The use of the term “technology” has changed significantly over the last 200 years. Before the 20th century. The human species’ use of technology began with the conversion of natural resources into simple tools. The prehistoric discovery of how to control fire and the later Neolithic Revolution increased the available sources of food and the invention of the wheel helped humans to travel in and control their environment. Developments in historic times, including the printing press, the telephone, and the Internet, have lessened physical barriers to communication and allowed humans to interact freely on a global scale. The steady progress of military technology has brought weapons of ever-increasing destructive power, from clubs to nuclear weapons.
Keeping up with the latest building technology is difficult, due to the huge number of advances every year. But if maintenance and engineering managers do not keep up, they risk missing opportunities to decrease costs and improve tenant comfort and staff productivity.
As managers, it is unequivocally important to be aware of the newest technology and to understand its benefits and limitations. Fail to do this, and managers risk getting run over by technology advances.
When a piece of older equipment nears its end of life, one option is to spend a bit more money on a more efficient, state-of-the-art replacement. The small additional capital cost will often be paid back with energy savings in just a couple of years, and over the life of the equipment, that can mean big savings for the facility — which is good news for those on the corporate level.
Many new technologies can benefit every type of facility, so managers have no one to blame but themselves for missing the opportunities. They include:
Lighting. Light-emitting-diode (LED) technology and other high-efficiency products are getting a big push because lighting is such a large percentage of energy use in buildings. But does an LED fixture that costs $400 and uses 20 percent less energy than a $200 high-efficiency T8 make fiscal sense? Is a $200 high-efficiency T8 better than a $120 run-of-the-mill T8? The answers often depend on utility rates and labor costs, but knowing the limitations allows managers to leverage the capital budget most effectively.
Motors and drives. Variable-frequency drives (VFD) and high-efficiency motors are no-brainers. Motors die all the time, and the additional costs to replace the dead motor with a VFD and a high-efficiency unit is more than offset by the energy savings.
Exhaust controls. Each cubic foot per minute (CFM) of exhaust costs about $5.50 per year, so use VFDs and static duct-pressure monitoring to control exhaust. Imagine a facility with three 5,000 CFM fans running constantly. Reducing the load by 20 percent over the course of the year results in more than $16,000 in savings.
Controls. Consider an intelligent building- or lighting-control system. Control HVAC systems to operate only when needed, make them automatically adjustable to the actual load, and use free cooling in cold weather. Have the lighting-control system automatically turn out lights in unoccupied buildings or spaces.
Uninterruptible power supply (UPS). The typical dual-conversion UPS is 90-97 percent efficient, losing a good deal of its power in the form of heat. Flywheel and high-efficiency UPS that use line-interactive or hybrid technology — dual conversion on demand — can be 96-99 percent efficient. Batteries are a main source of failure and maintenance costs, and flywheel technology can decrease the rates of failure and maintenance costs dramatically. For example, a 500-kilowatt UPS system in a data center in an region with an energy rate of $0.12 per kilowatt-hour will save $16,000 per year if it increases its UPS efficiency by 3 percent. That will make any CFO happy.
Retro commissioning. A new building might be highly efficient when it opens, but as time passes, the building requires retro commissioning to maintain its efficiency. Technicians lock out controls for maintenance but put them back in place. They set a motor on manual for a specific event but never put it back to automatic. All of these moves will use more energy, and retro commissioning can identify and solve all of them.
Building automation is the automatic centralized control of a building’s heating, ventilation and air conditioning, lighting and other systems through a building management system or building automation system (BAS). The objectives of building automation are improved occupant comfort, efficient operation of building systems, and reduction in energy consumption and operating costs, and improve life cycle of utilities.
Building automation is an example of a distributed control system – the computer networking of electronic devices designed to monitor and control the mechanical, security, fire and flood safety, lighting (especially emergency lighting), HVAC and humidity control and ventilation systems in a building.
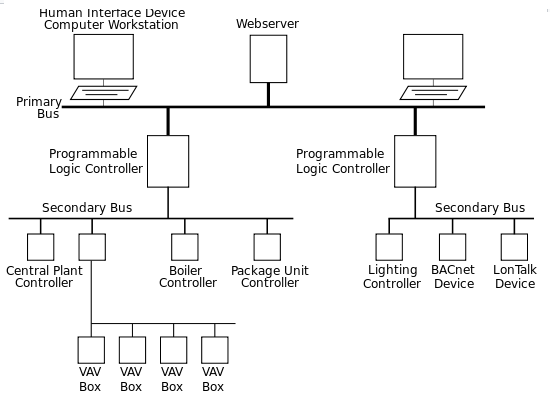
BAS core functionality keeps building climate within a specified range, provides light to rooms based on an occupancy schedule (in the absence of overt switches to the contrary), monitors performance and device failures in all systems, and provides malfunction alarms to building maintenance staff. A BAS should reduce building energy and maintenance costs compared to a non-controlled building. Most commercial, institutional, and industrial buildings built after 2000 include a BAS. Many older buildings have been retrofitted with a new BAS, typically financed through energy and insurance savings, and other savings associated with pre-emptive maintenance and fault detection.
