Air conditioners use refrigeration to chill indoor air, taking advantage of a remarkable physical law: When a liquid converts to a gas (in a process called phase conversion), it absorbs heat. Air conditioners exploit this feature of phase conversion by forcing special chemical compounds to evaporate and condense over and over again in a closed system of coils.
The compounds involved are refrigerants that have properties enabling them to change at relatively low temperatures. Air conditioners also contain fans that move warm interior air over these cold, refrigerant-filled coils. In fact, central air conditioners have a whole system of ducts designed to funnel air to and from these serpentine, air-chilling coils.
When hot air flows over the cold, low-pressure evaporator coils, the refrigerant inside absorbs heat as it changes from a liquid to a gaseous state. To keep cooling efficiently, the air conditioner has to convert the refrigerant gas back to a liquid again. To do that, a compressor puts the gas under high pressure, a process that creates unwanted heat. All the extra heat created by compressing the gas is then evacuated to the outdoors with the help of a second set of coils called condenser coils, and a second fan. As the gas cools, it changes back to a liquid, and the process starts all over again. Think of it as an endless, elegant cycle: liquid refrigerant, phase conversion to a gas/ heat absorption, compression and phase transition back to a liquid again.
It’s easy to see that there are two distinct things going on in an air conditioner. Refrigerant is chilling the indoor air, and the resulting gas is being continually compressed and cooled for conversion back to a liquid again. On the next page, we’ll look at how the different parts of an air conditioner work to make all that possible.
Classification
The air-conditioning components and equipments may be designed and assembled in hundred different ways but in practice these are broadly classified into three categories:
- Decentralized Systems (Individual Room Systems): This can be divided to three major types as
- Mini-Split Cooling Units (ductless split Units).
- Window Units.
- Mini- Heat Pump.
- Semi- centralized systems (packaged systems): This can be divided to two major types as follows:
- One piece systems (Unitary Packaged Systems):
- Packaged Air Conditioners with Water Cooled Condenser.
- Packaged Air Conditioners with Air Cooled Condensers.
- Two pieces systems (ducted Split system).
- Centralized systems (Central Hydronic systems): This can be divided to three major types as follows:
- Centralized Ducted “All – Air” Systems.
- Centralized Fluid Based Hydronic Systems.
- Combined (Hybrid) Water and Air Systems.
The following table will show a comparison between these
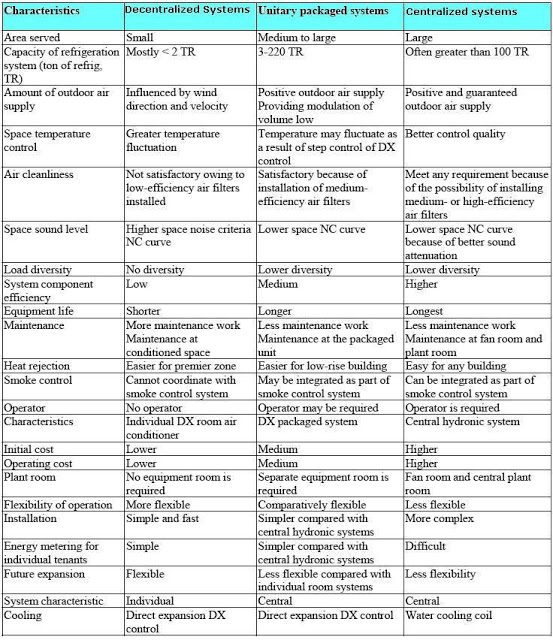
Decentralized Systems (Individual Room Systems)
These are systems in which heating and cooling is conducted locally, these systems are relatively common in schools, small hotels, domestic applications, residential homes and small offices. Decentralized Systems are essentially direct expansion (DX) systems, which operate using direct expansion of refrigerant in the finned tubes across the air path. In smaller buildings, smaller room air conditioners are less expensive to operate than central units, even though their efficiency is generally lower than that of central air conditioners.
