Software Name | Website |
ACS Optima | www.cgsinc.com/softwaresoultions/index.html |
Bann | www.bann.com |
BPCS | www.ssagt.com |
Datatex | www.datatex-tim.com |
Intenia MovexFashion | www.intenia.com/w2000.nsf/index |
JD Edwards | www.jdedwards.com |
Pointman | www.pivotpoint.co.uk |
SAP | www.sap.com |
StyleFashion | NA |
Abas | NA |
Datatex Software
Datatex has been designing, developing, and implementing solutions exclusively for the textile and apparel industry since 1987. Dedication is the key to the Datatex development strategy. Specialization is the foundation of service to its customers. Datatex technological know-how and application skills have resulted in the worldwide success of TIM Textile Integrated Manufacturing – an ERP (Enterprise Resource Planning) solution designed for textile manufacturers of all sizes, whether vertically integrated, or specializing in just one stage of the manufacturing chain.
Datatex is an international company with offices in Italy, Israel, the USA, Germany, and Switzerland. The Datatex structure has been designed to cater to:
- The customer’s needs
- The customers practices and procedures
- The customer’s competencies.
Datatex:
- Has the expertise required presenting a detailed and realistic offering to the textile and appareling industry.
- Has the product and skills to implement the required functions of our solution while respecting the cost and time budgets (On time and within budget).
- Guarantee its customers that TIM will be supported for years to come.
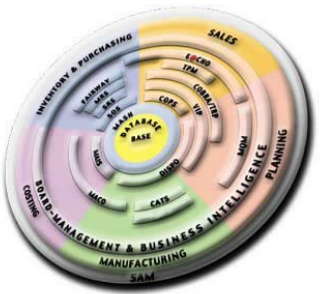
Figure 1.2 TIM – Textile Integrated Manufacturing
TIM is an integrated solution; therefore the enterprise information is available to everyone, not just to the few. Data is entered once and to be used across all company functions. A TIM implementation can cover all the manufacturing and logistical requirements, or only some of them. The TIM functions will be highlighted with reference to the following application areas: Sales, Planning, Inventory and Purchasing, Manufacturing, Costing and company Database.
MTO / Make-To-Order Highlights
- Capacity and/or materials feasibility checking
- Multi-level product views
- Suggested dates or availability if original request is not feasible
- The ability to consider forecasted orders from the master Gantt chart without having to create firm production orders
- Manual overrides of blocking as required
- Scheduling and allocating of scarce (critical) resources.
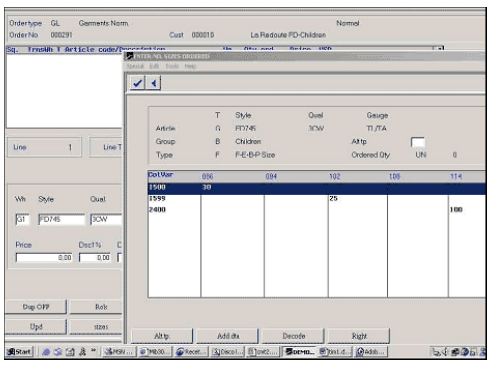
Fabric Inspection and Cut Optimization System
CATS (Computer Aided Textile Supervision) is a PC based module that integrates the production and inventory systems with greige and finished inspection. It provides methods to identify, map, and place inspected fabric defects either directly into the TIM database, or into an integrated PC network, so as to both archive the data, and to make it immediately available for use in allocation and production confirmation. CATS utilize an encoder to measure the cloth and a PC screen at each inspection table.
CATS is capable of:
- Providing a graphical user interface for inspection and cutting operators workstations, including connection to length counter
- Previous inspection performed for this roll or piece is simultaneously displayed on a graphical bar, just below the graphic bar of the actual inspection
- Coding defects, including length defects, keeping both length and width co-ordinates and denoting severity
- Ranking defects through user-defined parameters, including a points system
- Automatic calculation of quality level based on defect count or points. The quality level is constantly displayed on the graphic bar in real-time, changing color as one level is changed to another
- Producing reports of defect types, quantities downgraded per shift, per loom, etc.
- Multiple evaluation methods with different value grids
- Optimizing roll cutting
- Creating piece labels and tags
- Automatic uploading of inspected rolls/pieces into inventory
- Initializing re-inspection activities
- Interfacing with electronic weight checking systems
- Management of narrow width splitting after inspection
- Optimization of the joining of small rolls within a batch