Geothermal power is considered to be a sustainable, renewable source of energy because the heat extraction is small compared with the Earth’s heat content. The greenhouse gas emissions of geothermal electric stations are on average 45 grams of carbon dioxide per kilowatt-hour of electricity, or less than 5 percent of that of conventional coal-fired plants.
Geothermal Exploration
Geological and hydrogeological studies are the starting point of any exploration programme, and their basic function is that of identifying the location and extension of the areas worth investigating in greater detail and of recommending the most suitable exploration methods for these areas. Geological and hydrogeological studies have an important role in all subsequent phases of geothermal research, right up to the siting of exploratory and producing boreholes. They also provide the background information for interpreting the data obtained with the other exploration methods and, finally, for constructing a realistic model of the geothermal system and assessing the potential of the resource. The information obtained from the geological and hydrogeological studies may also be used in the production phase, providing valuable information for the reservoir and production engineers. The duration and cost of exploration can be appreciably reduced by a good exploration programme and an efficient coordination of the research.
Geochemical surveys (including isotope geochemistry) are a useful means of determining whether the geothermal system is water- or vapour-dominated, of estimating the minimum temperature expected at depth, of estimating the homogeneity of the water supply, of inferring the chemical characteristics of the deep fluid, and of determining the source of recharge water. Valuable information can also be obtained on the type of problems that are likely to arise during the re-injection phase and plant utilization (e.g. changes in fluid composition, corrosion and scaling on pipes and plant installations, environmental impact) and how to avoid or combat them. The geochemical survey consists of sampling and chemical and/or isotope analyses of the water and gas from geothermal manifestations (hot springs, fumaroles, etc.) or wells in the study area. As the geochemical survey provides useful data for planning exploration and its cost is relatively low compared to other more sophisticated methods, such as the geophysical surveys, the geochemical techniques should be utilised as much as possible before proceeding with other more expensive methodologies.
Geothermal Electricity Generation
Electricity generation mainly takes place in conventional steam turbines and binary plants, depending on the characteristics of the geothermal resource.
Conventional steam turbines require fluids at temperatures of at least 150 °C and are available with either atmospheric (back-pressure) or condensing exhausts. Atmospheric exhaust turbines are simpler and cheaper. The steam, direct from dry steam wells or, after separation, from wet wells, is passed through a turbine and exhausted to the atmosphere (Figure 1).
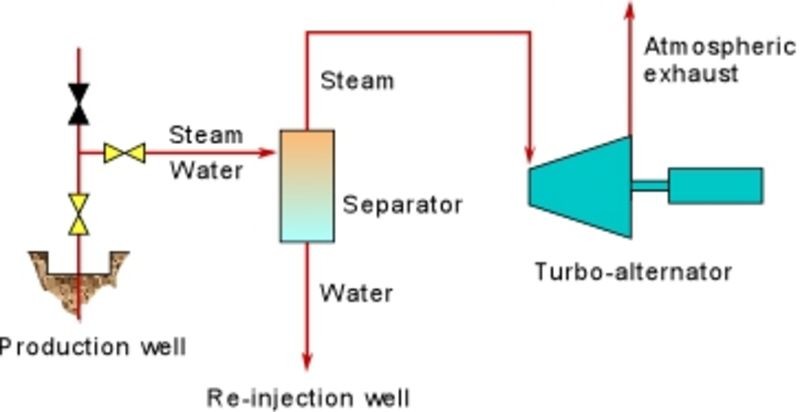
Figure 1: Sketch of an atmospheric exhaust geothermal power-plant. The flow of geothermal fluid is indicated in red.
With this type of unit, steam consumption (from the same inlet pressure) per kilowatt-hour produced is almost double that of a condensing unit. However, the atmospheric exhaust turbines are extremely useful as pilot plants, stand-by plants, in the case of small supplies from isolated wells, and for generating electricity from test wells during field development. They are also used when the steam has a high non-condensable gas content (>12% in weight). The atmospheric exhaust units can be constructed and installed very quickly and put into operation in little more than 13-14 months from their order date. This type of machine is usually available in small sizes (2.5 – 5 MWe).
The condensing units, having more auxiliary equipment, are more complex than the atmospheric exhaust units and the bigger sizes can take twice as long to construct and install. The specific steam consumption of the condensing units is, however, about half that of the atmospheric exhaust units. Condensing plants of 55 – 60 MWe capacity are very common, but recently plants of 110 MWe have also been constructed and installed (Figure 2).