In the outdoor unit there is a fan that blows air over the condenser thus cooling the compressed Freon gas in it. This gas passes through the expansion coil and gets converted into low pressure, low temperature partial gas and partial liquid Freon fluid, after passing from the expansion coil, the chilled Freon fluid enters the cooling coil. The blower sucks the hot, humid and filtered air from the room and it blows it over the cooling coil. As the air passes over cooling coil its temperature reduces drastically and also loses the excess moisture. The cool and dry air enters the room and maintains comfortable conditions of around 25-27 degree Celsius as per the requirements. The major types of decentralized systems are
Split Cooling Units – The split systems are individual systems in which the two heat exchangers are separated (one outside, one inside). The split air conditioner can be installed in rooms and offices where you don’t want to disturb the setup of the room and avoid demolitions in your favorite space. There are two main parts of the split air conditioner – outdoor and indoor unit.
Outdoor unit: This unit is installed outside the room or office space which is to be cooled and houses important components of the air conditioner like:
- The compressor: External power has to be supplied to the compressor, which is utilized for compressing the refrigerant and increases its pressure before sending it to the condenser. The size of the compressor varies depending on the desired air conditioning load. In most of the domestic split air conditioners hermetically sealed type of compressor is used. In such compressors the motor used for driving the shaft is located inside the sealed unit and it is not visible externally.
- Condenser coil: It is the coiled copper tubing with one or more rows depending on the size of the air conditioning unit and the compressor. The condenser is also covered with the aluminum fins so that the heat from the refrigerant can be removed at more faster rate.
- Condenser Cooling Fan: The condenser cooling fan is an ordinary fan with three or four blades and is driven by a motor. The cooling fan is located in front of the compressor and the condenser coil. As the blades of the fan rotate it absorbs the surrounding air from the open space and blows it over the compressor and the condenser with the aluminum fins thus cooling them.
- Expansion Valve: The expansion valve is usually copper capillary tubing with several rounds of coils. The high pressure and medium temperature refrigerant leaves the condenser and enters the expansion valve, where its temperature and pressure drops suddenly.
Indoor unit: The most common type of the indoor unit is the wall mounted type though other types like ceiling mounted and floor mounted are also used. the indoor unit produces the cooling effect inside the room or the office and houses
- The evaporator coil or the cooling coil: The cooling coil is a copper coil made of number turns of the copper tubing with one or more rows depending on the capacity of the air conditioning system. The cooling coil is covered with the aluminum fins so that the maximum amount of heat can be transferred from the coil to the air inside the room.
- Cooling Fan or Blower: The blower sucks the hot and unclean air from the room and supplies cool and clean air back. The shaft of the blower rotates inside the bushes and it is connected to a small multiple speed motor, thus the speed of the blower can be changed. When the fan speed is changed with the remote it is the speed of the blower that changes.
- The drain pipe: The drain pipe helps removing dew water collected inside the indoor unit.
- Louvers or Fins: The cool air supplied by the blower is passed into the room through louvers. The louvers help changing the angle or direction in which the air needs to be supplied into the room as per the requirements. There are two types of louvers: horizontal and vertical. The horizontal louvers are connected to a small motor and their position can set by the remote control and the vertical louvers are operated manually and one can easily change their position as per the requirements
- Air filter: It removes all the dirt particles from the room air and helps supplying clean air to the room. The air filter in the wall mounted type of the indoor unit is placed just before the cooling coil.
- Controls: The temperature inside the space can be maintained by thermostat setting.
These days, multi-split air conditioners are also being used commonly. In units for one outdoor unit there are two indoor units which can be placed in two different rooms or at two different locations inside a large room.
Window Units – Window-mounted air conditioners cool the individual conditioned spaces. A window unit is an encased assembly designed primarily for mounting in a window, through a wall, or as a console. A window unit produces cool air on one side and rejects hot air on the other and provides delivery of conditioned air to a room without ducts. A window unit has a low initial cost and is quick and easy to install. A window unit requires outside exposure for heat rejection and cannot be used for interior rooms
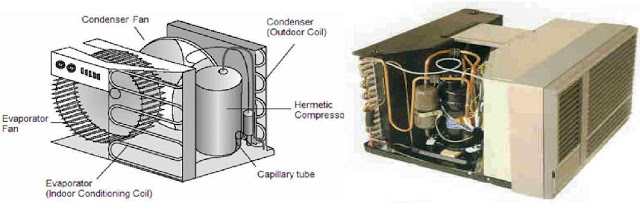
- Condenser (outdoor coil).
- Condenser fan.
