Design for Six Sigma can be seen as a subset of Six Sigma focusing on preventing problems by going upstream to recognize that decisions made during the design phase profoundly affect the quality and cost of all subsequent activities to build and deliver the product. Early investments of time and effort pay off in getting the product right the first time. DFSS adds a new, more predictive front end to Six Sigma. It describes the application of Six Sigma tools to product development and process design efforts with the goal of “designing in” Six Sigma performance capability. The intension of DFSS is to bring such new products and/or services to market with a process performance of around 4.5 sigma or better, for every customer requirement.
In the development of new processes, products, and services, Design for Six Sigma (DFSS) is the preferred method for ensuring Six Sigma-level quality and process performance right from the start.
When people refer to Six Sigma, they are usually talking about Six Sigma DMAIC. The DMAIC process targets sources of variation in existing processes, and then tries to reduce defects to near zero. DFSS is a closely linked strategy with many of the same characteristics. DFSS works on the same key principle: reducing defects, costs, and cycle time by reducing rework and the need for inspections. The difference is that DFSS focuses on future development and is proactive in nature.
DFSS is used to design, or redesign, a product or service from the ground up to ensure that the product or service and its associated processes are virtually error-free from the start.
DFSS lets you consider customer expectations and needs before the design is completed and implemented. It aims to create products, services and processes that are immune to problems, attractive to customers, and that inspire confidence in a company’s ability to deliver value and excellence. Unlike DMAIC, DFSS is not a single methodology but rather a flexible overall approach. It encompasses several methods, such as IDOV, DMADV, and DMADOV.
DFSS provides tremendous benefit but is complex to implement and has high start-up costs. Organizations must consider four other factors when deciding whether it’s appropriate to deploy DFSS: the Six Sigma levels of the organization’s current development, the amount of change in the business environment, the organization’s prioritized project schedule, and the organization’s capacity to roll out DFSS.
If, after many Six Sigma projects, the rate of improvement has slowed, or stops, and customers and improvement teams feel that the process and its outputs are still not at the desired quality level then it may be time to redesign the process or product from the ground up using DFSS. New products are vital contributors to company revenues. DFSS is the preferred method for ensuring Six Sigma-level quality and process performance when designing new products or redesigning old ones. To decide if the situation calls for employing DFSS methodologies, you must take into consideration the organization’s current success with DMAIC methods as well as its capacity, project scheduling, and business environment.
IDOV and DMADV methodologies
The two core methodologies employed in DFSS are IDOV and DMADV. Both have their foundations in the NPD methodology, and they encompass the same overall processes of identification, design, and verification.
Under the IDOV methodology, you first identify and incorporate customer requirements into a formal product design. Then, in the Design stage, you develop various concept designs, evaluate them, and select the best. The raw materials, process or service scope, procurement, and development plans are also developed. The Optimize step includes establishing the product specifications, service parameters, or process settings. It also entails using process capability information to predict performance and optimize designs where possible. The final step is to validate results by test runs, verifying the design and quality control systems.
The DMADV methodology is similar to IDOV except the process is divided into five steps, with the first three steps being roughly analogous to the Identify stage of IDOV. In DMADV, the process of identifying is parsed into Define, Measure, and Analyze stages. In the Define stage, the project goals and customer needs are taken into account. Then, in the second stage, you measure customer needs and specifications. In the third stage, you analyze the process options against customer needs. The final two stages of DMADV are where you design the product and verify the results.
DMADOV methodology
The DMADOV process is another methodology commonly used to build new products to high-quality levels. DMADOV has six stages or process steps: Define, Measure, Analyze, Design, Optimize, and Verify. All the stages of DMADOV are similar to DMADV, except that DMADOV integrates an Optimize stage before the final Verify stage. DMADOV also follows the IDOV methodology closely. The difference is the DMA in DMADOV takes the place of the “I” in IDOV and the “V” represents “verify” rather than “validate.”
There is no one standardized process for Design for Six Sigma. All of the various methods related to DFSS focus on customer needs and specifications and on early detection and correction of errors. Using cross-functional teams and stage gate processes has become the standard to ensure more efficient design development.
There are two, similar core methodologies you can adopt to roll out DFSS: IDOV and DMADV. Both are based on the New Product Development (NPD) process. A third option, DMADOV, is a variation on DMADV. It adds an Optimize stage, and is another good option for designing to a very high quality level.
Quality Function Deployment (QFD)
Quality Function Deployment is a method for prioritizing and translating customer inputs into designs and specifications for a product, service, and/or process. While the detail of the work involved in QFD can be both complex and exhaustive, the essentials of the QFD method are based on common-sense ideas and tools. QFD is a planning tool that relates a list of delights, wants, and needs of customers to design technical functional requirements.
