Automated storage and retrieval systems include a variety of methods for automatically placing and retrieving loads from specific storage locations, and include equipment such as:
- horizontal carousels
- vertical carousels
- vertical lift module
- traditional crane-in-aisle storage and retrieval systems
The systems are categorised into three main types – single masted, double masted and man aboard (which can be equipped with a picking platform). Items are delivered and removed from an automatic storage and retrieval system at stations which provide precise pickup and delivery points where the loads are transferred to/from conveyors or automatic guided vehicles (AGVs). It comprises a reception point where palletised goods are placed onto mechanical handling devices (eg lift trucks, conveyors, automatic guided vehicles), which are then taken to a transfer point where the palletised goods are transferred onto a storage and retrieval machine and placed onto storage racking. The retrieval of palletised goods from the storage racking is the reverse procedure.
Carry out a design risk assessment of the equipment, its installation and its systems during the design and construction phases. Also carry out hazard analysis and risk assessment before the equipment is used for the first time, to ensure that people are adequately safeguarded.
Hazards in an automated storage system
Hazards in an automated system include those between reception and transfer points. Hazards associated with the use of automatic guided vehicles (AGVs) include,
- collision between AGVs and people
- trapping points between AGVs and stationary objects or fixed structures
- dangerous occurrences by inadvertent movement of the AGV, eg where AGVs interact with storage and retrieval machines. The AGV could move off before the load transfer is complete, causing displacement or collapse of the load or other devices
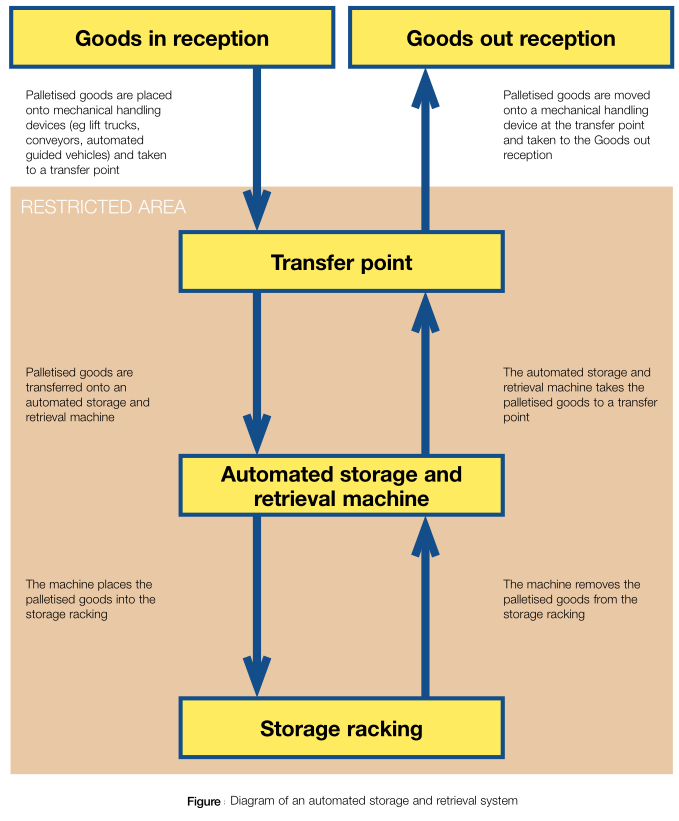
Hazards at transfer points include
- trapping points between mechanical handling devices, palletised loads and the structure of the transfer point
- collapse of the palletised load
- trapping points between an automated storage retrieval machine, palletised load, mechanical handling devices and the structure of the transfer point
Hazards in an automated storage area include,
- being struck by an automated storage and retrieval machine
- trapping points between automated storage and retrieval machines and fixed structures, eg racking
- trapping points between dangerous moving parts of the automated storage and retrieval machine
- trapping points at transfer points for goods, eg transfer arms, transfer pallets
- trapping points at transfer points for automated storage and retrieval machines which serve more than one aisle (movement of stacker onto transfer bogey, movement of the transfer bogey)
- collapse of an automated storage and retrieval machine or load, also part of load
- fall of a load (eg due to poor placement of the load)
- overrun of automated storage machine in horizontal or vertical travel
- inadvertent movement of an automated storage and retrieval machine (eg by maintenance technician unaware of position of co-worker); and
- fall from height (eg maintenance technician during recovery or routine servicing).
Always carry out a hazard analysis and risk assessment,
- when a new process is being introduced,
- when there has been a significant change in process
- in any case, review at appropriate intervals
Hazard analysis and risk assessment should be undertaken by a competent person or persons. It should also involve operators, users and maintenance.
Safeguarding automated and semi-automated systems
The type of hazard created and the level of risk will determine which safeguard(s) are appropriate.
Safeguarding at transfer points
In automated and semi-automated warehousing, the palletised load is transferred from the mechanical handling device to the automated storage and retrieval machine, usually via an opening in the perimeter fence surrounding the storage area. Risks may arise from contact with dangerous moving parts of the transfer mechanism, and access into the restricted area of the warehouse through large openings for feeding and delivery of pallets.
