at a time.
- Schedule the gross requirements, GR.
- Enter records for any scheduled receipts, SR.
- Consider GR, SR and inventory, I, to determine timing and size of orders we will plan to receive, PR. These are orders which we must receive to meet demand.
PRt = It-1 + SRt – GRt – It
- Use the lead time to schedule the planned order releases, POR, so that the orders are received when they are needed.
Time of POR = Time of PR – L
- A POR for an end item in week t becomes a GR in week t for every component part of the end item.
Step 2
Schedule the components. If a component occurs at more than one level it is scheduled at the deepest level so that you will know all demand for parents of the component before you try to schedule the component.
Level 1 Components:
The POR’s for end items are scheduled as GR’s for level 1 components. Any spare parts orders are scheduled as GR’s also.
- Complete the table as discussed in step 1.
Repeat the process for all components.
For each component the gross requirements come from planned order releases for all direct parents of the component and from any orders for spare parts.
The final result will be planned orders (quantity and timing) for end products and all of their component which must be made in order to meet demand.
Example 2
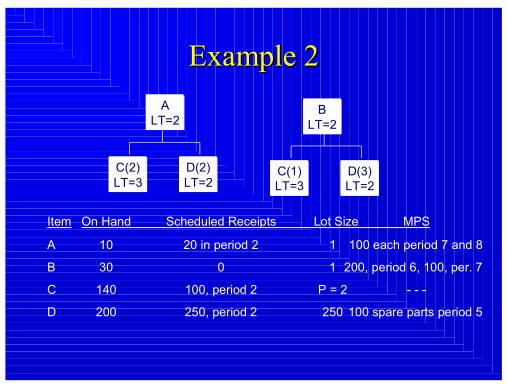
Implementation of Materials Requirements Planning Systems
Favorable environments for ERP:
- batch manufacturing environment
- stable demand
- limited number of products
- large number of bill-of-materials levels
- large lot sizes
Some conditions which are less favorable for ERP
Process-focused environments:
- many customized products
- small production volumes
- small number of bill-of-materials levels
Just-In-Time environments:
- small batch sizes
- demand pulls parts and components through the system
Other Types of ERP Systems
Closed-loop ERP:
ERP system that provides feedback to other stages of the production plan, such as the aggregate production plan, capacity plan, and Master Production Schedule.
Manufacturing Resource Planning (ERP II)
A planning system that uses all outputs of a ERP system to integrate production, marketing, and financial plans.
Distribution Resource Planning (DRP)
A time-phased stock replenishment technique for distribution networks based on ERP procedures and logic.
Is ERP a Planning System?
The ERP (Enterprises Resource Planning) concept exists since the 60s of the last century. It is the basis for most software systems supporting production planning and control in industrial practice. Most of these so-called ERP systems provide good assistance for order processing, data handling and inventory book-keeping, but they do not support planning.
A typical ERP system follows a successive planning concept, as depicted in the following figure.
Master Production Scheduling.
Based on existing customer orders and a medium-term aggregate production plan Master Production Scheduling (MPS) prepares a short-term production plan for end or rather main products. The planning result is the Master Production Schedule, which is commonly referred to as the MPS.
Material Requirements Planning.
The next step, Material Requirements Planning (ERP), uses the MPS as a starting point and computes derived demands for all components required for the production of the end products. The planning data used are the bill-of-materials structure (BOM structure, Gozinto structure), the current inventory status (including planned receipts) and planned lead times. Within this planning step lot sizes are computed under the assumption that infinite capacity is available. Result of these computations is planned production quantities per item and period.
Capacity Requirements Planning.
Next, for each operation required to make the products the planned starting time and ending time are computed with the help of standard project planning algorithms, such as the Critical Path Method (CPM). Again, capacities of the resources are neglected (infinite loading). Following this planning step, the capacity requirements resulting from infinite loading are tabulated and graphed. Usually the comparison with the available capacities shows that the production plan developed so far is infeasible.
This is the point in time when adjustment of the production plan by the human planner comes into play. Usually based on experience, the planner tries to shift operations on the time axis in order to generate a feasible production schedule. If this is not possible due to conflicts between the resource requirements of different operations, the capacity is extended by overtime, if possible. In general, a human does not have the capability to solve this complicated combinatorial optimization problem, which is a variant of the so-called Resource-Constrained Project Planning Problem (RCPSP).
Production Control
In the last planning, for the upcoming short-term planning horizon production orders are released and assigned to the resources. For each resource orders are scheduled with the help of simple priority rules.
Critique of the ERP concept
Basically, the ERP concept is nothing else than the automation of order processing procedures that in earlier days have been done manually. Planning methods that support decision making in the sense that a feasible production plan is developed are not applied. The ERP concept has been criticized by many scientists as well as practitioners in a large number of publications. Its flaws are system-immanent and cannot be deleted by modern data base methods, user interfaces and faster computers. The major flaws to be criticized are:
- The medium-term aggregated production planning which aims at the coordination of sales and operations planning is not supported. Usually the production plan is equated to the sales plan. With scarce resources, however, these both plans must differ.
