The first step in implementing a one-piece flow cell is to decide which products or product families will go into the cells, and determine the type of cell: Product-focused or mixed model. For product focused cells to work correctly, demand needs to be high enough for an individual product. For mixed model cells to work, changeover times must be kept short; a general rule of thumb is that changeover time must be less than one takt time.
The next step is to calculate takt time for the set of products that will go into the cell. Takt time is a measure of customer demand expressed in units of time and is calculated as follows
Takt time = Available work-time per shift / Customer demand per shift
Next, determine the work elements and time required for making one piece. In much detail, list each step and its associated time. Time each step separately several times and use the lowest repeatable time. Then, determine if the equipment to be used within the cell can meet takt time. Considerations here include changeover times, load and unload times, and downtime.
The next step is to create a lean layout. Using the principles of 5-S (eliminating those items that are not needed and locating all items/equipment/materials that are needed at their points of use in the proper sequence), design a layout. Space between processes within a one-piece flow cell must be limited to eliminate motion waste and to prevent unwanted WIP accumulation. U-shaped cells are generally best; however, if this is impossible due to factory floor limitations, other shapes will do.
Finally, balance the cell and create standardized work for each operator within the cell. Determine how many operators are needed to meet takt time and then split the work between operators. Use the following equation
Number of operators = Total work content / Takt time
In most cases, an “inconvenient” remainder term will result (e.g., user will end up with Number of Operators = 4.4 or 2.3 or 3.6 instead of 2.0, 3.0, or 4.0). If there is a remainder term, it may be necessary to kaizen the process and reduce the work content. Other possibilities include moving operations to the supplying process to balance the line.
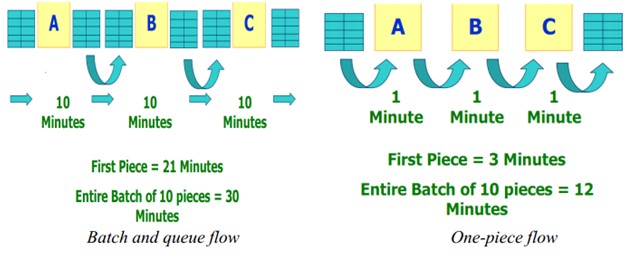