The goal of most warehouses is to increase throughput rates and reduce the amount of stock held. Cross docking is a process where products are moved directly from goods-in to the dispatch bays. This avoids the need to place the product into store and any subsequent picking operation. Cross docking needs the full support of suppliers as to how they present the product. This includes clear labeling and advance notice of arrival together with accurate, on-time delivery. Cross docking requires systems to identify the product that needs to be cross docked and a process needs to be in place to recognize and prompt the transfer.
Once checked in, the products should be taken directly to the dispatch area and their floor or temporary rack location recorded on the system, alerting staff that the product is now awaiting dispatch. The details must be recorded in order to provide an audit trail. Other points to take into account include the amount of space available at the inbound and outbound areas. Sufficient space is the key to moving products quickly and safely. Any congestion in these areas will slow up the process appreciably and lead to tension between teams. There also needs to be a well-marked staging area where the products can be placed prior to dispatch. An area of drive-in racking can assist in marshalling loads for particular collections.
Goods for cross-docking need to arrive by a strict time schedule linked to the vehicle departure times. The outgoing vehicles may be taking a mix of cross-docked goods (eg fresh goods) and stocked goods (eg long-shelf-life items), and thus a great degree of co-ordination is required to ensure that the operation can occur smoothly. If sortation is required, then a pick-by-line technique may be used to pick individual products from incoming pallets and place them on outgoing customer pallets. This may be undertaken manually or by using automated sortation equipment.
Cross docking is used significantly in the movement of perishable goods through the supply chain. Retailers use this system in their distribution centres where they receive products from multiple suppliers and sort and consolidate them for onward shipment to different stores. Just-in-time systems also rely on cross docking whereby manufacturers deliver parts to a cross-dock centre where they are consolidated and delivered line-side in sequence.
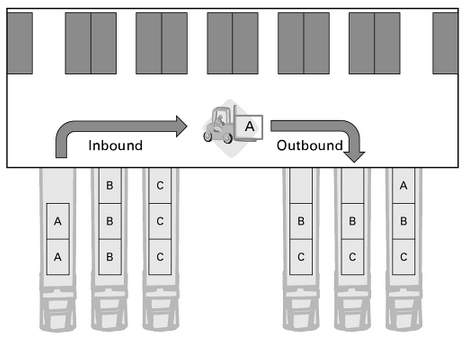
Figure: Example of Cross Docking
Cross-docking has a number of advantages in that it facilitates the rapid flow of goods through the supply chain and can be used as a technique to reduce inventory levels. It is particularly common for fresh and short-shelf-life goods, as well as for goods that are pre-allocated and need to be ‘pushed’ out to stores, as in the fashion industry.
Situations where cross-docking is not applicable are
- The introduction of cross-docking at a warehouse may just move inventory upstream in a supply chain, as suppliers may need to hold more inventory themselves to supply the warehouse on a just-in-time basis. A holistic view therefore needs to be taken to ensure that total inventory in the supply chain is reduced.
- Goods may be transported in less than pallet load quantities or less than vehicle load quantities, thus increasing transport costs.
- Considerable handling space may be required at the warehouse for the sortation activities.
- Close co-ordination is required with the suppliers (plus high levels of reliability), and this becomes increasingly complex with greater numbers of SKUs and suppliers.