- The production lot sizes are computed for each item in isolation without consideration of the interdependencies between predecessor and successor items in a multi-level BOM structure. The competition of items for resources is neglected, which leads to infeasible production plans. In addition, the cost-related interdependencies between a parent item and its components are not considered. Whitin the ERP planning phase a successive planning of the items is performed (first requirements computation, then lot sizing), based on an ordering of the items according to their low level codes.
- In the ERP phase and in the Capacity Requirements Planning phase so-called “planned lead times” are used. These are stored as a resource-independent characteristic of an item in the production data base and are often not changed for years. The planned lead time includes estimates of transportation times and of waiting time due to scarcety of production resources. However, it is obvious that the waiting time for a resource depends on the workload of the resource. As the workload and, consequently, the bottleneck status of a resource changes over time, it does not make sense to store the waiting time (as part of the planned lead time) in a data base. The lead times are a result of the planning and not a given.
All planning phase suffer from the severe flaw, that the scarce capacities of the resources are completely neglected in the planning. Only immediately before the start of the production operation on the job shop level the infeasibility of a production schedule is recognized. But at this point in time, it is too late. Delivery delays and superfluous inventory are the consequence.
Material Requirements Planning – Calculations
ERP is basically is a demand explosion concept without any planning functionality, as will be shown below.
The ERP calculations are as follows:
Sort items according to their low level code.
Consider each item in sequence and perform the following steps:
- Get external demand (from the master production schedule), sif any
- Compute derived demands
Get available inventory (from the inventory records)
Compute net demand
Compute lot sizes (usually with the a heuristic for the single level dynamic not sizzling problem
Offset lots according to the planned lead time and fix production dates
Here is a numerical Example
Consider the following Bill of material (BOM) structure with seven items:
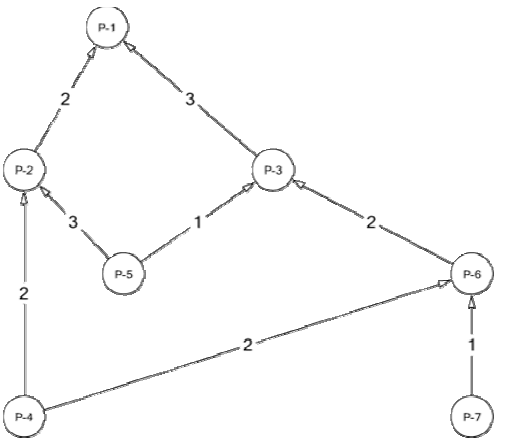
There is a demand of 35 units in period 8 for the end product. The initial inventory on hand for each item is given in the following table:
Product | P-1 | P-2 | P-3 | P-4 | P-5 | P-6 | P-7 |
Inventory | 10 | 15 | 20 | 10 | 10 | 10 | 30 |
For each item 5 unit of safety stock are required. The remaining data are shown in the following table:
Product | Setup Costs | Holding Costs | Setup Times | Processing Times | Resource | Lead Time |
P-1 | 100 | 4 | 10 | 1 | 1 | 1 |
P-2 | 100 | 3 | 10 | 1 | 1 | 2 |
P-3 | 100 | 2 | 10 | 1 | 2 | 1 |
P-4 | 100 | 1 | 10 | 1 | 2 | 1 |
P-5 | 100 | 1 | 10 | 1 | 3 | 2 |
P-6 | 100 | 1 | 10 | 1 | 3 | 3 |
P-7 | 100 | 1 | 10 | 1 | 4 |
A formal computerized approach to inventory planning, manufacturing scheduling, supplier scheduling, and overall corporate planning. The material requirements planning (ERP) system provides the user with information about timing (when to order) and quantity (how much to order), generates new orders, and reschedules existing orders as necessary to meet the changing requirements of customers and manufacturing. The system is driven by change and constantly recalculates material requirements based on actual forecast orders. It makes adjustments for possible problems prior to their occurrence, as opposed to traditional control systems, which looked at more historical demand and reacted to existing problems. Material resource planning (ERP II) evolved from material requirements planning when it was recognized that most major data needed to manage a manufacturing or distribution firm could be obtained from the material requirements planning information. The ability of a material resource planning system to meet the various needs of manufacturing, materials, and marketing personnel within a changing business environment contributes to its growing implementation by manufacturing companies.
The logic of the material requirements planning system is based on the principle of dependent demand, a term describing the direct relationship between demand for one item and demand for a higher-level assembly part or component. For example, the demand for the number of wheel assemblies on a bicycle is directly related to the number of bicycles planned for production; further, the demand for tires is directly dependent on the demand for wheel assemblies. In most manufacturing businesses, the bulk of the raw material and in-process inventories are subject to dependent demand. Dependent demand quantities are calculated, while independent demand items are forecast. Independent demand is unrelated to a higher-level item which the company manufactures or stocks. Generally, independent demand items are carried in finished goods inventory and subject to uncertain end customer demand. Spare parts or replacement requirements for a drill press are an example of an independent demand item.