With the application of QFD, possible relationships are explored between quality characteristics as expressed by customers and substitute quality requirements expressed in engineering terms. In the context of DFSS, these requirements critical-to characteristics, which include subsets such as critical-to-quality (CTQ) and critical-to-delivery (CTD). In the QFD methodology, customers define the product using their own expressions, which rarely carry any significant technical terminology. The voice of the customer can be discounted into a list of needs used later as input to a relationship diagram, which is called QFD’s house of quality.
One major advantage of a QFD is the attainment of shortest development cycle, which is gained by companies with the ability and desire to satisfy customer expectation. The other significant advantage is improvement gained in the design family of the company, resulting in increased customer satisfaction. QFD is a robust method having many variations in applications, as
- Prioritize and select improvement projects based on customer needs and current performance
- Assess a process’s or product’s performance versus competitors
- Translate customer requirements into performance measures
- Design, test, and refine new processes, products, and services
QFD uses various other methods like Voice of the Customer input to Design of Experiments, to work well. A special multidimensional matrix, also called as the “House of Quality,” is the best-known element of the QFD method. A full QFD product design project will involve a series of these matrices, translating from customer and competitive needs to detailed process specifications. QFD concept involves two core concepts, which are
The QFD Cycle
An iterative effort to develop operational designs and plans in four phases of
- Translate customer input and competitor analysis into product or service features.
- Translate product/service features into product/service specifications and measures.
- Translate product/service specifications and measures into process design features.
- Translate process design features into process performance specifications and measures.
QFD is accomplished by multidisciplinary DFSS teams using a series of charts to deploy critical customer attributes throughout the phases of design development. QFD is usually deployed over four phases. The four phases are phase 1—CTS planning, phase 2—functional requirements, phase 3—design parameters planning, and phase 4—process variables planning, as shown in the figure below.
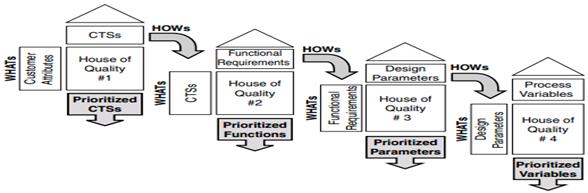
Prioritization and Correlation
Detailed analysis of the relationships among specific needs, features, requirements, and measures. Matrices like the House of Quality or the simple L-Matrix keep this analysis organized and document the rationale behind the design effort.
The QFD Cycle develops the links from downstream Ys (Customer Requirements and Product Specifications) back to upstream Xs (Process Specifications) in the design process itself. With an existing process or product, it can be used to clarify and document those relationships if they’ve never been investigated before. Another benefit of the House of Quality is a “diagonal” relationship test afforded by the matrix, testing combinations that may not have been considered by our standard human “linear” thought processes. An example is shown below
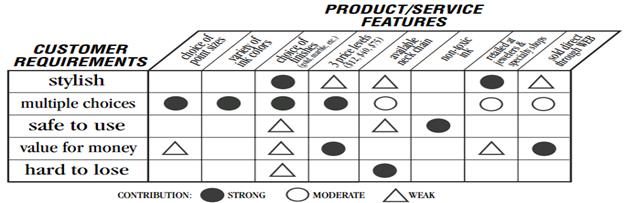
QFD analysis is conducted in six steps as
- It starts with the articulation of customer requirements. Techniques used could be interviewing, observation, prototyping, conceptual modeling, etc. The data from marketing research are also used. These requirements are also known as the “What’s”.
- In the second step, the company’s current product is ranked against the competitors.
- Next, the team looks at Product/Process Characteristics, in other words, the “How’s” of meeting the customer requirements. Candidate CCR’s are listed across the top and for each their relevance is considered and ranked as to which will address customer needs.
- Then, the team relates customer and technical requirements with ratings such as “high”, “moderate”, “low”, and “no” correlation. The team evaluates the degree to which customer wants and needs are addressed by the product or process characteristics.
- In the fifth step, the roof of the “House” focuses on relationships among product/process characteristics. It shows whether the “How’s” reinforce or conflict with one another.
- In last, the team summarizes the key conclusions. It ranks the relevance of product or process characteristics to the attainment of customers’ wants or needs.
Design And Process Failure Mode And Effects Analysis (DFMEA and PFMEA)
FMEA is a systematic, proactive method for evaluating a process to identify where and how it might fail and to assess the relative impact of different failures, in order to identify the parts of the process that are most in need of change. FMEA includes review of the following
- Steps in the process
- Failure modes (What could go wrong?)
- Failure causes (Why would the failure happen?)
- Failure effects (What would be the consequences of each failure?)