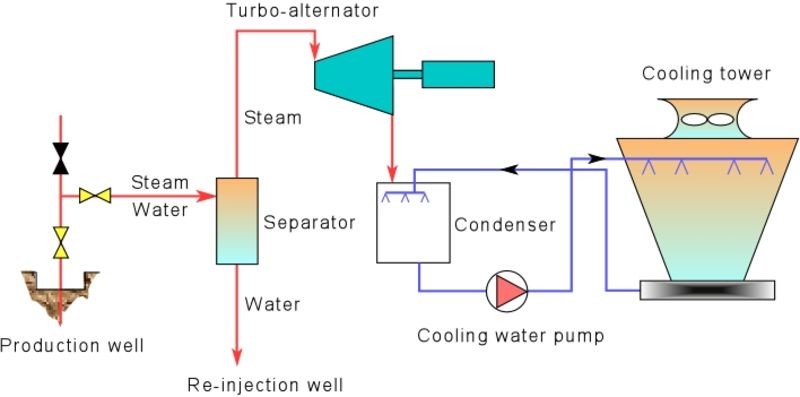
Figure 2: Sketch of a condensing geothermal power-plant. The flow of high-temperature fluid is indicated in red, and the cooling water in blue.
Generating electricity from low-to-medium temperature geothermal fluids and from the waste hot waters coming from the separators in water – dominated geothermal fields has made considerable progress since improvements were made in binary fluid technology. The binary plants utilize a secondary working fluid, usually an organic fluid (typically n-pentane), that has a low boiling point and high vapour pressure at low temperatures when compared to steam. The secondary fluid is operated through a conventional Rankine cycle (ORC): the geothermal fluid yields heat to the secondary fluid through heat exchangers, in which this fluid is heated and vaporises; the vapour produced drives a normal axial flow turbine, is then cooled and condensed, and the cycle begins again (Figure 3).
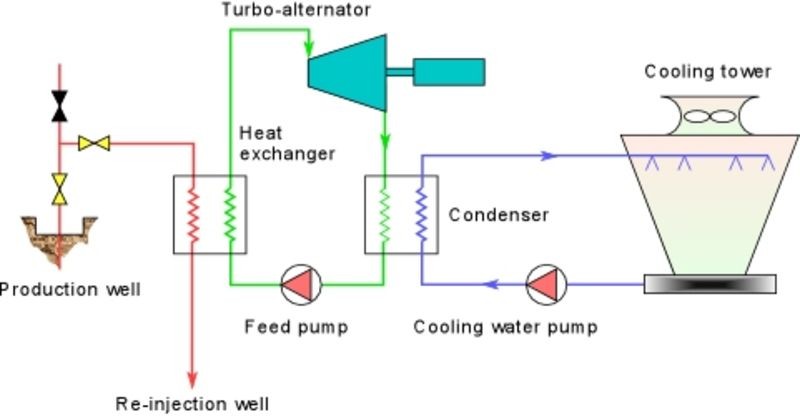
Figure 3: Sketch of a geothermal binary power plant. The flow of geothermal fluid is in red, the secondary fluid in green, and the cooling water in blue.
By selecting suitable secondary fluids, binary systems can be designed to utilise geothermal fluids in the temperature range 85-170 °C. The upper limit depends on the thermal stability of the organic binary fluid, and the lower limit on technical-economic factors: below this temperature the size of the heat exchangers required would render the project uneconomical. Apart from low-to-medium temperature geothermal fluids and waste fluids, binary systems can also be utilised where flashing of the geothermal fluids should preferably be avoided (for example, to prevent well sealing). In this case, down-hole pumps can be used to keep the fluids in a pressurised liquid state, and the energy can be extracted from the circulating fluid by means of binary units.
Binary plants are usually constructed in small modular units of a few hundred kWe to a few MWe capacity. These units can then be linked up to create power-plants of a few tens of megawatts. Their cost depends on a number of factors, but particularly on the temperature of the geothermal fluid produced, which influences the size of the turbine, heat exchangers and cooling system. The total size of the plant has little effect on the specific cost, as a series of standard modular units is joined together to obtain larger capacities.
Binary plant technology is a very cost-effective and reliable means of converting into electricity the energy available from water-dominated geothermal fields (below 170 °C).
A new binary system, the Kalina cycle, which utilizes a water-ammonia mixture as working fluid, was developed in the 1990s. The working fluid is expanded, in super-heated conditions, through the high-pressure turbine and then re-heated before entering the low-pressure turbine. After the second expansion the saturated vapour moves through a recuperative boiler before being condensed in a water-cooled condenser. The Kalina cycle is more efficient than existing geothermal ORC binary power plants, but is of more complex design.
Small mobile plants, conventional or not, can not only reduce the risk inherent to drilling new wells but, what is more important, they can help in meeting the energy requirements of isolated areas. The standard of living of many communities could be considerably improved were they able to draw on local sources of energy. Electricity could facilitate many apparently banal, but extremely important operations, such as pumping water for irrigation, freezing fruit and vegetables for longer conservation.
The convenience of the small mobile plants is most evident for areas without ready access to conventional fuels, and for communities that would be too expensive to connect to the national electric grid, despite the presence of high voltage transmission lines in the vicinity. The expense involved in serving these small by-passed communities is prohibitive, since the step-down transformers needed to tap electricity from high voltage lines cost more than US$ 675,000 each, installed, and the simplest form of local distribution of electricity, at 11 kV using wooden poles, costs a minimum of US$ 20,000 per kilometre (US$ 1994). By comparison, the capital cost (US$ 1998) of a binary unit is of the order of 1500-2500 US$/kW installed, excluding drilling costs. The demand for electric capacity per person at off-grid sites will range from 0.2 kW in less-developed areas to 1.0 kW or higher in developed areas. A 100 kWe plant could serve 100 to 500 people. A 1000 kWe plant would serve 1000 to 5000 people (Entingh et al., 1994).
