W. Edwards Deming in the 1950’s proposed that business processes should be analyzed and measured to identify sources of variations that cause products to deviate from customer requirements. He recommended that business processes be placed in a continuous feedback loop so that managers can identify and change the parts of the process that need improvements. As a teacher, Deming created a (rather oversimplified) diagram to illustrate this continuous process, commonly known as the PDCA cycle.
The plan–do–check–act cycle (Figure 1) is a four–step model for carrying out change. Just as a circle has no end, the PDCA cycle should be repeated again and again for continuous improvement.
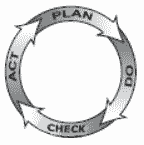
Figure 1: Plan-do-check-act cycle
When to Use Plan–Do–Check–Act
- As a model for continuous improvement.
- When starting a new improvement project.
- When developing a new or improved design of a process, product or service.
- When defining a repetitive work process.
- When planning data collection and analysis in order to verify and prioritize problems or root causes.
- When implementing any change.
Plan–Do–Check–Act Procedure
- Plan: Recognize an opportunity and plan a change.
- Do: Test the change. Carry out a small-scale study.
- Check: Review the test, analyze the results and identify what you’ve learned.
- Act: Take action based on what you learned in the study step: If the change did not work, go through the cycle again with a different plan. If you were successful, incorporate what you learned from the test into wider changes. Use what you learned to plan new improvements, beginning the cycle again.
A fundamental principle of the scientific method and PDCA is iteration—once a hypothesis is confirmed (or negated), executing the cycle again will extend the knowledge further. Repeating the PDCA cycle can bring us closer to the goal, usually a perfect operation and output.
Another fundamental function of PDCA is the “hygienic” separation of each phase, for if not properly separated measurements of effects due to various simultaneous actions (causes) risk becoming confounded.
PDCA (and other forms of scientific problem solving) is also known as a system for developing critical thinking. At Toyota this is also known as “Building people before building cars.” Toyota and other Lean companies propose that an engaged, problem-solving workforce using PDCA is better able to innovate and stay ahead of the competition through rigorous problem solving and the subsequent innovations. This also creates a culture of problem solvers using PDCA and creating a culture of critical thinkers.
In Six Sigma programs, the PDCA cycle is called “define, measure, analyze, improve, control” (DMAIC). The iterative nature of the cycle must be explicitly added to the DMAIC procedure.
Deming continually emphasized iterating towards an improved system, hence PDCA should be repeatedly implemented in spirals of increasing knowledge of the system that converge on the ultimate goal, each cycle closer than the previous. One can envision an open coil spring, with each loop being one cycle of the scientific method – PDCA, and each complete cycle indicating an increase in our knowledge of the system under study. This approach is based on the belief that our knowledge and skills are limited, but improving. Especially at the start of a project, key information may not be known; the PDCA—scientific method—provides feedback to justify our guesses (hypotheses) and increase our knowledge. Rather than enter “analysis paralysis” to get it perfect the first time, it is better to be approximately right than exactly wrong. With the improved knowledge, we may choose to refine or alter the goal (ideal state). Certainly, the PDCA approach can bring us closer to whatever goal we choose.
Rate of change, that is, rate of improvement, is a key competitive factor in today’s world. PDCA allows for major “jumps” in performance (“breakthroughs” often desired in a Western approach), as well as Kaizen (frequent small improvements). In the United States a PDCA approach is usually associated with a sizable project involving numerous people’s time, and thus managers want to see large “breakthrough” improvements to justify the effort expended. However, the scientific method and PDCA apply to all sorts of projects and improvement activities.