Hydrogen from Fossil Fuels
Hydrogen can be produced from most fossil fuels. The complexity of the processes varies, and in this chapter hydrogen production from natural gas and coal is briefly discussed. Since carbon dioxide is produced as a by-product, the CO2 should be captured to ensure a sustainable (zero-emission) process. The feasibility of the processes will vary with respect to a centralised or distributed production plant.
Production from natural gas – Hydrogen can currently be produced from natural gas by means of three different chemical processes
- Steam reforming (steam methane reforming – SMR).
- Partial oxidation (POX).
- Autothermal reforming (ATR).
Steam reforming involves the endothermic conversion of methane and water vapour into hydrogen and carbon monoxide (2.1). The heat is often supplied from the combustion of some of the methane feed-gas. The process typically occurs at temperatures of 700 to 850 °C and pressures of 3 to 25 bar. The product gas contains approximately 12 % CO, which can be further converted to CO2 and H2 through the water-gas shift reaction (2.2).
CH4 + H2O + heat à CO + 3H2 (2.1)
CO + H2O à CO2 + H2+ heat (2.2)
Partial oxidation of natural gas is the process whereby hydrogen is produced through the partial combustion of methane with oxygen gas to yield carbon monoxide and hydrogen (2.3). In this process, heat is produced in an exothermic reaction, and hence a more compact design is possible as there is no need for any external heating of the reactor. The CO produced is further converted to H2 as described in equation (2.2).
CH4+ 1/2 O2 à CO + 2H2 + heat (2.3)
Autothermal reforming is a combination of both steam reforming (2.1) and partial oxidation (2.3). The total reaction is exothermic, and so it releases heat. The outlet temperature from the reactor is in the range of 950 to 1100 °C, and the gas pressure can be as high as 100 bar. Again, the CO produced is converted to H2through the water-gas shift reaction (2.2). The need to purify the output gases adds significantly to plant costs and reduces the total efficiency.
Production from coal – Hydrogen can be produced from coal through a variety of gasification processes (e.g. fixed bed, fluidised bed or entrained flow). In practice, high-temperature entrained flow processes are favoured to maximise carbon conversion to gas, thus avoiding the formation of significant amounts of char, tars and phenols. A typical reaction for the process is given in equation (2.4), in which carbon is converted to carbon monoxide and hydrogen.
C(s) + H2O + heat à CO + H2 (2.4)
Since this reaction is endothermic, additional heat is required, as with methane reforming. The CO is further converted to CO2 and H2 through the water-gas shift reaction, described in equation (2.2). Hydrogen production from coal is commercially mature, but it is more complex than the production of hydrogen from natural gas. The cost of the resulting hydrogen is also higher. But since coal is plentiful in many parts of the world and will probably be used as an energy source regardless, it is worthwhile to explore the development of clean technologies for its use.
Hydrogen from Splitting Of Water
Hydrogen can be produced from the splitting of water through various processes.
Water Electrolysis – Water electrolysis is the process whereby water is split into hydrogen and oxygen through the application of electrical energy, as in equation (3.1). The total energy that is needed for water electrolysis is increasing slightly with temperature, while the required electrical energy decreases. A high-temperature electrolysis process might, therefore, be preferable when high-temperature heat is available as waste heat from other processes. This is especially important globally, as most of the electricity produced is based on fossil energy sources with relatively low efficiencies.
H2O + electricity à H2 + 1/2 O2 (3.1)
Alkaline Electrolysis – Alkaline electrolysers use an aqueous KOH solution (caustic) as an electrolyte that usually circulates through the electrolytic cells. Alkaline electrolysers are suited for stationary applications and are available at operating pressures up to 25 bar. Alkaline electrolysis is a mature technology, with a significant operating record in industrial applications, that allows remote operation.
Commercial electrolysers usually consist of a number of electrolytic cells arranged in a cell stack. The major R&D challenge for the future is to design and manufacture electrolyser equipment at lower costs with higher energy efficiency and larger turn-down ratios.
Polymer electrolyte membrane (PEM) electrolysis – PEM electrolysers require no liquid electrolyte, which simplifies the design significantly. The electrolyte is an acidic polymer membrane. PEM electrolysers can potentially be designed for operating pressures up to several hundred bar, and are suited for both stationary and mobile applications. The main drawback of this technology is the limited lifetime of the membranes. The major advantages of PEM over alkaline electrolysers are the higher turndown ratio, the increased safety due to the absence of KOH electrolytes, a more compact design due to higher densities, and higher operating pressures.
With relatively high cost, low capacity, poor efficiency and short lifetimes, the PEM electrolysers currently available are not as mature as alkaline electrolysers. It is expected that the performance of PEM electrolysers can be improved significantly by additional work in materials development and cell stack design.
High-temperature Electrolysis – High-temperature electrolysis is based on technology from high-temperature fuel cells. The electrical energy needed to split water at 1000 °C is considerably less than electrolysis at 100 °C. This means that a high-temperature electrolyser can operate at significantly higher overall process efficiencies than regular low-temperature electrolysers.
A typical technology is the solid oxide electrolyser cell (SOEC). This electrolyser is based on the solid oxide fuel cell (SOFC), which normally operates at 700 to 1000 °C. At these temperatures, the electrode reactions are more reversible, and the fuel cell reaction can more easily be reversed to an electrolysis reaction. Attempts are currently underway to develop systems in which some of the electricity consumed by the electrolyser can be replaced with the heat available from geothermal, solar or natural gas sources, thus reducing the consumption of electricity significantly.
