The systems and procedures in stores can be broadly studied under four heads, viz. identification system, receipt system, storage system and issue system. The overall system of store functioning along with the major input-output documents at each state is shown in Figure I. A substantial amount of information is required, at every stage, for checking, controlling and feedback purposes. The stores systems have been discussed with reference to the physical system as well as the recording or information system.
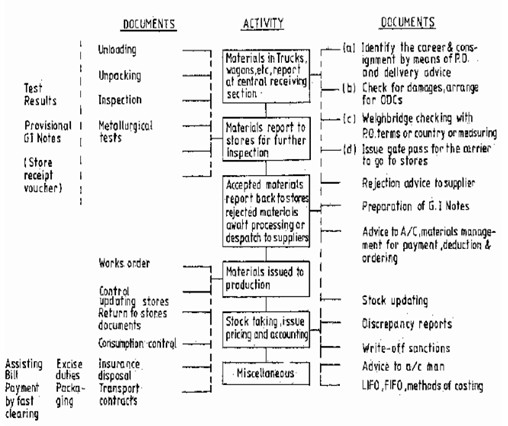
Identification System
The stores management is concerned with the design and control of the systems utilized in conducting the. Store activities A large number of materials are being handled by typical stores. Thus the development of an unambiguous and efficient identification system is the first responsibility confronting a store’s manager so as to facilitate clear internal communication.
The physical description of each item is usually lengthy and imprecise to be taken for the purposes of identification in day-to-day operations. Moreover, it cannot be operated on mechanical or electronic computing devices, the use of which is increasing every day in automating the clerical operations of the stores. One kind of identification of the parts can be done with the supplier’s part numbers. But each supplier has got his own codification system and it will be cumbersome to operate on these numbers for the identification of different parts.
Thus the need to develop a proper identification system to coordinate the activities of purchasing inventory control and stores departments with possible integration with the operations of design engineering, production and cost accounting can hardly be overemphasized. The use of codification of parts can be done in any one of the following. ways:
Arbitrary approach: The inventory items are given an arbitrary number in the sequence in which these are added in the stores account. Clearly, each item gets a discrete number but there is no systematic relationship to the numbers assigned to related items.
The symbolic approach: This is a very systematic approach to the design of codification system. The codes assigned to different parts may be numeric or mnemonic (alpha numeric). A numerical system assigns a six to ten digit code number to each item to develop the classification from broader to specific categories. This is illustrated with the help of following example:
The code number of an item is 152 43 25; the explanation is as follows:
First digit 1 General-class
Next two digits 52 Generic class
Next two digits 43 Subclass
Last two digits 25 Specific item numbers
This code is based on the assumption that there are maximum 10 general classes, 100 generic classes, 100 sub-classes in each generic class and 100 specific items in each sub class. If it is more than this limit in any of the categories, one more digit is to be added for that category. The general classification of the parts may be done as follows:
Code General Class
1 Raw materials
2 Purchased parts
3 Manufactured parts
4 Work in process
5 Spares.
This mnemonic or alphanumeric system combines the numeric and alphabetic notations. This makes the visual identification easier because they are more descriptive and often shorter. Atypical example is.

As the number of good alphabetical symbols is limited the system may not work with larger number of items.
The use of engineering drawing number: The number in the engineering drawing at times is used as an identification number in the stores. This has the advantage of better internal communication as this number is used by other departments. But it has the major limitation that it can be only for manufactured items; for bought out items a separate system is to be devised. Further, it has the non-sequencing disadvantage of arbitrary system.
Receipt System
The stores department receives the stores both from outside suppliers and internal divisions and accordingly there are separate receipt systems. The system of receipt starts much before the physical receipt of the materials in the stores. It starts with the placement of purchase order by the purchasing department, a copy of which is sent to stores. This is maintained in chronological order, so as to give an idea at any time about the volume of receipt, and helps in the planning of receipt, unloading, unpacking and other related activities. Further, the supplies while dispatching the Stores Management goods normally send an advice note to the stores. This contains information regarding the date of dispatch, carrier details, description of the consignment and value. Another document known as `consignment note’ is prepared by the transport carrier and is sent to the stores concerned. These documents help the store’s manager to organize and plan for expeditious clearance of materials to minimize costly demurrages.