A building controlled by a BAS is often referred to as an intelligent building, “smart building”, or (if a residence) a “smart home”. Commercial and industrial buildings have historically relied on robust proven protocols (like BACnet) while proprietary protocols (like X-10 were used in homes. Recent IEEE standards (notably IEEE 802.15.4, IEEE 1901 and IEEE 1905.1, IEEE 802.21, IEEE 802.11ac, IEEE 802.3at) and consortia efforts like nVoy (which verifies IEEE 1905.1 compliance) or QIVICON have provided a standards-based foundation for heterogeneous networking of many devices on many physical networks for diverse purposes, and quality of service and failover guarantees appropriate to support human health and safety. Accordingly commercial, industrial, military and other institutional users now use systems that differ from home systems mostly in scale. See home automation for more on entry level systems, nVoy, 1905.1, and the major proprietary vendors who implement or resist this trend to standards integration.
Almost all multi-story green buildings are designed to accommodate a BAS for the energy, air and water conservation characteristics. Electrical device demand response is a typical function of a BAS, as is the more sophisticated ventilation and humidity monitoring required of “tight” insulated buildings. Most green buildings also use as many low-power DC devices as possible, typically integrated with power over Ethernet wiring, so by definition always accessible to a BAS through the Ethernet connectivity. Even a passive design intended to consume no net energy whatsoever will typically require a BAS to manage heat capture, shading and venting, and scheduling device use.
Buses and protocols
Most building automation networks consist of a primary and secondary bus which connect high-level controllers (generally specialized for building automation, but may be generic programmable logic controllers) with lower-level controllers, input/output devices and a user interface (also known as a human interface device). ASHRAE’s open protocol BACnet or the open protocol LonTalk specify how most such devices interoperate. Modern systems use SNMP to track events, building on decades of history with SNMP-based protocols in the computer networking world.
Physical connectivity between devices was historically provided by dedicated optical fiber, ethernet, ARCNET, RS-232, RS-485 or a low-bandwidth special purpose wireless network. Modern systems rely on standards-based multi-protocol heterogeneous networking such as that specified in the IEEE 1905.1 standard and verified by the nVoy auditing mark. These accommodate typically only IP-based networking but can make use of any existing wiring, and also integrate powerline networking over AC circuits, power over Ethernet low-power DC circuits, high-bandwidth wireless networks such as LTE and IEEE 802.11n and IEEE 802.11ac and often integrate these using the building-specific wireless mesh open standard ZigBee).
Proprietary hardware dominates the controller market. Each company has controllers for specific applications. Some are designed with limited controls and no interoperability, such as simple packaged roof top units for HVAC. Software will typically not integrate well with packages from other vendors. Cooperation is at the Zigbee/BACnet/LonTalk level only.
Current systems provide interoperability at the application level, allowing users to mix-and-match devices from different manufacturers, and to provide integration with other compatible building control systems. These typically rely on SNMP, long used for this same purpose to integrate diverse computer networking devices into one coherent network.
Types of inputs and outputs
Sensors – Analog inputs are used to read a variable measurement. Examples are temperature, humidity and pressure sensors which could be thermistor, 4–20 mA, 0–10 volt or platinum resistance thermometer (resistance temperature detector), or wireless sensors.
A digital input indicates if a device is turned on or not – however it was detected. Some examples of an inherently digital input would be a 24 V DC/AC signal, current switch, an air flow switch, or a volta-free relay contact (dry contact). Digital inputs could also be pulse type inputs counting the frequency of pulses over a given period of time. An example is a turbine flow meter transmitting rotation data as a frequency of pulses to an input.
Nonintrusive load monitoring is software relying on digital sensors and algorithms to discover appliance or other loads from electrical or magnetic characteristics of the circuit. It is however detecting the event by an analog means. These are extremely cost-effective in operation and useful not only for identification but to detect start-up transients, line or equipment faults, etc.
Controls – Analog outputs control the speed or position of a device, such as a variable frequency drive, an I-P (current to pneumatics) transducer, or a valve or damper actuator. An example is a hot water valve opening up 25% to maintain a setpoint. Another example is a variable frequency drive ramping up a motor slowly to avoid a hard start.
Digital outputs are used to open and close relays and switches as well as drive a load upon command. An example would be to turn on the parking lot lights when a photocell indicates it is dark outside. Another example would be to open a valve by allowing 24VDC/AC to pass through the output powering the valve. Digital outputs could also be pulse type outputs emitting a frequency of pulses over a given period of time. An example is an energy meter calculating kWh and emitting a frequency of pulses accordingly.
Infrastructure
Controller – Controllers are essentially small, purpose-built computers with input and output capabilities. These controllers come in a range of sizes and capabilities to control devices commonly found in buildings, and to control sub-networks of controllers.
Inputs allow a controller to read temperature, humidity, pressure, current flow, air flow, and other essential factors. The outputs allow the controller to send command and control signals to slave devices, and to other parts of the system. Inputs and outputs can be either digital or analog. Digital outputs are also sometimes called discrete depending on manufacturer.
