When immediate delivery is not expected (or is not possible due to stock outs), a promised delivery date must be established. The order promising task is to determine when the shipment can be made. Available-to-promise (ATP) procedures coordinate order promising with production schedules.
A fundamental distinction between ATP functions is based on the push-pull strategy. Push-based ATP is based on forecasts regarding future demand – based on anticipation of demand, ATP quantities and availability dates are computed. A prominent example is the traditional determination of ATP based on the Master Production Schedule. The push-based approach is fundamentally limited by dependence on forecasts, which may prove inaccurate. Gross ATP represents the total available supply, Net ATP represents the supply remaining to support new demands, after existing demands have been accounted for.
Pull-based models, on the other hand, dynamically allocate resources in response to actual customer orders. This means that pull-based ATP is able to balance forecast-driven resource replenishment with order-triggered resource utilization, but because resources are allocated with each coming order, the process will yield myopic results.
ATP functions can be executed in real time, driven by each individual order, or in batch mode – meaning that at a certain time interval, the system checks availability for orders piled up in that period of time. The process is triggered by the need to check resource availability before making a commitment to deliver an order. For example, ATP calculation using SAP software depends on the level of stock, planned receipts (production orders, purchase orders, planned orders and so on), and planned requirements (sales orders, deliveries, reservations, etc.)
The uncommitted portion of a company’s inventory and planned production maintained in the master schedule to support customer-order promising is termed Available-To-Promise (ATP). The ATP quantity is the uncommitted inventory balance in the first period and is normally calculated for each period in which a Master Production Schedule (MPS) receipt is scheduled. In the first period, ATP includes on-hand inventory less customer orders that are due and overdue.
Three methods of calculation are used
- discrete ATP,
- cumulative ATP with look-ahead, and,
- cumulative ATP without look-ahead.
Discrete Available-To-Promise
A calculation based on the available-to-promise figure in the master schedule. For the first period, the ATP is the sum of the beginning inventory plus the MPS quantity minus backlog for all periods until the item is master scheduled again. For all other periods, if a quantity has been scheduled for that time period then the ATP is this quantity minus all customer commitments for this and other periods until another quantity is scheduled in the MPS. For those periods where the quantity scheduled is zero, the ATP is zero (even if deliveries have been promised). The promised customer commitments are accumulated and shown in the period where the item was most recently scheduled. Discrete Available-To-Promise is also, at times, referred to as Incremental Available-To-Promise.
Discrete ATP treats each period independently.
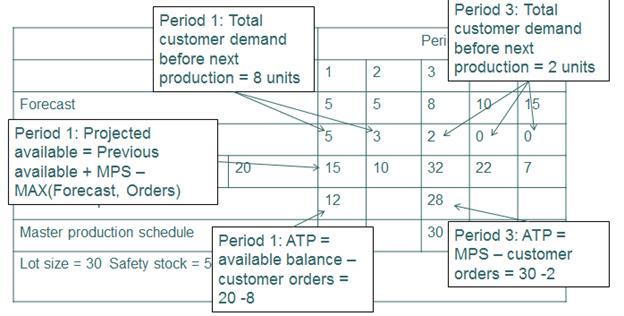
Cumulative Available-To-Promise
A calculation based on the available-to-promise (ATP) figure in the master schedule. Two methods of computing the cumulative available-to-promise are used, with and without look-ahead calculation. The cumulative with look-ahead ATP equals the ATP from the previous period plus the MPS of the period minus the backlog of the period minus the sum of the differences between the backlogs and MPSs of all future periods until, but not to include, the period where point production exceeds the backlogs. The cumulative without look-ahead procedure equals the ATP in the previous period plus the MPS, minus the backlog in the period being considered.
Cumulative ATP carries ATP units forward