Photo-electrolysis (photolysis) – Photovoltaic (PV) systems coupled to electrolysers are commercially available. The systems offer some flexibility, as the output can be electricity from photovoltaic cells or hydrogen from the electrolyser. Direct photo-electrolysis represents an advanced alternative to a PV-electrolysis system by combining both processes in a single apparatus. Photo-electrolysis of water is the process whereby light is used to split water directly into hydrogen and oxygen. Such systems offer great potential for cost reduction of electrolytic hydrogen, compared with conventional two-step technologies.
The key challenges to advance PEC cell innovation toward the market concern progress in materials science and engineering. It is very important to develop photo-electrode materials and their processing technologies with high-efficiency (performance) and corrosion-resistance (longevity) characteristics, paving the path toward smart system integration and engineering. Since no “ideal” photo-electrode material commercially exists for water splitting, tailored materials have to be engineered.
Photo-biological production (biophotolysis) – Photo-biological production of hydrogen is based on two steps: photosynthesis and hydrogen production catalysed by hydrogenases in, for example, green algae and cyanobacteria. Long-term basic and applied research is needed in this area, but if successful, a long-term solution for renewable hydrogen production will result. It is of vital importance to understand the natural processes and the genetic regulations of H2 production. Metabolic and genetic engineering may be used to demonstrate the process in larger bioreactors. Another option is to reproduce the two steps using artificial photosynthesis.
Biomass to Hydrogen
In biomass conversion processes, a hydrogen-containing gas is normally produced in a manner similar to the gasification of coal, as in equation (2.4). However, no commercial plants exist to produce hydrogen from biomass. Currently, the pathways followed are steam gasification (direct or indirect), entrained flow gasification, and more advanced concepts such as gasification in supercritical water, application of thermo-chemical cycles, or the conversion of intermediates ( e.g. ethanol, bio-oil or torrified wood). None of the concepts have reached a demonstration phase for hydrogen production.
Biomass feedstocks are unrefined products with inconsistent quality and poor quality control. The production methods vary according to crop type, location and climatic variations. Erratic fuels have contributed to the difficulties in technological innovation, since less homogenous and low-quality fuels need more sophisticated conversion systems. There is a need to rationalise the production and preparation of fuel to produce more consistent, higher-quality fuels that can be described by common standards. Large-scale systems tend to be suitable for cheaper and lower quality fuels, while smaller plants tend to require higher levels of fuel quality and better fuel homogeneity. A better understanding of this relationship, and the specific tolerances that each technology can accommodate, is needed.
Centralised Hydrogen Production
Large-scale, industrial hydrogen production from all fossil energy sources can be considered a commercial technology for industrial purposes, though not yet for utilities. Hydrogen production at a large scale has the potential for relatively low unit costs, although the hydrogen production cost from natural gas in medium sized plants may be reduced towards the cost of large-scale production. An important challenge is to decarbonise the hydrogen production process. CO2 capture and storage options are not fully technically and commercially proven. They require R&D on absorption or separation processes and process line-up, as well as acceptance for CO2 storage. It is also important to increase plant efficiency, reduce capital costs and enhance reliability and operating flexibility. A principle sketch of hydrogen distribution from a natural gas-based centralised hydrogen production plant is presented in figure below.
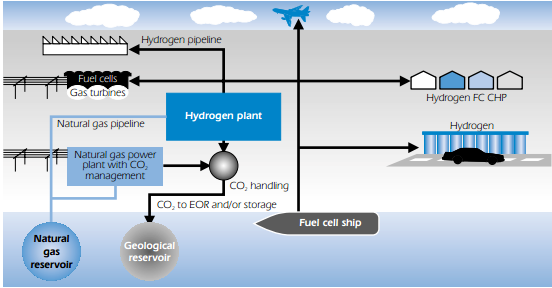
Further R&D is particularly needed on hydrogen purification (to produce H2 suitable for fuel cells) and on gas separation (to separate hydrogen or CO2 from gas mixtures). This involves the development of catalysts, adsorption materials and gas separation membranes for the production and purification of hydrogen. Hydrogen and power can be co-produced in integrated gasification combined cycle (IGCC) plants. The IGCC plant is the most advanced and efficient solution in which the carbon in the fuel is removed and the hydrogen is produced in a pre-combustion process.
Distributed Hydrogen Production
Distributed hydrogen production can be based on both water electrolysis and the natural gas processes discussed above. The benefit would be a reduced need for the transportation of hydrogen fuel, and hence less need for the construction of a new hydrogen infrastructure. Distributed production would also utilise existing infrastructure, such as natural gas or water and electric power. However, the production costs are higher for the smaller-capacity production facilities, and the efficiencies of production will probably be lower than those of centralised plants. In addition, carbon capture and sequestration would be more difficult and costly in small fossil-fuelled plants. Also, it is unlikely that CO2 from fossil fuels will be captured and stored when hydrogen is produced from distributed reformers.
Small-scale reformers will enable the use of existing natural gas pipelines for the production of hydrogen at the site of the consumer. Such reformers therefore represent an important technology for the transition to a larger hydrogen supply. The availability of commercial reformers is limited and most reformers are currently in an R&D stage. Further development and R&D is essential to meet customer requirements.