Dangerous moving parts of the transfer mechanism should be dealt with by, eliminating them by design, by providing close guarding (eg for chains and sprockets, vee belt drives) and by fixed or interlocked guards. The use of electro-sensitive safety systems, including pressure sensitive mats and photo-electric devices, may be necessary either to supplement fixed or interlocked guarding, or instead of such guarding if it is not practicable.
Access through the feed and delivery openings into the restricted area of the automated warehouse should be prevented by,
- restricting the size of the opening to the minimum possible, eg when trays of components are being fed into the system. This may present a simple and effective way of preventing access. Secondary traps between the load and sides of the fixed opening should, however, be avoided. It may be necessary to provide sensitive edges or trip flaps at the openings to prevent finger traps
- if it is not possible to reduce the opening to the extent that a person is not able to climb through, other means will be required, eg a photo-electric safety device which causes a shutdown of the transfer system and those parts of the automated warehouse that would be accessible following access through the opening. This photo-electric system would be muted after positive identification of the presence of incoming or outgoing goods for a timed period to allow goods in/out. Means of identification include a combination of transponders, identification tags, pallet profile identification, patterns and sequences of tripping of photo-electric sensors, load sensors etc
The objective should be to allow legitimate goods entry and exit, but to prevent inadvertent human access to an automated storage area when it is in operation.
Examples of safety systems
Electro-sensitive safety systems
These systems may be arranged to operate as trip devices, on the principle of detecting the approach of people, or as presence-sensing devices where dangerous parts cannot be set in motion when a person or object is detected.
Photo-electric (PE) safety systems
These systems detect an obstruction in the path by using a beam or beams of light (visible or invisible, eg infrared). PE safety systems may be used as:
- a trip device;
- a presence-sensing device; or
- a combination or zoning system where two or more PE devices are used as sensors and/or trip devices.
Pressure sensitive mats
These devices are placed on and secured to the horizontal surface over which a person may attempt to seek access. They have a sensitive upper surface so that the pressure applied by someone standing on them will cause dangerous motion to stop. When using electro-sensitive safety systems, PE safety systems, pressure sensitive mats or other suitable safeguards, the presence of a person or people in an identified and defined hazardous area should be detected and the appropriate action taken to remove or reduce the risk of injury, eg conveyor system stopped and approach to an active automated stacking machine prevented.
Safeguards for storage areas
Conventional perimeter fencing
Conventional perimeter fencing is made from rigid 2 m high fencing, securely fastened to the floor or to some convenient structure (eg racking) and positioned so that it is not possible to reach any dangerous parts of machinery or trapping points between automated stacking machines and fixed structures.
Access gates provided with interlocking device
An example is a trapped key exchange, which positively isolates the power supply or the control to all or parts of the storage system. The essential elements are a lock on the perimeter fencing gate and another lock on the control unit for the automated stacking machine. The key cannot be removed from the control unit to open the gate lock until a safe condition is established, eg isolation of the power supply to automated stacking machine.
Safe systems of work
Establish a safe system of work, eg for routine maintenance work, access for statutory examination of plant and where the automated stacking machine is rider-operated. It is important that the design of the storage area allows safe systems of work to be adopted . If it is necessary to restore power to the system with someone inside the restricted area (eg for fault finding, fault recovery or maintenance), it should be possible for this to be done in safety
- Restoring power to the system should be in the hands of the person within the restricted area (eg a key exchange system that allows them to restore power to a specific stacking machine).
- Operation of the stacking machine or other unit should be under the sole control of the person within the restricted area. There should be no other possibility of restoring automatic operation, and the stacking machine or other item of equipment should not respond to remote signals
- All other equipment should remain isolated. Alternatively, if there are multiple bays and several stacking machines, there should be means of safely isolating the stacking machine in the bay being worked on to prevent transfer bogies or other machines moving into that bay and to prevent maintenance staff moving into operating areas. This should include software control features, hardware features and physical barriers
- There should be a safe place or places of work for the person within the restricted area, eg areas around the subsidiary control panel (if any), working platform on the stacking machine etc
- Access/egress routes to rider-operated stacking machines should be designed so that entry into other parts of the restricted area, eg aisles, is not possible. A safe system of work should comprise a carefully considered analysis of the hazards, taking into account all the modes of operation, and needs for access/approach, leading to a method of working which will ensure the safety of those engaged in the particular activity. For each activity involving access to automated storage areas, adopt a formal written safe system of work. In some situations (eg repair work) it may be necessary to introduce a formal permit-to-work system which should set out a clear handover procedure; what work is to be done; who is to carry it out and the equipment necessary for the task; what safety precautions are to be taken; and a clear hand-back procedure.
Provide effective means to prevent overrun in the horizontal and vertical directions of travel, and to ensure the stacking machine is correctly positioned for loading, unloading and stacking etc. An adequate combination of limit switches and position-sensing devices should be provided and clearly identified in maintenance manuals etc. As a final safeguard, buffers should be provided on track-mounted systems at the limits of horizontal travel.
Clear warning notices
Clear, unambiguous warning notices should be prominently displayed at all access gates and strategic locations. Such notices may include,
- Restricted access. Authorised persons only
- Authorised persons must have read and understood the written safe systems of work
- Procedures specified in the safe system of work must be strictly adhered to