FMEA evaluates processes for possible failures and to prevent them by correcting the processes proactively rather than reacting to adverse events after failures have occurred. FMEA is also useful in evaluating new process prior to implementation and in assessing impact of changes to an existing process. FMEA usually involves the following steps
- Select a process to evaluate with FMEA – Evaluation using FMEA works best on processes that do not have too many sub-processes, instead of doing an FMEA on a large and complex process.
- Recruit a multidisciplinary team – Be sure to include everyone who is involved at any point in the process.
- Have the team meet together to list all of the steps in the process – Number every step of the process, and be as specific as possible. It may take several meetings for the team to complete this part of the FMEA, depending on the number of steps and the complexity of the process. Flowcharting can be a helpful tool for outlining the steps. When finished, be sure to obtain consensus from the group. The team should agree that the steps enumerated in the FMEA accurately describe the process.
- Have the team list failure modes and causes – For each step in the process, list all possible failure modes, anything that could go wrong, including minor and rare problems. Then, for each failure mode listed, identify all possible causes.
- For each failure mode, have the team assign a numeric value (known as the Risk Priority Number, or RPN) for likelihood of occurrence, likelihood of detection, and severity. Assigning RPNs helps the team prioritize areas to focus on and can also help in assessing opportunities for improvement. For every failure mode identified, the team should answer as a group with consensus on all values assigned to the following questions
- Likelihood of occurrence: How likely is it that this failure mode will occur? – Assign a score in 1 and 10, with 1 meaning “very unlikely to occur” and 10 meaning “very likely to occur.”
- Likelihood of detection: If this failure mode occurs, how likely is it that the failure will be detected? – Assign a score between 1 and 10, with 1 meaning “very likely to be detected” and 10 meaning “very unlikely to be detected.”
- Severity: If this failure mode occurs, how likely is it that harm will occur? – Assign a score between 1 and 10, with 1 meaning “very unlikely that harm will occur” and 10 meaning “very likely that severe harm will occur.” In patient care examples, a score of 10 for harm often denotes death.
- Evaluate the results – To calculate the Risk Priority Number (RPN) for each failure mode, multiply the three scores obtained (the 1to 10 score for each of likelihood of occurrence, detection, and severity). The lowest possible score will be 1 and the highest 1,000. Identify the failure modes with the top 10 highest RPNs. These are the ones the team should consider first as improvement opportunities. To calculate the RPN for the entire process, simply add up all of the individual RPNs for each failure mode.
- Use RPNs to plan improvement efforts – Failure modes with high RPNs are probably the most important parts of the process on which to focus improvement efforts. Failure modes with very low RPNs are not likely to affect the overall process very much, even if eliminated completely, and they should therefore be at the bottom of the list of priorities.
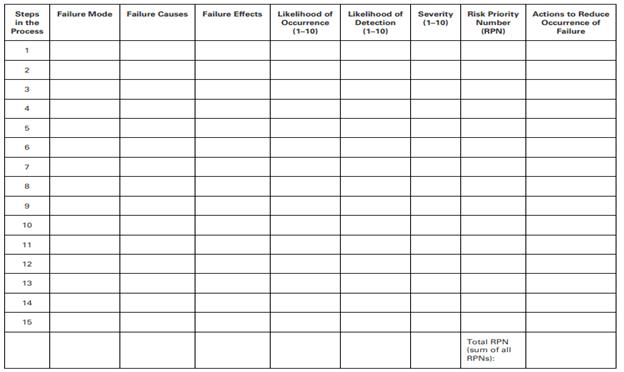
- Failure Mode: What could go wrong?
- Failure Causes: Why would the failure happen?
- Failure Effects: What would be the consequences of failure?
- Likelihood of Occurrence: 1–10, 10 = very likely to occur
- Likelihood of Detection: 1–10, 10 = very unlikely to detect
- Severity: 1–10, 10 = most severe effect
- Risk Priority Number (RPN): Likelihood of Occurrence × Likelihood of Detection × Severity
Design FMEA (DFMEA)
It is used to analyze designs before they are released to production. In the DFSS algorithm, a DFMEA should always be completed well in advance of a prototype build. The input to DFMEA is the array of functional requirements. The outputs are
- List of actions to prevent causes or to detect failure modes and
- History of actions taken and future activity.
The DFMEA helps the DFSS team in
- Estimating the effects on all customer segments
- Assessing and selecting design alternatives
- Developing an efficient validation phase within the DFSS algorithm
- Inputting the needed information for Design for X (DFMA, DFS,DFR, DFE, etc.)