On actual Delivery the receiving department unpacks the goods received and checks quantity and condition of goods using weighbridges, measuring devices, tapes, etc., and tallies it with that in previous documents. There is a packing slip inside each package detailing the contents in package and usually it gives the purchase order number.
A ‘Provisional Goods Inward Note’ (PGI) or a `Materials Received Report’ is prepared as soon as the materials are cleared from the receiving sections and sent for inspections. This gives information on materials code, quantity received, rate, date of receipt, carrier details, supplier details, location code and description of the material. All the items received are inspected and sample tested to ensure that the purchase order specifications are made. Results of the inspection are indicated in special testing report and a `Clearance Report’ or `Rejection Note’ is prepared and sent by inspection department to purchase, Production and Accounting departments. This forms the basis for the preparation of `Final Goods Inward Note’ (FGI) as shown in Figure II. FGI indicates quantity accepted and quantity received in addition to the information provided by PGI. FGI help in preparing shortage reports, claims documents, making appropriate payments and recoveries in case of shortages.
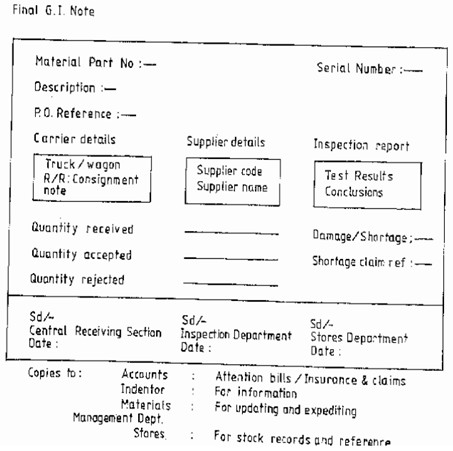
In case of materials received from internal divisions or returned from user departments transfer notes or `Return to Stores documents’ are used. In some cases, Stores Department also handles the scraps. Usually scrap cards are prepared to indicate the nature and weight of the scrap:
Storage System
A Physical System: The design of proper shortage system is very important for easy location, proper identification, and speedy issue to the consuming department. The commonly followed systems for physically controlling stores materials are: closed stores system, open stores system and random access stores system. A single firm can follow a combination of these systems depending upon the nature of production operation and the use of materials.
Closed Stores System: In such a system all materials are physically stored in a closed or controlled area, usually kept in physical control by locking. Only stores personnel are permitted to enter the stores area. Entry and exit of the material from the area is permissible only with the accompaniment of authorizing document. Maximum physical security and tight accounting control of inventory material are ensured by such a storage system.
Open Stores System: In this system no separate store room exists. The material is stored as close to the point of use as is physically possible. Such a system finds applicability in the highly repetitive, mass production type of systems exhibiting a continuous and predictable demand, e.g. automobile assembly plant. The storage facilities are arranged at each work station as per requirement and availability of space. The storage facilities are open and worker has direct access to it; no authorization document is needed.
The open type of shortage system expedites the activities, cutting down the retrieval time. Since material is used relatively quickly it is not subject to high rate of deterioration or obsolescence. This system places little emphasis on the security of materials. The materials used in open system should not be easily damaged or pilferage
The responsibility of stores in this system is to deliver the material to production areas and to devise satisfactory physical storage arrangements with production supervisors. The further responsibility of the materials stored in production areas rests with the production supervisors.
The paper work is also considerably less in open system, as it places less emphasis on accounting control. No perpetual inventory records are kept. The actual usage can be determined by finding the difference between the number of items in the beginning and end of the period.
