Standard costing system provides standard cost for budgeting purpose to plan future performance. Standards are pre-determined and it helps organization to achieve its objectives in economic and efficient manner. It can be used to motivate employee to achieve set standards of production/expenses level i.e. ideal standards. It provides some allowances for wastage and idle time (attainable standards), it recognizes the fact the labour are likely to waste some material and will become absent for various reasons like sickness.
A standard costing system initially records the cost of production at standard. Units of inventory flow through the inventory accounts (work-in-process finished goods cost of goods sold) at their per-unit standard cost. Standards are compared with actual outcomes to find deviations and reasons for these deviations, so that corrective action can be taken. It helps in managing human resources by giving them signal that their performances are being measured, compared and analyzed.
Rewards can be given and Disciplinary action can be taken based on pre-defined criteria communicated to them, so that decisions regarding whatever action taken can be justified to avoid resentment among workforce. The management evaluates the performance of a company by comparing it with some predetermined measures. Therefore, it can be used as a process of measuring and correcting actual performance to ensure that the plans are properly set and implemented
Installation of a Standard Costing System
The installation of a standard costing system involves the following steps:
- To Set the predetermined standards for sales margin and production costs
- To ascertain and collect the actual results
- To compare the actual performance with pre-determined standards
- To determine the variances
- To analyze and investigate the variances
- To ascertain the causes of variance
- To take corrective action where necessary
- To adjust the budget in order to make the standards more realistic
Functions of Standard Costing System
- Valuation: Assigning the standard cost to the actual output.
- Planning: Use the current standards to estimate future sales volume and future costs.
- Controlling: Evaluating performance by determining how efficiently the current operations are being carried out.
Features of a Standard Costing System
- The fact that standards are based on estimates.
- Standards will change according to conditions.
- It provides continual incentive for employee to keep costs and performance in line with predetermined standard.
- A standard cost system helps focus management’s attention on the following questions and their causes:
- Were materials purchased at prices above or below standard?
- Were materials used in quantities above or below standard?
- Is labour being paid at rates above or below standard?
- Is labour being used in amounts above or below standard?
Standard Costs for Material, Labour and Overhead
It should be noted that though standards must be set for materials, labour and overheads, only an integrated approach will bring the best results. There can be saving in labour, for example, if materials of certain quality or size are purchased or if more automatic machines are introduced. When standards are to be laid down, the exact process of production and the facilities that are to be used for the purpose should be decided and taken into account. Then only the standards can be fixed properly.
The first step in the development of a standard costing system is to set standard cost, i.e., to predetermine the standards in respect of each element of cost – direct material, direct labour and overheads. Extreme care is essential in the fixation of standards as the success of a standard costing system depends largely upon the accuracy of the standard costs used. While setting production cost standards, the following factors should be considered:
- Technical and operational aspects of the concern.
- Industrial engineering criteria for materials, labour, etc.
- The type of standard to be used.
- Proper classification of the accounts so that variance may be determined properly.
- Responsibility for setting standards. As definite responsibility for variances from standards is ultimately to be laid on individuals or departments, it is obvious that all those individuals or departments should be associated with setting of standards.
Direct Materials Standards
The standard cost of direct materials is closely related to the quantities and prices of materials to be used in production. Hence, two related standards are set:
- Materials Usage Standard: The object of setting the materials usage standard is to achieve maximum efficiency in materials usage. The first step in this connection lies in specifying the size and quality of materials. This is followed by an analysis of the materials requirements. A list is prepared showing the details of materials-size, grade, quantity etc. – for setting the standard. This is known as a ‘Standard Materials Specification.’ The standard quantities of materials to be used per unit of production can be laid down by one of the following means:
- By reference to the weight of materials in the final production.
- On the basis of past performance with due allowance for change in conditions.
- By means of test runs conducted under different conditions and taking an average of quantities used.
Due allowance must be made for normal wastage. This is generally based on an estimate wastage which is unavoidable, e.g., normal loss through evaporation, off-cuts, broken parts, etc.
- Materials Price Standard: Standards are set for material prices after due consideration of the efficiency of purchasing and store-keeping functions. The aim of setting materials price standard is to achieve maximum efficiency in this function, and thus minimize direct materials costs. The price standard should provide for discount on purchases, economy of bulk purchasing and anticipated changes in market price.
Standard Cost for Direct Labour
Direct labour costs depends upon labour time and wage rates and therefore, setting standard cost for direct labour involves setting two related standard:
- Standard Labour Time: This indicates the precise time (hours) that labour of a particular grade should take to perform a given operation. The main object of setting standard labour time is to derive maximum efficiency in the use of labour time. The standard time may be set on the basis of past performance with adjustments for change of conditions. Time and motion studies are a great help in setting standard time.
- Labour Rate Standard: This refers to the wage rates expected to be paid to different grades of labour employed in the organization. The object is to plan for the actual wages to be paid. A variety of factors should be considered and allowance made for them while setting standard wage rates, principal of them are-future trend of wages which can be anticipated; collective agreement between labour and management; guaranteed minimum wages; and overtime wages, if the level of activity makes overtime inevitable.
Both these standards must be set after a detailed study of labour work involved. Besides, the workers employed must be graded on a standard basis.
Standard Overhead Rates
The principal object of setting standard overhead rates is to minimize the overhead costs chargeable to production. Following steps are necessary for setting standard rates:
- The level of activity of production departments and the work to be done by the service departments should be determined.
- Overheads costs should be classified into fixed, variable and semi-variable overheads. The costs expected to be incurred under each head for each of the production and service departments should be calculated for a given period. The expected costs may be laid down in details in the form of cost-budgets based on past experience, present conditions and future trends.
- The standard overhead rates for each of the service departments should be calculated, and applied to the producing departments.
- The standard overhead rates for the producing departments may be determined as a direct labour hour rate, or a machine hour rate, or as a percentage of direct wages. The rates may be computed using the following ratios:
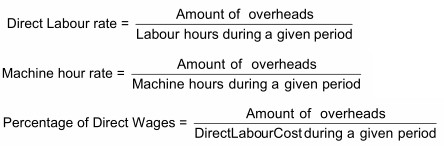
Standard Administration Costs
The object of setting standard administration cost is to secure the maximum quantity and quality of administrative services at minimum cost. For this purpose, all administrative functions should be studied in detail. O and M division by examining the office operations and suggesting simplification and standardization of methods and procedures may help a lot in this.
The standard quantity of work to be performed may be set by one or more of the following methods:
- On the basis of past performance:
- On the advice of organization and methods team;
- Time and motion studies; and
- Choosing appropriate ‘work units’ and fixing standard costs per work-unit.
Administrative costs should be classified into fixed, variable and semi-variable items before setting the standard rates.
Standard Cost For Selling and Distribution
Since selling and distribution expenses are primarily related to volume of sales, a sales forecast is essential before setting standards of selling and distribution costs. The classification of these costs into fixed, variable and semi-variable items is necessary. Another pre-requisite for setting standards is a detailed examination of the functions and determining standard units of operation.