- Hermetic compressor.
- Capillary tube.
- Evaporator (indoor conditioning coil).
- Evaporator fan.
- Controls: The controls for window units are simple and inbuilt, with a rotating switch marked with a hot-cold scale with no temperature settings. Most units will heat as well as cool. Fresh air control, if it exists, is normally adjusted by a manual lever.
Split Heat Pumps – A cooling only system cools the indoor air but a heat pump provides cooling in summer season and heating in winter season. DX system operating in reverse vapor compression cycle is classified as Heat pump. Through an addition of a special four-way reversing valve, heat flow in mechanical refrigeration loop can be reversed so that heat is extracted from outside air and rejected into the building.
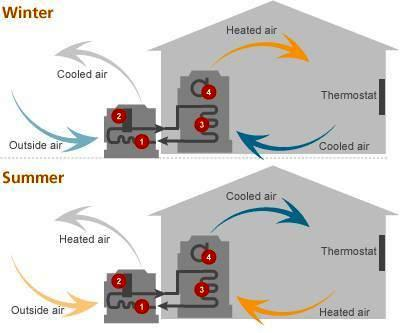
Such a facility is required during winter season to heat the indoor using the same physical components. Due to added heat of compression, the efficiency of heat pump is higher compared to the cooling cycle.
A supplementary electric resistance heater may also be used to assist the heat pump at lower outdoor temperatures. In colder climates, heats pumps require defrost period. During defrost times the electric heater is the only means of heating the interior of the building.
Split heat pumps are Air-to-Air types and they are the most common type of heat pumps. It is particularly suitable for factory-built unitary heat pumps, and has been widely used for residential and commercial application. Air is used as the heat source and heat sink. Extended surface, forced convection heat transfer coils are normally employed to transfer the heat between the air and the refrigerant. When selecting or designing an air-source heat pump, two factors in particular must be taken into consideration:
- The variation in temperature experienced in a given locality.
- The formation of frost.
Semi- centralized systems (packaged systems)
Packaged Systems are similar in nature to decentralized system but serve more rooms or even more than one floor. The packaged air conditioners are available in the fixed rated capacities of 3, 5, 7, 10 and 15 tons. These units are used commonly in places like restaurants, telephone exchanges, homes, small halls, etc. The major types of Semi- centralized systems (packaged systems) are:
- One piece systems (Unitary Packaged Systems):
- Packaged Air Conditioners with Water Cooled Condenser.
- Packaged Air Conditioners with Air Cooled Condensers.
- Two pieces systems (Split system).
One piece systems (Unitary Packaged Systems): In the Unitary packaged air conditioners all the important components of the air conditioners are enclosed in a single casing like window AC. Thus the compressor, cooling coil, air handling unit and the air filter are all housed in a single casing and assembled at the factory location. Since all equipment is prepackaged, the installation cost is usually lower, and the performance quality is often higher than field-erected systems.
Depending on the type of the cooling system used in these systems, the unitary packaged air conditioners are divided into two types:
Packaged Air Conditioners with Water Cooled Condenser: In these packaged air conditions the condenser is cooled by the water. The condenser is of shell and tube type, with refrigerant flowing along the tube side and the cooling water flowing along the shell side. The water has to be supplied continuously in these systems to maintain functioning of the air conditioning system.
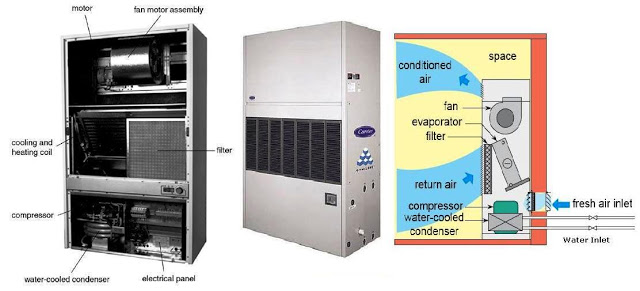
In the packaged units with the water cooled condenser, the compressor is located at the bottom along with the condenser (refer the figure below). Above these components the evaporator or the cooling coil is located. The air handling unit comprising of the centrifugal blower and the air filter is located above the cooling coil. The centrifugal blower has the capacity to handle large volume of air required for cooling a number of rooms. From the top of the package air conditioners the duct comes out that extends to the various rooms that are to be cooled.
