Once a company gets off the ground, the next possible step usually involves optimizing processes and adopting a model of continuous improvement. This is where the 5S strategy comes into play. By adopting a 5S strategy, manufacturers can maintain their focus on running a lean operation without sacrificing the health and safety of employees.
5S is a simple step-by-step methodology to ensure that workspaces and resources are arranged and maintained in an orderly manner, thereby enhancing productivity and reducing waste. Furthermore, 5S allows the business to function at peak capacity with minimal interruptions in service.
In this article, we will be talking about 5S and its importance. Moreover, we will be sharing the steps required to gain excellence. So, let’s begin.
5S: An Initiative for workplace efficiency
Borrowed from the Japanese concept of Poka-yoke and popularised by Taichi Ohno and Shigeo Shingo, 5S is a system for organizing spaces so work can be performed efficiently, effectively, and safely. The main focus of the 5S system is to put everything where it belongs and to keep the workplace clean, thereby ensuring people do their jobs without wasting time or risking injury.
5 Steps towards excellence
5S refers to the five terms, all beginning with the letter S when transliterated. The equal terms in English also begin with an S. Basically, these five terms represent the five steps toward operational and process excellence:
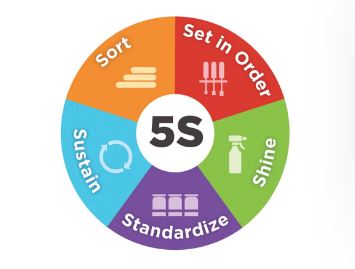
Step 1: Sort [Seiri]
Firstly, in this step, the 5S practitioner is responsible to go through all the equipment, tools and resources they have. Further, the practitioner has to determine which equipment or resources need retention on the work floor and which resources require rejection. To keep things simple, the practitioner has to segregate the important or useful things from the unnecessary thing and discard the unnecessary.
Step 2: Straighten or Set in Order [Seiton]
Secondly, in this step, the 5S practitioner has to reorganize their workplace after eliminating unnecessary tools and equipment. In this particular step, the practitioner follows the simple philosophy of “a place for everything, and everything in its place”. This philosophy simply helps the other staff members locate the required resources easily and swiftly. This concept can be applied to any sector.
Step 3: Shine [Seiso]
Subsequently, in this step, the practitioner makes sure that the equipment and tools are tidy and are ready to use by other staff members. For instance, if this concept is applied in the information technology sector, then the practitioner has the responsibility to delete all the irrelevant files and folders and clean the file system.
Step 4: Standardize [Seiketsu]
After that, in this step, the practitioner can combine similar work activities in their facility and allot a workspace for that particular process in the work facility. For instance, if there are five lathe machines dispersed across different locations doing the same work, then the practitioner can place all these units in one place, so as to achieve through constant monitoring of work processes. This concept is applicable in any sector to reduce redundancy.
Step 5: Sustain [Shitsuke]
Last but not least, the final step in the 5S is concept implementation. In this stage, the practitioner has to ensure that tools, equipment, and resources are in neat and tidy condition and they are placed where they are meant to be.
Who Should Participate in 5S?
The shortest and the only answer to this question is everyone. That is to say, if a department is starting 5S, managers and all other employees should be included. If anyone is overlooked, this could lead to confusion that people don’t want to take ownership of.
However, there is a possibility that some people will play a bigger role in 5S than others, which is fine. There might be 5S coordinators who are in charge of installing and maintaining 5S labeling, keeping tracking of assigned tasks, or introducing new department members to the 5S system. These people will obviously spend a lot of time thinking about 5S compared to others. Everyone should think about 5S regularly, though. 5S initially take place as an event, but gradually, it becomes a part of daily work for everyone.
Most importantly, it becomes important for the company leaders to participate in 5S, especially if 5S is a company-wide effort. When people see their superiors taking 5S seriously by participating in it, they will be more likely to take it seriously, too.
Importance of 5S
When you adopt 5S, you make a commitment to put safety, organization, and effectiveness ahead of production deadlines, profits, and output.
When deciding whether 5S is a good option for a given situation or not, it is best to give a look at the importance attached to 5S.
Increase in Efficiency
First things first, 5S is a great strategy for business in improving the efficiency of a facility since it helps to put things in their proper place and standardize the way work is done. Moreover, 5S can help the business to cut down on wasted time looking for and transporting parts, ensuring that things are completed as quickly and correctly as possible.
