Firms generally use a combination of public, private and contract facilities. A private or contract facility is used to accommodate basic annual requirements, while a public facility is used to take care of peak period. In other situations, central warehouses serve as private facilities, and field warehouses serve as public facilities.
Full warehouse utilisation annually is a remote probability. As per the planning rule, warehouses designed for full capacity utilisation will be utilized fully by 75-85% of the time. And 15-25% of the time, the space to meet peak requirements remains unutilized. In such cases, building private facilities is proven more efficient to cover 75% requirement, and using public facilities to meet peak demand.
Another form of combined public warehousing emanates from market needs. Basis distribution volume, an organization can identify private warehousing as perfect at particular locations. At other market situations, public facilities are most low cost option. In case of a logistical system design, the prime objective is to find which combination of warehousing strategy is most economical in meeting customer service objectives.
An all-inclusive warehouse strategy focuses on (1) number of warehouses to be employed, and (2) type of warehouses to be used to cater to market requirements. For most of the firms, it should be combination that can be differentiated by product and customer. In specificity, some customer groups can be better served from a private warehouse, whereas, a public warehouse can be used for other groups. Some of the qualitative factors that need to be considered include:
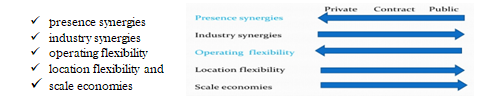
Presence synergies are the marketing advantages of having stock inventory situated close by in a facility, with a clear affiliation with the organization. Industry synergies are the operating advantages of co-locating with other organizations within the same industry. Operating flexibility is referred to as the ability to make adjustments in internal policies and procedures to accommodate product and customer requirements. Location flexibility is referred to as the ability to make quick adjustments on warehouse location and number as per permanent or seasonal demand changes. Scale economies are referred to as the ability to made reduction in material handling and storage by use of advanced technologies.
Alternate warehouse strategies
Warehouse alternatives include
- Private warehouses,
- Public warehouses, and
- Contract warehouses.
A private warehouse facility is owned and managed by the same enterprise that owns the merchandise handled and stored at the facility.
A public warehouse, in contrast, is operated as an independent business offering a range of services -such as storage, handling, and transportation- on the basis of a fixed or variable fee. Public warehouse operators generally offer relatively standardized services to all clients.
Contract warehousing, which is evolving from the public warehouse segment, provides benefits of both the private and public alternatives. Contract warehousing is a long term, mutually beneficial arrangement which provides unique and specially tailored warehousing and logistics services exclusively to one client, where the vendor and client share the risks associated with the operation.
Important dimensions that differentiate contract warehousing operators from public warehouse operators are the extended time frame of the service relationship, tailored services, exclusivity, and shared risk.
Private warehousing – A private warehouse is operated by the firm owning the product. The actual facility, however, may be owned or leased. The decision as to which strategy best fits an individual firm is essentially financial. Often it is not possible to find a warehouse for lease that fits the exact requirements of a firm. The major benefits of private warehousing include control, flexibility, cost, and other intangible benefits. Private warehouses provide more control since the enterprise has absolute decision-making authority over all activities and priorities in the facility. This control facilitates the ability to integrate warehouse operations with the rest of the firm’s internal logistics process.
Private warehousing is usually considered less costly than public warehousing because private facility costs do not have a profit markup. This perceived benefit, however, may be misleading since public warehouses often are more efficient or may operate at lower wage scales. Private warehousing has also some intangible benefits, particularly with respect to market presence.
A private warehouse with a firm’s name on it may produce customer perceptions of responsiveness and stability. This perception sometimes provides a firm with a marketing advantage over other enterprises.
Public warehouse – On the basis of the range of specialized operations performed, public warehouses are classified as
- General merchandise
- Refrigerated
- Special commodity
- Bonded
- Household goods and furniture
Each warehouse type differs in its material handling and storage technology as a result of the product and environmental characteristics.
General merchandise: These warehouses are designed to handle general package commodities such as paper, small appliances, and household supplies.
Refrigerated warehouses (either frozen or chilled): These warehouses handle and maintain food, medical items, and chemical products with special temperature requirements.
Commodity warehouses: These warehouses are designed to handle bulk material or items with special handling considerations, such as tires or clothing.
Bonded warehouses: These warehouses are licensed by the government to store goods prior to payment of taxes or duties.
They exert very tight control over all movements in and out of the facility since government documents must be filed with each move. For example, cigarettes are often stored in bonded warehouses prior to having the tax stamp applied.
This tactic saves the firm money by delaying tax payments; it also reduces inventory value substantially. Finally, a household goods or furniture warehouse is designed to handle and store large, bulky items such as appliances and furniture.
Of course, many public warehouses offer combinations of these operations. From a financial perspective, public warehousing may have a lower variable cost than comparable privately operated facilities. The lower variable cost may be the result of lower pay scales, better productivity, or economy of scale.
Public warehouses certainly result in lower capital costs. When management performance is judged according to return on investment (ROI), the use of public warehousing can substantially increase enterprise return.
Public warehousing offers flexibility in that it is easy to change the location, size, and number of facilities, allowing a firm to quickly respond to supplier, customer, and seasonal demands. Private warehouses are relatively fixed and difficult to change because buildings have to be constructed or sold.
Public warehousing can also offer significant scale economies since the volume for each customer is leveraged with that of other users. This results in high-volume operations that can spread fixed costs and justify more efficient handling equipment.
A public warehouse can also leverage transportation by providing delivery of loads that represent many public warehouse customers. For example, rather than have vendor A and vendor B, each deliver to a retail store from their own warehouse, a public warehouse serving both vendors could deliver a single combined load more efficiently. A public warehouse charges clients a basic fee for handling and storage.
In the case of handling, the charge is based on the number of cases or pounds handled. For storage, the charge is assessed on the number of cases or weight in storage during the month. Such charges normally exceed the cost of private warehousing if adequate private facility volume exists. However, when economies of scale are not possible in a private facility, public warehousing may be a low-cost alternative.
Contract warehouse – Contract warehousing combines the best characteristics of both private and public operations. The long-term relationship and shared risk result in lower cost than typical public warehouse arrangements.
Contract warehouse operations can provide benefits of expertise, flexibility, and economies of scale by sharing management, labor, equipment, and information resources across a number of clients. Although it is common for contract warehouse operators to share resources across clients in the same industry such as grocery products, it is not common that direct competitors will want to share resources. Contract warehouse operators are also expanding the scope of their services to include other logistics activities such as transportation, inventory control, order processing, customer service, and returns processing. For example, Rich Products, a frozen food manufacturer in Buffalo, New York, has increasingly utilized contract warehousing. The nature of the arrangement benefits both parties and allows Rich to expand its distribution network without incurring any fixed facility cost.