Packaged Air Conditioners with Air Cooled Condensers – In this packaged air conditioners the condenser of the refrigeration system is cooled by the atmospheric air.
There is an outdoor unit that comprises of the important components like the compressor, condenser and in some cases the expansion valve. The outdoor unit can be kept on the terrace or any other open place where the free flow of the atmospheric air is available. The fan located inside this unit sucks the outside air and blows it over the condenser coil cooling it in the process. The condenser coil is made up of several turns of the copper tubing and it is finned externally. The packaged ACs with the air cooled condensers are used more commonly than the ones with water cooled condensers since air is freely available it is difficult maintain continuous flow of the water.
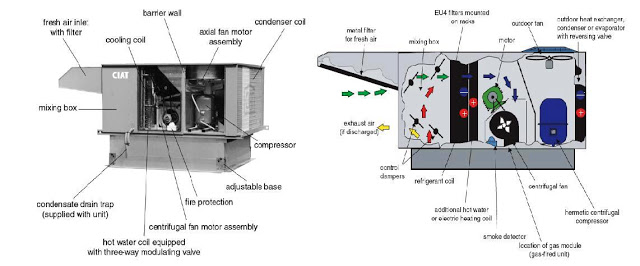
The cooling unit comprising of the expansion valve, evaporator, the air handling blower and the filter are located on the floor or hanged to the ceiling. The ducts coming from the cooling unit are connected to the various rooms that are to be cooled.
Two pieces systems (Ducted Split system) – In this system, the evaporator is separate from the condenser/compressor. These are commonly found in residential and small commercial installations with capacity ranges varying 1 to 50 TR and suitable for an area of 100 – 10000 square feet. The new ductless systems which can be conveniently mounted on the ceiling or wall are in this family.
A split system describes an air conditioning or heat pump system that is split into two sections – an outdoor section and an indoor section. The outdoor unit is comprised of a compressor and condenser and is located outside usually on the ground but sometimes on the roof. The indoor section, usually located in an interior closet or garage, consists of a fan, indoor cooling coil, furnace, and filter.
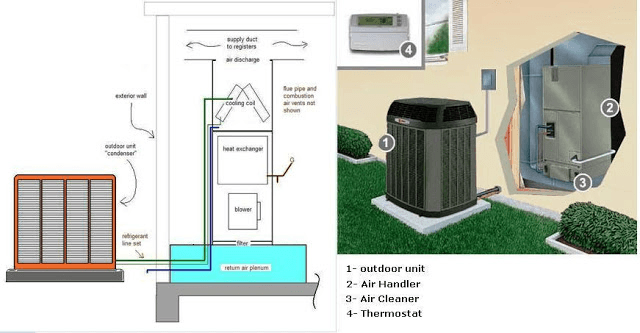
Centralized systems (Central Hydronic systems)
This can be divided to major types as
- Centralized Ducted “All – Air” Systems.
- Centralized Fluid Based Hydronic Systems.
- Combined (Hybrid) Water and Air Systems.
Centralized Ducted “All – Air” Systems : These are systems in which the primary movement of heat around the building is via heated and cooled air. These systems are the most common in large spaces such as office buildings, common public areas, retail, shopping, manufacturing areas, airports, hotel lobbies etc. In an ‘All-Air system’, the refrigerant or chilled water is used to cool and dehumidify the air in the air handling unit (AHU). The cool air is then circulated throughout the building thru the ductwork. Heating can also be accomplished either by hot water or electrical strip heaters.
The centralization of these systems allow for better management and system operation. On the other hand, they also require either a mechanical room adjacent to the controlled space for locating the AHU and large ductwork in building space.
Fresh air is drawn into the building through the intake louver, mixed with return air, heated or cooled to a controlled temperature, circulated around the building and provided to the occupied space. Local temperature control is provided by a terminal reheat unit attached to a temperature controller within the occupied space. Exhaust air is extracted from the space and dumped to the outside. In general, the majority of the return air is recycled via the return air duct.