Process of Power Generation
High Temperature Resources
High temperature geothermal reservoirs containing water and/or steam can provide steam to directly drive steam turbines and electrical generation plant. More recently developed binary power plant technologies enables more of the heat from the resource to be utilised for power generation. A combination of conventional flash and binary cycle technology is becoming increasingly popular.
High temperature resources commonly produce either steam, or a mixture of steam and water from the production wells. The steam and water is separated in a pressure vessel (Separator), with the steam piped to the power station where it drives one or more steam turbines to produce electric power. The separated geothermal water (brine) is either utilised in a binary cycle type plant to produce more power, or is disposed of back into the reservoir down deep (injection) wells. The following is a brief description of each of the technologies most commonly used to utilise high temperature resources for power generation.
Dry steam Power Plant

Dry steam power plants use very hot (>455 °F, or >235 °C) steam and little water from the geothermal reservoir. The steam goes directly through a pipe to a turbine to spin a generator that produces electricity. This type of geothermal power plant is the oldest, first being used at Lardarello, Italy, in 1904.
Flash Steam Power Plant
This is the most common type of geothermal power plant. The steam, once it has been separated from the water, is piped to the powerhouse where it is used to drive the steam turbine. The steam is condensed after leaving the turbine, creating a partial vacuum and thereby maximizing the power generated by the turbine-generator. The steam is usually condensed either in a direct contact condenser, or a heat exchanger type condenser. In a direct contact condenser the cooling water from the cooling tower is sprayed onto and mixes with the steam. The condensed steam then forms part of the cooling water circuit, and a substantial portion is subsequently evaporated and is dispersed into the atmosphere through the cooling tower. Excess cooling water called blow down is often disposed of in shallow injection wells. As an alternative to direct contact condensers shell and tube type condensers are sometimes used, as is shown in the schematic below. In this type of plant, the condensed steam does not come into contact with the cooling water, and is disposed of in injection wells.
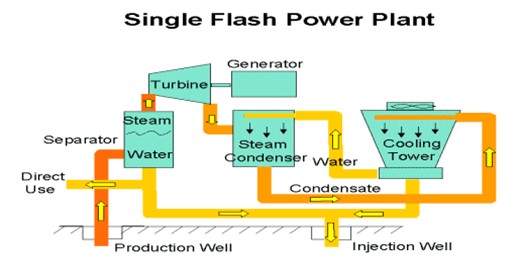
Typically, flash condensing geothermal power plants vary in size from 5 MW to over 100 MW. Depending on the steam characteristics, gas content, pressures, and power plant design, between 6000 kg and 9000 kg of steam each hour is required to produce each MW of electrical power. Small power plants (less than 10 MW) are often called well head units as they only require the steam of one well and are located adjacent to the well on the drilling pad in order to reduce pipeline costs. Often such well head units do not have a condenser, and are called backpressure units. They are very cheap and simple to install, but are inefficient (typically 10-20 tonne per hour of steam for every MW of electricity) and can have higher environmental impacts.
Binary Cycle Power Plants
In reservoirs where temperatures are typically less than 220o C. but greater than 100o C binary cycle plants are often utilised. The reservoir fluid (either steam or water or both) is passed through a heat exchanger which heats a secondary working fluid (organic) which has a boiling point lower than 100o C. This is typically an organic fluid such as Isopentane, which is vaporised and is used to drive the turbine. The organic fluid is then condensed in a similar manner to the steam in the flash power plant described above, except that a shell and tube type condenser rather than direct contact is used. The fluid in a binary plant is recycled back to the heat exchanger and forms a closed loop. The cooled reservoir fluid is again re-injected back into the reservoir.
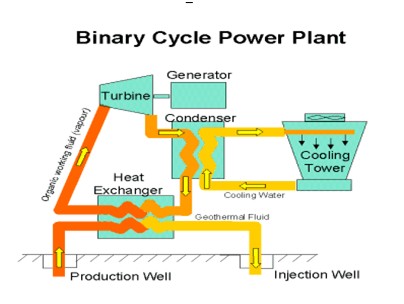
Binary cycle type plants are usually between 7 and 12 % efficient, depending on the temperature of the primary (geothermal) fluid. Binary Cycle plant typically vary in size from 500 kW to 10 MW.
Combined Cycle (Flash and Binary)
Combined Cycle power plants are a combination of conventional steam turbine technology and binary cycle technology. By combining both technologies, higher overall utilization efficiencies can be gained, as the conventional steam turbine is more efficient at generation of power from high temperature steam, and the binary cycle from the lower temperature separated water. In addition, by replacing the condenser-cooling tower cooling system in a conventional plant by a binary plant, the heat available from condensing the spent steam after it has left the steam turbine can be utilized to produce more power.