Random Access Stores System: This is a typical kind of closed stores system in which no material has a fixed location, All materials are stored at random locations throughout the store room. However, similar types and sizes of storage equipment are grouped together. When an item enters the stores, it is stocked at the first available storage location for that particular group, and when it leaves the storage, location becomes empty for any other item of the same group.
Usually a paper-work control system utilizing punched card data processing equipment is employed. On the entry of any particular items a punched card is prepared with stores address. The requisitions are run on an electronic device that matches the requisition with stored material record which contains the store’s address.
The most significant advantages of this system are that it utilizes the space more efficiently than a fixed location, system. Further, it provides greater flexibility by accommodating different materials and inventory mixes with some storage facilities.
This type of storage system has got certain disadvantages too. It is feasible for large scale operations and requires a costly control system using electronic data processing equipment. The preservation of record card is very important; if it is lost the item is also literally lost for indefinite period. Moreover, the physical stock verification without this is very cumbersome and time consuming.
B Store Records System: Development of appropriate recording system for stores is important to provide right information regarding the physical inventory and accounting of the transaction. Two records are usually kept of materials and other goods received, issued or transferred, namely, on Bin (or Stock) Cards and in the Store Ledger.
Bin Cards: For each kind of material, a separate record is kept on Bin Card which shows details of quantities of each type of material received, issued and on hand each day. A typical Bin Card is shown in Figure III. The Storekeeper maintains the Bin Cards up-to-date and usually in duplicate. One card is attached to each bin on shelf containing the material and record remains with the storekeeper for reference. Some firms use the KARDEX System in which a Kardex is prepared and updated. Bin cards are also used as a check on the stock I edger accounts in the material accounting division.
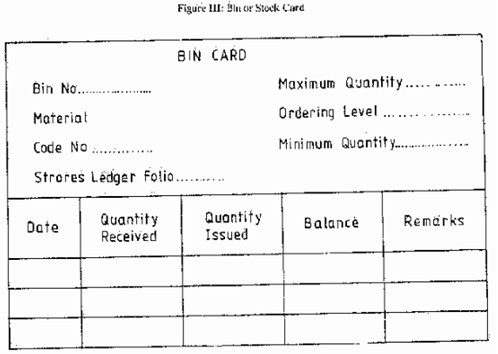
Stores Ledger: It is identical with bin card except that here money values are shown. The store ledger may be maintained by a separate material accounting department. The entries regarding the materials ordered, received and issued are made from the purchase order, receiving section report and the material requisitions respectively.
Issue System
This is the last stage in the stores system. Issues can be of two kinds, i.e., issues to consuming departments, and issues to outside supplies for processing. In both the cases there are certain common requirements. The control of issues is regulated by production programmers. Based on the programme and the bill of materials work orders are prepared, listing for each material quantity to be issued and the corresponding quantity of the component to be manufactured. Any material requirement over and above indicated in the work order quantity means excessive wastage and scrapping usually, the junior stores personnel are not authorized to issue beyond the work order quantity which brings an inbuilt control.
Normally, two copies of the work order or Material Requisition Form (shown in Figure IV) are prepared by the foreman or concerned manager which are forwarded by the storekeeper to material accounting division for pricing and entry in store ledger. One copy is retained there and the other is returned to the originating department where it is used as the basis for a charge to the appropriate production order: Adhoc material requisitions are sometimes made. Periodically consolidated statements of such items must be prepared. When issues are made to outside supplies, controls have to be more formal and adequate enough to take care of payments and claims.
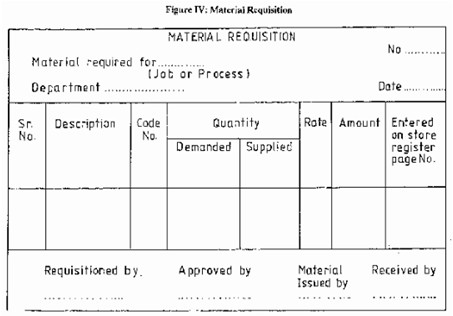