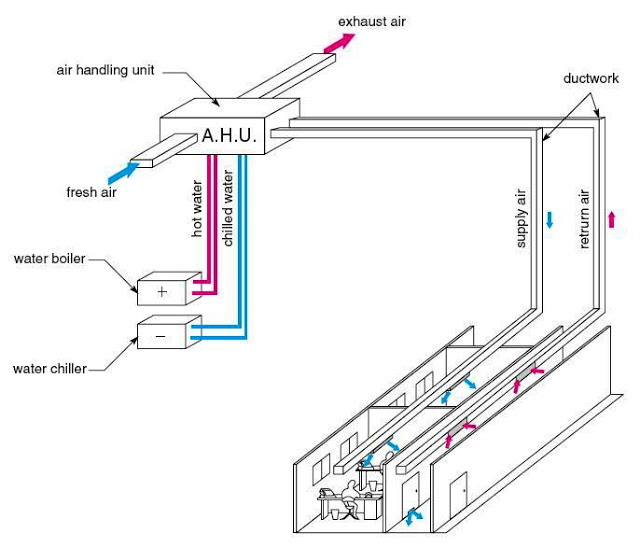
The individual components of this system are:
- Air Handling Unit: This is a cabinet that includes or houses the central furnace, air conditioner, or heat pump and the plenum and blower assembly that forces air through the ductwork.
- Intake louvers: These are the external louvers through which supply air is drawn into the building. Intake is generally equipped with volume control damper to regulate the amount of fresh air and economizing the quantity of outside air during favorable outside conditions.
- Filters: These are used to remove particles of dust or dirt from the supply air.
- Heating coils: These heat up the incoming airstream using coils through which hot water is passed or banks of electric heating elements.
- Cooling coils: These cool the incoming airstream using coils through which refrigerant or water is passed.
- Supply fans: These are used to circulate the air through the network of ductwork.
- Ductwork: It is a branching network of round or rectangular tubes generally constructed of sheet metal, fiberglass board, or a flexible plastic and wire composite material located within the walls, floors, and ceilings. The three most common types of duct material used in home construction are metal, fiberglass duct board, and flex-duct.
- Supply Ductwork: These carry air from the air handler to the rooms in a house. Typically each room has at least one supply duct and larger rooms may have several.
- Return Ductwork: These carry air from the conditioned space back to the air handler. Most houses have only one or two main return ducts located in a central area.
- Supply and Return Plenums: These are boxes made of duct board, metal, drywall or wood that distribute air to individual ducts or registers.
- Terminal reheat heating coils: These use hot water coils or electric heating elements to heat up the air being supplied to one part of the building according to the temperature in that space.
- Supply and extract grilles : These are the points at which the air is either supplied into or extracted from the space, and may be ceiling-mounted or wall-mounted. Also called diffusers or registers.
- Boots: These connect ductwork to registers.
- Extract fans :These are used to extract the air from the space and discharge it to outside.
- Return air duct: These are interconnections between inlet and outlet ductwork sections, which let a controlled amount of air recirculate around the air conditioning system when full fresh air is not required.
- Exhaust louvers: These are the external louvers through which extract air is discharged from the building
There are three major types of Centralized Ducted Air Systems:
Constant Volume Systems (CAV): Constant volume systems deliver a constant volume of air and responds to changing thermal loads by varying air temperature. The air volume is usually based on the design cooling load for the given zone. The ducting and air handling system are sized to match the heat gain from equipment, lights, exterior, and people. Typical applications include
- Space with uniform loads (small office buildings, manufacturing plants, retail etc.).
- Small spaces requiring precision control.
Constant Volume Systems (CAV) Configurations – Various configurations are
- Local AHU: Each space is supplied by its own specific unit.
- Single zone AHU: Air is supplied to several spaces by a single AHU.
- Multi zone AHU: each space has its own separate supply air duct and the conditions of the supply air are adjusted by mixing the cool and warm air.
Dual Duct Systems – Dual or double duct system is an air conditioning system in which cold and warm air is circulated throughout a building via two parallel ducts. Hot air flows within one duct, cold air within the other. The proportion of hot and cold air delivered to each room within the building may be controlled by thermostatically operated dampers on the ducts outlet. The system is well suited to provide temperature control for individual spaces or zones.
Variable Volume Systems – Variable air volume (VAV) systems use variable volume terminal units or boxes to vary the airflow in each zone or space in accordance to the thermostat signals within the space. Heating is turned on when the air flow reaches a predetermined minimum. If more cooling is required, more cold air is introduced into the space.
