Containerisation is the packing of cargo into large dedicated boxes enabling multiple units of cargo to be handled simultaneously. This has increasingly facilitated the transportation of cargo since 1970s.
The development of intermodal transportation and containerization are mutually inclusive, self-strengthening and rely of a set of driving forces linked with technology, infrastructures and management. One of the initial issue concerned the different sizes and dimensions of containers used by shipping lines, which were a source of much confusion in compiling container shipping statistics. A lift could involve different volumes since different box sizes were involved. As a result, the term TEU (Twenty foot Equivalent Unit) was first used by Richard F. Gibney in 1969, who worked for the Shipbuilding & Shipping Record, as a comparative measure. Since then, the TEU remains the standard measure for containerized traffic.
The usage of containers shows the complementarity between freight transportation modes by offering a higher fluidity to movements and a standardization of loads. The container has substantially contributed to the adoption and diffusion of intermodal transportation which has led to profound mutations in the transport sector. Through reduction of handling time, labor costs, and packing costs, container transportation allows considerable improvement in the efficiency of transportation. Thus, the relevance of containers is not what they are – simple boxes – but what they enable; intermodalism. Globalization could not have taken its current form without containerization.
Benefits and Constraints of Containerisation
The benefits of containerisation can be summarized as follows.
- Factor Advantage: It is a standard transport product as per ISO and can be handled anywhere in the world (ISO standard). Use of specialized ships, trucks and wagons renders efficiency to the transportation activity.
- Flexibility of usage: It can be used for commodities (coal, wheat), manufactured goods, cars, frozen products. Containers are adapted for dry cargo, liquids (oil and chemical products) and refrigerated cargo. Containers are also reused.
- Management: Every container has a unique identification number and a size type code. In case of transportation it is measured in terms of units and not in terms of loads,
- Costs: Transportation cost is low – significantly less than bulk transport. The shipping company is able to offer lower rate as it benefits from economies of scale with high capacity container ships in operation.
- Speed: Transshipment operations are minimal and rapid. With specialised container handling systems at ports the turnaround times at ports are reduced from 3 weeks to about 24 hours. Containerships are faster than regular freighter ships.
- Warehousing: Stuffing can be done at own warehouse with simple in-expensive packaging.
- With double stacking on ships, trains and on the ground efficient stacking is possible.
- Security: The content of the container is unknown to carriers. The containers can be opened at the origin, at customs and at the destination only. The spoilage and losses (theft) are significantly reduced.
The primary constraints in containerization are
- Site constraints: With large consumption of terminal space (mostly for storage), the warehouses are usually moved to periphery of urban areas. The large containerships require very high draft (more than 13 meters).
- Infrastructure costs: Container handling infrastructures and equipment (giant cranes, warehousing facilities, inland road, rail access), require significant investments.
- Stacking: Complexity of arrangement of containers, both on the ground and on modes (containerships and double-stack trains). Restacking is difficult to avoid resulting in multiple handling.
- Empty movements: Many containers are moved empty (20% of all flows) which is a straight loss as either full or empty; a container takes the same amount of space. Since commercial flows are generally imbalanced, containers need to be repositioned empty.
- Illicit trade: It is a common instrument used in the illicit trade of drug and weapons, as well as for illegal immigration. This aspect is worrying in the context of terrorism.
Yet, the advantages of containerization have far outweighed its drawbacks, transforming the global freight transport system and along with it the global economy.
Containers are either made of steel (the most common for maritime containers) or aluminum (particularly for domestic) and their structure confers flexibility and hardiness. Another factor behind the diffusion of the container is that an agreement about its base dimensions and latching system was reached through the International Standards Organization (ISO) within 10 years of its introduction. From this standard, a wide variety of container sizes and specifications have been put in use. The most prevalent container size is however the 40 foot box, which in its 2,400 cubic feet which carry on average 22 tons of cargo. However, transporting cargo in a 20 foot container is usually 20% cheaper than transporting cargo in a 40 foot container. Irrespective of the size a 20 foot container requires the same amount of intermodal movements even if it takes about half the space during transport and at terminals. There are five main types of containers:
- Standard container. Container designed to carry a wide variety general cargo. They are often labeled as dry containers because they carry dry goods either in break bulk (most common) or bulk (less common) form. Cargo is loaded and unloaded through a double door which marks the “back side” of the container.
- Tank container. Container designed to carry liquids (chemicals or foodstuff). It is composed of a tank surrounded by a structure making it the same size than a standard 20 foot containers, including its four latching points.
- Open top container. A container with an open roof and designed to carry cargo that is too large to be loaded through standard container doors, such as machinery. The container is loaded from the top with a tarpaulin used to cover its contents.
- Flat container. Container having an open roof and sides designed to carry heavy and oversized cargo. The cargo transported is left exposed to outdoor conditions.