- Prioritizing the list of corrective actions using strategies such as mitigation, transferring, ignoring, or preventing the failure modes
- Identifying the potential special design parameters (DPs) in terms of failure
- Documenting the findings for future reference
Process FMEA (PFMEA)
It is used to analyze manufacturing, assembly, or any other processes such as those identified as transactional DFSS projects. The focus is on process inputs. Software FMEA documents and addresses failure modes associated with software functions. The PFMEA is a valuable tool available to the concurrent DFSS team to help them in
- Identifying potential manufacturing/assembly or production process causes in order to place controls on either increasing detection, reducing occurrence, or both
- Prioritizing the list of corrective actions using strategies such as mitigation, transferring, ignoring, or preventing the failure modes
- Documenting the results of their processes
- Identifying the special potential process variables (PVs), from a failure standpoint, which need special controls
DFSS Roadmap
IDOV and DMADV helps in improving and extending DFSS. Both IDOV and DMADV are discussed.
IDOV
IDOV stands for Identify, Design, Optimize and Verify. It is a variant of DFSS (Design For Six Sigma) but, different from DMAIC (define, measure, analyze, improve and control). It consists of four different phases as
- Identify Phase – It identifies specific customer needs, based on which a product or business process will be designed. It is essential for launching a new product or service and involves various activities as, defining VOC, developing a team and team charter, performing competitive analysis and identifying CTQs. Other crucial steps in this phase involve the identification of customer and product requirements, establishment of an appropriate business model, identification of technical requirements such as CTQs, allocation of roles and responsibilities. Some of the tools used are QFD, FMEA, target costing and benchmarking.
- Design Phase – It focus on functional requirements, development of alternate business processes, evaluation of available options and selection of the most appropriate business process based on CTQs identified earlier. It includes the formulation of concept design, identification of probable risk elements, and identification of design parameters by utilizing advanced simulation tools and formulation of procurement plans and manufacturing plans. Tools used in this phase include risk assessment, FMEA, engineering analysis and Design of experiments.
- Optimize Phase – This phase uses CTQs for calculating the tolerance level of a selected business process by simulation tools. It predicts the performance capability of a business process, optimizing existing design and developing alternative design elements. This phase may involve assessment of process capabilities, optimization of design parameters, development of design for robust performance and reliability, error proofing and establishment of tolerance measurement objectives. Tools usually used are manufacturing database and flow back tools, design for manufacturability, process capability models, Monte Carlo methods, tolerance measurement tools and Six Sigma tools.
- Validate Phase – It being the last phase, focus on testing and validating the selected design. Any changes to the design can be made in this phase. This phase involves prototype test and validation, assessment of performance, failure modes, reliability and risks, design iteration and final phase review.
DMADV
DMADV refers to Define, Measure, Analyze, Design and Verify. DMADV is one aspect of Design for Six Sigma (DFSS), which has evolved from the earlier approaches of continuous quality improvement and Six Sigma approach to reduce variation. A key component of the DMADV approach is an active ‘toll gate’ check sheet review of the outcomes of each of the five steps of DMADOV. It is depicted as
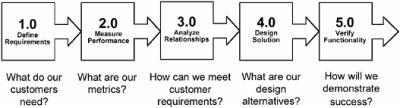
The application of DMADOV is aimed at creating a high-quality product keeping in mind customer requirements at every stage of the game. In general, the phases of DMADOV are
- Define phase – In this phase, wants and needs believed to be most important to customers are identified by historical information, customer feedback and other information sources. Teams are assembled to drive the process. Metrics and other tests are developed in alignment with customer information. The key deliverables are team charter, project plan, project team, critical customer requirements and design goals.
- Measure phase – The defined metrics are used to collect data and record specifications for remaining process. All the processes needed to successfully manufacture the product or service are assigned metrics for later evaluation. Technology teams test metrics and then apply them. The key deliverables are qualified measurement systems, data collection plan, capability analysis, refined metrics and functional requirements.
- Analyze phase – The result of the manufacturing process (i.e. finished product or service) is tested by internal teams to create a baseline for improvement. Leaders use data to identify areas of adjustment within the processes that will deliver improvement to either the quality or manufacturing process of a finished product or service. Teams set final processes in place and make adjustments as needed. The deliverables are data analysis, initial models developed, prioritized X’s, variability quantified, CTQ flow-down and documented design alternatives.
- Design phase – The results of internal tests are compared with customer wants and needs. Any additional adjustments needed are made. The improved manufacturing process is tested and test groups of customers provide feedback before the final product or service is widely released. The deliverables includes validated and refined models, feasible solutions, trade-offs quantified, tolerances set and predicted impact.
- Verify phase – The last stage in the methodology is ongoing. While the product or service is being released and customer reviews are coming in, the processes may be adjusted. Metrics are further developed to keep track of on-going customer feedback on the product or service. New data may lead to other changes that need to be addressed so the initial process may lead to new applications of DMADV in subsequent areas. The key deliverables are detailed design, validated predictions, pilot / prototype, FMEA’s, capability flow-up and standards and procedures.
The applications of these methodologies are generally rolled out over the course of many months, or even years. The end result is a product or service that is completely aligned with customer.