In the best implementation of these systems, the central air handling unit fan speed is controlled to maintain a constant duct pressure. An interlock is arranged between the supply and extract fans. Variable air volume systems are very common in larger office buildings.
Centralized Fluid Based Hydronic Systems – In an all-water hydronic system, the hot or cold-water is distributed to individual heat transfer devices (terminal units) located in each room of the building. When heating, the terminal units draw heat from the water and when cooling these reject heat to the water.
The biggest drawback of all-water hydronic system is the difficulty in providing adequate indoor air quality. These systems are fairly common in office rooms, hotel rooms, schools, building perimeter control etc.
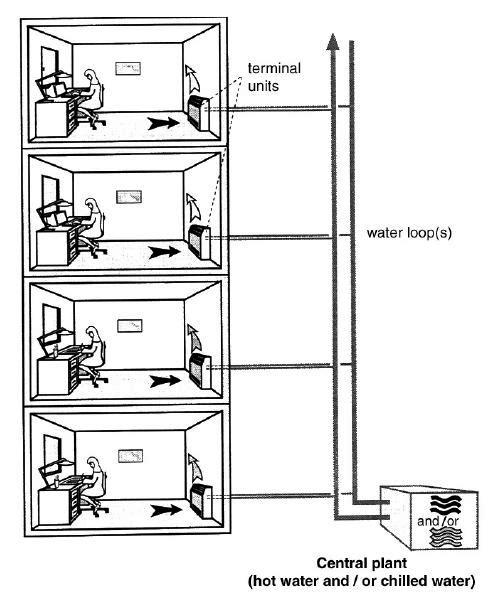
An All-Water system uses the following basic components:
- The use of a chiller (on roofs or plant rooms) to cool the water which would be circulated via circulating pumps to the terminal units (example fan coil units) located in the occupied space.
- The use of boilers (in plant rooms) to heat the water which would be circulated via circulating pumps to the terminal units located in the occupied space. Hydronic heating systems employ a variety of terminal units that include fan coil units, baseboard radiators, convectors, unit heaters, and radiant floors.
A fan coil unit is a terminal unit with:
- Heat exchange coil.
- A fan motor.
- A filter.
- A condensate drain pipe.
The hydronic system piping in All Water Systems can be arranged in 3 basic configurations:
- Two-pipe system – Two pipe systems consist of a network of insulated pipes; one pipe supplies chilled water and the second pipe returns it to the chiller. The secondary water is cold in summer and intermediate seasons and warm in winter. With water-changeover, chilled water is circulated during the cooling season and hot water during the heating season. The problems occur during the mid-seasons where cooling can be required part of the time and heating part of the time and no heating or cooling the rest of the time.
- Three-pipe system – In the three pipe system, hot water and chilled water are fed to each fan coil, with a common return. This is somewhat more expensive than 2-pipe system, since a third pipe must be run to each unit. Since the hot water and cold water are mixed in the return, these inefficient systems are seldom installed today.
- Four-pipe system – In the four pipe system, the chilled water loop and the hot water loop are completely separate. While these systems are most expensive to install, they are easier to operate in unpredictable climates.
Combined (Hybrid) Water and Air Systems – Hybrid systems use both air and water (cooled or heated in central plant room) distribution to room terminals to perform cooling or heating function. Unlike all-water system, this system ensures ventilation air in the spaces so that indoor air quality is not sacrificed.