- Refrigerated container. Also known as a reefer. Container designed to carry temperature controlled cargo, often around or below freezing point. It is insulated and equipped with refrigeration plant maintaining the temperature constant.
In terms of the type of cargo for which the containers are mainly intended, they are classified as follows.
- General Cargo Container
- Specific Cargo Container
General Cargo Container
The general cargo containers are further classified as:
- Dry Cargo Containers
- Special Dry Cargo Containers
Dry Cargo Containers: The most commonly used shipping containers are general cargo boxes.
These are the steel containers that are visible in virtually every seaport around the world. They are fully enclosed with strong, rigid walls, a roof and floor and resistant to the elements as well as animals, birds and vermin.
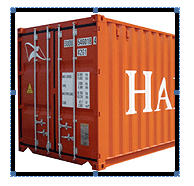
One of the walls is usually adapted to create an aperture for a door opening. End loaders have a door at one of the ends on the shortest side, while some containers are fitted with side wall doors for convenient “side loading”. 20 foot shipping containers and their 40 foot equivalents are the most common lengths while the standard width is 8 feet.
Special Dry Cargo Containers: Sometimes, loading (also known as packing) and unloading (also known as unpacking) cannot be easily accomplished through the end or side doors and therefore, special containers are used to do so.
- Open Top Containers: Open top shipping containers have similar characteristics to dry cargo containers but do not have a hard top steel roof. Instead, a canvas or reinforced cover is used to protect the cargo. The cover is supported on special “roof bows”.
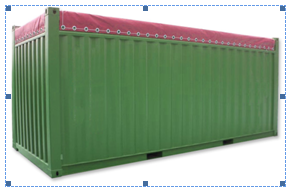
Such containers are used for heavy, bulky or fragile items such as sheet glass or machinery. Open top containers are sometimes in short supply and are not always available in some markets.
- ”Flat Rack” & Platform Containers Flat rack containers lack the superstructure of enclosed, dry cargo boxes. They do not have, therefore, fixed walls or any load-carrying structures. They do have special corner fittings at the top and bottom of the container to ensure safe stacking and handling at the container ports. These containers might be used in the transport and distribution of wood or other heavy and difficult to manage objects. They are not always available in some countries as supply is scarce.
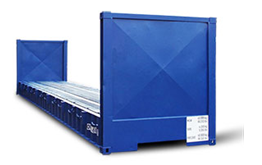
- Closed Ventilated Containers: Where goods need to be protected against excess moisture or humidity, special ventilation-adapted containers are used.
Specific Cargo Container
For the transportation of food, frozen, perishable or cold goods, shipping containers are adapted to specific purpose containers. Worldwide demand for these products has created a market and a requirement for different types of specific purpose container which are summarised as follows.
- Thermal Containers or “Reefers” Thermal containers are known in the industry as reefers. They are characterized by interior insulation on the doors, roof, floor and walls. Used for prolonging the shelf-life of food items and perishables, thermal reefers help to restrict the temperature range inside the containers.
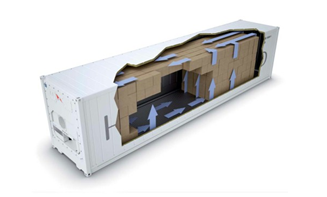
Reefers are commonly found in 20 foot and 40 foot shipping container sizes and are further classified as
- Insulated Shipping Containers: Insulated shipping containers do not utilize any devices for temperature regulation. Only the internal insulation helps maintain an ambient temperature.
- Refrigerated Shipping Containers: Refrigerated shipping containers have no external power or energy supply, so cold temperatures are maintained using dry ice or liquefied gas.
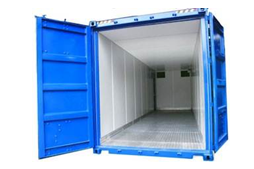
- Mechanically Refrigerated Containers: In these cases, a power supply is required to a refrigeration appliance. This is providing on land at sea ports, on road distribution trucks, or even on some container ships.
- Heated Containers: Similarly, a power supply is needed to run a heat-producing device.
- Named Cargo Containers: These containers transport items such as cars, other vehicles, livestock and poultry.
- Dry Bulk Containers: Dry bulk containers are used where no external packaging is required. Grains and dry foodstuffs fall into this category.
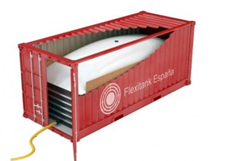
- Tank Containers: Tank containers incorporate a tank for the transport and distribution of chemicals, gases and hazardous liquids.
Unit Load Device (ULD)
The unit load device (ULD) is the air equivalent of the ISO container. Due to its unique shape resembling an igloo, the ULD is sometimes called the igloo (or iglu). The air mode containers mainly are of the IATA (International Air Transport Association) types. The popular sizes of ULD include the IATA Type.