Controllers used for building automation can be grouped in three categories: programmable logic controllers (PLCs), system/network controllers, and terminal unit controllers. However an additional device can also exist in order to integrate third-party systems (e.g. a stand-alone AC system) into a central building automation system.
Terminal unit controllers usually are suited for control of lighting and/or simpler devices such as a package rooftop unit, heat pump, VAV box, fan coil, etc. The installer typically selects one of the available pre-programmed personalities best suited to the device to be controlled, and does not have to create new control logic.
Occupancy – Occupancy is one of two or more operating modes for a building automation system. Unoccupied, Morning Warmup, and Night-time Setback are other common modes.
Occupancy is usually based on time of day schedules. In Occupancy mode, the BAS aims to provides a comfortable climate and adequate lighting, often with zone-based control so that users on one side of a building have a different thermostat (or a different system, or sub system) than users on the opposite side.
A temperature sensor in the zone provides feedback to the controller, so it can deliver heating or cooling as needed.
If enabled, morning warmup (MWU) mode occurs prior to occupancy. During Morning Warmup the BAS tries to bring the building to setpoint just in time for Occupancy. The BAS often factors in outdoor conditions and historical experience to optimize MWU. This is also referred to as optimized start.
An override is a manually initiated command to the BAS. For example, many wall-mounted temperature sensors will have a push-button that forces the system into Occupancy mode for a set number of minutes. Where present, web interfaces allow users to remotely initiate an override on the BAS.
Some buildings rely on occupancy sensors to activate lighting or climate conditioning. Given the potential for long lead times before a space becomes sufficiently cool or warm, climate conditioning is not often initiated directly by an occupancy sensor.
Lighting – Lighting can be turned on, off, or dimmed with a building automation or lighting control system based on time of day, or on occupancy sensor, photosensors and timers. One typical example is to turn the lights in a space on for a half-hour since the last motion was sensed. A photocell placed outside a building can sense darkness, and the time of day, and modulate lights in outer offices and the parking lot.
Lighting is also a good candidate for demand response, with many control systems providing the ability to dim (or turn off) lights to take advantage of DR incentives and savings.
In newer buildings, the lighting control can be based on the field bus Digital Addressable Lighting Interface (DALI). Lamps with DALI ballasts are fully dimmable. DALI can also detect lamp and ballast failures on DALI luminaires and signals failures.
Air handlers – Most air handlers mix return and outside air so less temperature/humidity conditioning is needed. This can save money by using less chilled or heated water (not all AHUs use chilled or hot water circuits). Some external air is needed to keep the building’s air healthy. To optimize energy efficiency while maintaining healthy indoor air quality (IAQ), demand control (or controlled) ventilation (DCV) adjusts the amount of outside air based on measured levels of occupancy.
Analog or digital temperature sensors may be placed in the space or room, the return and supply air ducts, and sometimes the external air. Actuators are placed on the hot and chilled water valves, the outside air and return air dampers. The supply fan (and return if applicable) is started and stopped based on either time of day, temperatures, building pressures or a combination.
Central plant – A central plant is needed to supply the air-handling units with water. It may supply a chilled water system, hot water system and a condenser water system, as well as transformers and auxiliary power unit for emergency power. If well managed, these can often help each other. For example, some plants generate electric power at periods with peak demand, using a gas turbine, and then use the turbine’s hot exhaust to heat water or power an absorptive chiller.
Alarms and security – All modern building automation systems have alarm capabilities. It does little good to detect a potentially hazardous or costly situation if no one who can solve the problem is notified. Notification can be through a computer (email or text message), pager, cellular phone voice call, audible alarm, or all of these. For insurance and liability purposes all systems keep logs of who was notified, when and how.
Alarms may immediately notify someone or only notify when alarms build to some threshold of seriousness or urgency. At sites with several buildings, momentary power failures can cause hundreds or thousands of alarms from equipment that has shut down – these should be suppressed and recognized as symptoms of a larger failure. Some sites are programmed so that critical alarms are automatically re-sent at varying intervals. For example, a repeating critical alarm (of an uninterruptible power supply in ‘bypass’) might resound at 10 minutes, 30 minutes, and every 2 to 4 hours thereafter until the alarms are resolved.
Information security – With the growing spectrum of capabilities and their connection with the Internet, building automation systems were repeatedly reported to be vulnerable, allowing hackers and cybercriminals to attack their components. Buildings can be exploited by hackers to measure or change their environment: sensors allow surveillance (e.g. monitoring movements of employees or habits of inhabitants) while actuators allow to perform actions in buildings (e.g. opening doors or windows for intruders). Several vendors and committees started to improve the security features in their products and standards, including KNX, ZigBee and BACnet (see recent standards or standard drafts), however, research reports several open problems in building automation security.
Room Automation
Room automation is a subset of building automation and with a similar purpose; it is the consolidation of one or more systems under centralized control, though in this case in one room.
The most common example of room automation is corporate boardroom, presentation suites, and lecture halls, where the operation of the large number of devices that define the room function (such as videoconferencing equipment, video projectors, lighting control systems, public address systems etc.) would make manual operation of the room very complex. It is common for room automation systems to employ a touchscreen as the primary way of controlling each operation.