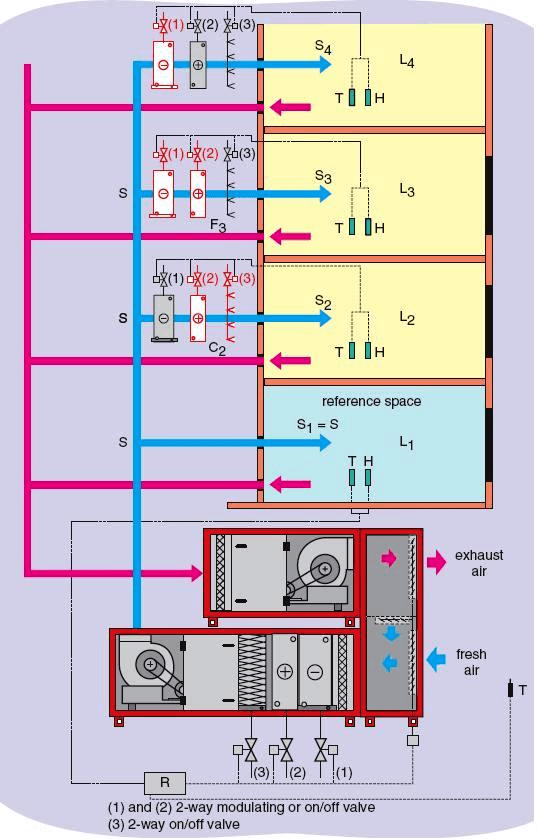
The air side is comprised of central air conditioning equipment, a duct distribution system, and a room terminal. The supply air, called primary air, usually has a constant volume which is determined by the need for outside (fresh) air for ventilation. When in cooling mode the primary air is dehumidified, to provide comfort and prevent condensation, by a central conditioning unit. In the winter, heating mode, the air is humidified, by the central conditioning unit, to limit dryness.
The water side consists of a pump and piping to convey water to heat transfer surfaces within each conditioned space. The water used can be chilled by direct refrigeration, by using chilled water from a primary cooling system, or by heat transfer through a water-to-water exchanger. Chillers usually supply chilled water anywhere from 35-48°F. Individual room temperature control is by regulation of either the water flow through it or the air flow over it. In the winter, the heating capacity of the coil in a conditioned space must be great enough to heat the space and offset the cool primary air, which is provided. Water Portion of the system which is determined by the need for outside (fresh) air for ventilation. When in cooling mode the primary air is dehumidified, to provide comfort and prevent condensation, by a central conditioning unit. In the w
Ducted whole house (central systems):
- Roof installation.
- Cool air is ducted into rooms through ceiling outlets.
- Existing heating ductwork is not suitable.
- Consider carefully in water restricted areas or when dependent on limited water supply.
Suitable for: whole home cooling.
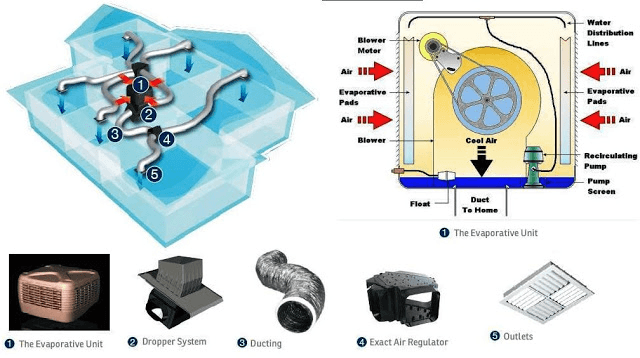
Cooling Towers
A cooling tower is a heat rejection device, installed outside of the building envelope, through which condenser water is circulated. Refrigerant in the refrigeration cycle is condensed in a refrigerant-to-water heat exchanger. Heat rejected from the refrigerant increases the temperature of the condenser water, which must be cooled to permit the cycle to continue. The condenser water is circulated to the cooling tower where evaporative cooling causes heat to be removed from the water and added to the outside air. The cooled condenser water is then piped back to the condenser of the chiller.
There are three basic types of towers as follows:
Forced Draft Tower – In forced draft cooling towers, air is “pushed” through the tower from an inlet to an exhaust. A forced draft mechanical draft tower is a blow-through arrangement, where a blower type fan at the intake forces air through the tower.
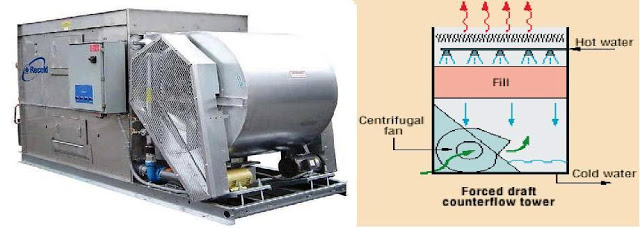
Induced Draft Tower – A second type of tower, induced draft has a fan in the wet air stream to draw air through the fill. The fan located is located at the discharge end, which pulls air through tower.
