An Integrated Reliability program starts with the data collected by operators, mechanics, and lubrication technicians and continues through to data analysis and information dissemination by Reliability, Operations and Maintenance departments ending with decision making and prioritizing by Reliability, Operations, Maintenance, Sales / Marketing and Purchasing. At the primary level, the data collected from all asset care disciplines are brought together to make informed decisions that pertain specifically to asset life. At the secondary level, the disseminated information is spread throughout the corporation to the all departments that can utilize that information to make intelligent decisions to achieve corporate goals (profitability). The key element of this process is integrated data management – both within the reliability program (internal) and outward to the EAM/ERP/Control system used (external).
Integrated Data Management can take place in a variety of forms. The two main areas of integration can be grouped as internal and external. Internal integration brings multiple asset care disciplines together under a single system. Internal integration benefits the collection/analysis/distribution cycle specifically data, collection, data analysis and the distribution of the results. External integration concerns the exchanging of this data with existing ERP, EAM and plant operations systems. External integration greatly enhances the ability to use reliability information to manage maintenance and production scheduling. As a result integrated reliability processes make the decision-making process less costly and more accurate.
Integrated Data Management
Integrated Data Management is one of the keys to a successful implementation of a corporate reliability program. In small, single plant environments, non-integrated reliability tools can be used independently, with little or no formal integration. However, in large or multi-plant environments, the effort of accessing and managing data from non-integrated reliability tools can quickly overwhelm the benefits of those tools.
Integration has the largest positive affect on processes involving plant personnel from different fields because it shifts the focus to a shared process from an individual departmental focus. The following chart illustrates the reliability task and the plant personnel that might be involved. When working with an integrated system, the focus shifts to a team approach, as the individuals involved are able to view the information in the manner most meaningful to each.

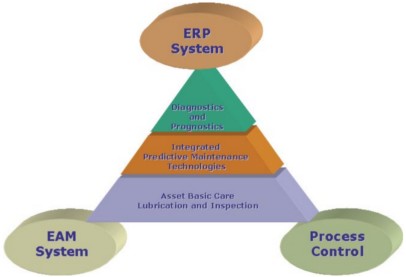
Systems Integration distributes the findings of the reliability program to decision makers within the plant. The following diagram illustrates an integrated reliability system where the internal (the reliability program ) is represented by the pyramid and the external (EAM/ERP/Control system).
Internal Integration
Internal integration brings multiple asset care disciplines together to present a cohesive view of the operating state of the asset. The advantages are:
- Data Collection – an integrated system provides a single mechanism for gathering route-based, sample-based and continuously collected data.
- Exception Handling – a single location is provided for viewing ALL alarms generated from the data collection process.
- Data Analysis – there is a single set of diagnostic methods that allows for consistent analysis of data from multiple disciplines.
External Integration
External integration involves exchanging reliability data with existing ERP, EAM and operations systems. External integration allows the sharing of key data through the plant in two areas.
- The existing operations data display is integrated with the reliability program to allow operations to access condition / inspection collected data on their plant information systems.
- The existing EAM/ERP system is integrated with the reliability program for workflow management information through a single mechanism managing condition and inspection-trigger work requests/ notifications in the EAM/ERP systems.