Ensures safety at workplace
Secondly, cutting down on workplace accidents and injuries is critical for all companies, and their employees. Here, 5S plays a crucial role by clearing away clutter, keeping everything in good working order, and maintaining progress. This all adds up to a much safer work environment for everyone.
Reduces waste at workplace
Further, for most workplaces waste is a big problem that disturbs the costs. Irrespective of the form, the waste i.e excess materials have to be disposed of, or products that are created with defects, or some other form of waste, it is important to get rid of it. Therefore, 5S is set up used to eliminate this type of waste by improving processes and minimizing defects.
Improves existing strategies
Lastly, if a facility is using other improvement strategies such as lean manufacturing or Six Sigma, 5S can surely be a great addition. The 5S system works well with all other strategies because it is a repeatable set of concepts that can be applied to almost any environment.
Possible Challenges to Initiative
5s is one of the most fundamental building blocks in a lean process. However, many people often misinterpret it and certainly end up giving the results that they didn’t expect to have. Some of the challenges are mostly found as resistance to changes by Stakeholders. This takes the form of
- No procedure for monitoring non- compliance
- Ineffective feedback where procedures are available and implementation is in place.
- Unfavorable comments from workers and departments who have been involved in unsafe work practices especially when non-compliances are communicated with objective evidence such as pictures.
- Lack of understanding of the concept of following a standard which is supported by the employee policy and the factory act relating to a safe and clean environment
- Lack of encouragement from some stakeholders to participate in a highly rewarding employee suggestion scheme for committed employees and departments
Career Opportunities
While you make up your mind to take up 5S certification, you surely want to learn about currently available jobs for the same. Therefore, in order to ease your learning, we have provided a list of the following:
- Firstly, Quality Improvement Specialist
- Secondly, Senior Manager
- In addition, Senior SQE Manager
- Subsequently, Business Process Engineer
- Moreover, Senior Procurement Specialist
- Further, Business Operations Analyst
- Last but not the least, Senior Manager
Top Recruiters
After scrolling through all the details, you might be keen to know the carer opportunities which involve the name of the company. There are many top-level companies ruling over the market space for a long time. Some of the top financial institutions hiring 5S professionals include –
- Oracle India
- KPMG
- Accenture
- TCS
- GE
- Genpact
- Vmware
Base Salary
Once you are exposed to the top recruiters that might hire you, let us give a look at the salary of the 5S professionals. In general, the average salary depends upon the knowledge and expertise you bring to the table. That being side, the average pay scale for jobs that require the skills of the 5S method is $104,554.

Using the right Learning Resources
If you want to learn 5S sooner rather than later, then creating time-management habits will be beneficial for you. Therefore, here are a few learning resources that will surely work in your favor. So, let’s get started.
Online Tutorials
Online tutorials are one of the most effective parts of the learning process. Ther are basically the teaching sessions which take place over the internet. The main motive of tutorials is to transfer the knowledge in such a manner that the candidate imbibes the idea of tutorials at his/her own pace. So, Make your learning easy here.
5S Certification Courses
There are a number of certification providers that offer courses to become a Certified 5S Professional with a self-paced or live trainer that can help you in learning 5S up to intermediate level. Furthermore, these courses will be beneficial in advancing your skills and career. However, it is important to understand that there are only a few certification providers that are widely accepted. So, make sure to choose wisely. Some of the top certification bodies include,
- Vskills – India’s Largest Certification Body
- ASCI
- Coursera
- ASQ
- Udemy
Study Groups or Forums
The idea of getting enrolled in study groups and forums aads nothing, but an advantage. That is to say, these online study centers allow aspirants to keep up with the learning trends. Moreover, they help the aspirants to clear their doubts if they have any. However, it is equally important to note here that the idea of joining study groups or forums is completely subjective.
Practice Tests
Practice tests may be the oldest medium to study, yet are one of the most beneficial as well as reliable medium to study for the exam. The evolution of practice tests form pen-paper to online has been remarkable which adds more to its generosity. They not only help you find the errors (strengths and weaknesses) but also provides you a chance to rectify the errors before it gets too late. Ready to take the challenge? START PRACTICING NOW!
Final Thoughts
To conclude, the process of 5S is simple and has applicability across various spheres of business environments. For say, simple techniques like Sort and Shine is possibly applicable without the workplace and the homes as well.
We hope the article has succeeded to open your mind to a new perspective on the behavior of people you are trying to engage in continuous improvement. Constructive feedback welcome!
Stand out from the crowd with advanced learning skills and expert tutorials on 5S. Prepare and become a Certified 5S Professional Now!