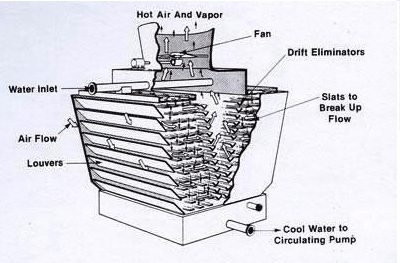
Natural Draft Tower – Natural draft tower has no mechanical means to create airflow. Natural-draft cooling towers use the buoyancy of the exhaust air rising in a tall chimney to provide the draft. Warm, moist air naturally rises due to the density differential to the dry, cooler outside air.
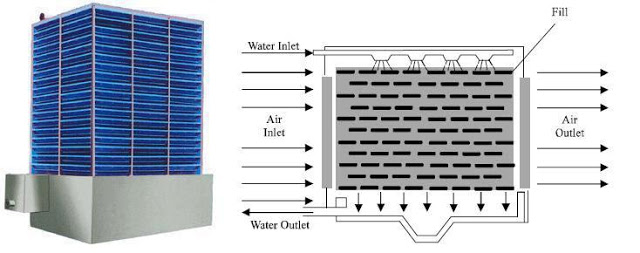
Maintenance
Outdoor units
- Inspect unit for proper refrigerant level and adjust if necessary
- Clean dirt, leaves and debris from inside cabinet
- Inspect base pan for restricted drain openings—remove obstructions as necessary
- Inspect coil and cabinet—clean as needed
- Inspect fan motor and fan blades for wear and damage—on older models lubricate as needed
- Inspect control box, associated controls/accessories, wiring and connections. Controls may include contactors, relays, circuit boards, capacitors, sump heat and other accessories. All control box and electrical parts should be checked for wear or damage.
- Inspect compressor and associated tubing for damage
Indoor units
- Inspect and clean blower assembly (includes blower housing, blower wheel and motor)
- On older models, lubricate motor and inspect and replace fan belt if needed
- Check combustion blower housing for lint and debris and clean as necessary
- Inspect evaporator coil, drain pan and condensate drain lines. Clean as needed
- Inspect for gas leaks in gas furnaces
- Inspect burner assembly—clean and adjust as needed
- Inspect ignition system and safety controls—clean and adjust as needed
- Inspect heat exchanger or heating elements
- Inspect flue system—check for proper attachment to the furnace, any dislocated sections, and for signs of corrosion. Replace if necessary.
- Inspect control box, associated controls, wiring and connections
- Clean or replace air filters
- Inspect conditioned airflow system (ductwork)—check for leaks
Whie system is operating
- Monitor system starting characteristics and capabilities
- Listen for abnormal noise
- Search for source of unusual odors
- Monitor air conditioning and heat pump systems for correct refrigerant charge
- Measure outdoor dry bulb temperature
- Measure indoor dry and wet bulb temperature
- Measure high and low side system pressures
- Monitor gas furnace for correct line and manifold gas pressure—make adjustments as needed
- Measure temperature rise and adjust airflow as needed
- Check vent system for proper operation
- Monitor system for correct line and load volts/amps
A typical maintenance check-up should include the following
- Check thermostat settings to ensure the cooling and heating system keeps you comfortable when you are home and saves energy while you are away.
- Tighten all electrical connections and measure voltage and current on motors. Faulty electrical connections can cause unsafe operation of your system and reduce the life of major components.
- Lubricate all moving parts. Parts that lack lubrication cause friction in motors and increases the amount of electricity you use.
- Check and inspect the condensate drain in your central air conditioner, furnace and/or heat pump (when in cooling mode). A plugged drain can cause water damage in the house and affect indoor humidity levels.
- Check controls of the system to ensure proper and safe operation. Check the starting cycle of the equipment to assure the system starts, operates, and shuts off properly.
- Clean evaporator and condenser air conditioning coils. Dirty coils reduce the system’s ability to cool your home and cause the system to run longer, increasing energy costs and reducing the life of the equipment.
- Check your central air conditioner’s refrigerant level and adjust if necessary. Too much or too little refrigerant will make your system less efficient increasing energy costs and reducing the life of the equipment.
- Clean and adjust blower components to provide proper system airflow for greater comfort levels. Airflow problems can reduce your system’s efficiency by up to 15 percent.