INVENTORY MANAGEMENT IN SCM
Inventory is considered as a very large and huge investment that every stage of the supply chain needs to acquire. The Supply chain management has been organized in such a way that every stage works independently to make the supply chain profitable. It therefore becomes very important for every stage of the supply chain to coordinate together and thereby form the inventory policy.
What is the need for holding inventory?
- For achieving economies of scale
- To balance demand and supply
- To attain specialization
- To protect from uncertainty and order cycles
- To act as a buffer between the various stages of the supply chain
Types of Inventories
- Cycle inventory: It is the average inventory that exists in a supply chain, due to excessive production or purchase of products in a given lot sizes larger than those demanded by the customers.
- Safety inventory: Safe inventory carried is primarily kept for the purpose of satisfying the demand that exceeds the amount forecasted for a given period of time.
- Speculative inventory: Speculative inventory refers to the stock held for reasons other than satisfying current demand. For instance, a manufacturer might purchase more material; more than what is actually required to serve the current demand.
- Seasonal inventory: Seasonal inventory is a form of speculative demand involving the accumulation of inventory before any season begins in order to maintain stable production or maintain a stable work force during periods of seasonal demand.
- Dead stock: Dead stock refers to those products for which no demand has been registered over a large period of time.
Costs Associated with Inventories
Following are the various holding cost associated with inventories which is estimated as the sum of the given costs. In general, the holding cost is referred as a percentage of the cost of the product –
- Cost of capital: Holding cost using the weighted average cost of capital (WACC)
Where,
E = amount of equity
D = amount of debt
R f=risk free rate of return
b = the firm’s beta
MRP = market risk premium
R b = rate at which a firm can borrow money
t = tax rate
- Spoilage cost: Spoilage test refers to the value of the product which a firm stores, drops following a drop in the market value of the product or due to quality deterioration.
- Handling cost: Handling cost includes receiving and storage cost of the products. Handling costs primarily vary with the quantity of products received.
- Occupancy cost: In case a firm is charged on the number of units stored, then we call it the direct occupancy cost.
- Miscellaneous cost: It refers to any incremental costs arising due to a change in the cycle inventory must also be added to the holding cost.
Inventory Control Systems
Since demand and lead times differ so fixed quantities of stock are order at variable times or order variable quantities at fixed times to fix the difference. Each one has inferences for safety stock, operational responsiveness, the level of risk involved given variable demand and supply and security.
Inventory Control Systems
As demand and lead times are variable, we can either
- Order fixed quantities of stock at variable times or
- Order variable quantities at fixed times
Fixed quantity systems (Re-order levels)
- It is easy to manage
- It manages well with demand variability/changes and facilitate lower stocks
- It orders can also be processed for convenience e.g. small orders can be consolidated to secure supplier discounts
Two-bin replenishment system: With the first bin empty, a new full bin is “called” to arrive before the second bin is exhausted. The call is then rotated.
Stock records
A two bin system is suited to components needing to be issued in large quantities and where the bin size and hence ROL can be checked simply.
Fixed Time/Order Cycle Systems
Annual requirements for low value, low bulk items can be estimated and ordered in a routine re-order cycle. At the routine re-order time current stock can be subtracted from the maximum to give the order quantity
Re-order level approach
There is a risk of stock outs with expected rising demand but outstanding re-supply orders can be chased.
Re-order cycle systems
Rising demand can exhaust stocks with no outstanding orders in the pipeline.
Which System?
Many organizations operate a hybrid. Choosing between fixed quantity or fixed time approaches depends on risking unexpected movement in demand against the costs of administering convenient, scheduled replenishment.
Risk and security
Accurate stock records assist security monitoring (detecting theft) and control. A two-bin or annual demand system offers little security for high value, important, difficult to supervise items.
Economic Order Quantity
Economic order quantity (EOQ) is defined as an ideal order quantity that a company should purchase for its inventory considering a set cost of production, demand rate and other variables. This process is conducted to minimize variable inventory costs, such that the equation for EOQ takes into account storage, ordering costs and shortage costs.
Purchasing an economic order quantity (a.k.a. economic batch quantity, economic lot size or EOQ) seeks to reconcile ordering and holding costs to obtain an optimum order size.
Cost of holding stock and ordering/acquisition cost are represented by
- The value of the average stockholding = (Q/2 x item cost/value) where Q is the order quantity. The holding cost/unit (C J is derived from the average inventory value) multiplied by the cost of carrying the item over the period (one year) expressed as a % of the item cost/value.
- Order cost (CJ is derived from the number of orders placed (D/Q – demand p.a. divided by order quantity) multiplied by the cost of placing an order.
- Order/acquisition cost or set-up cost for a make-to-stock situation.
Holding costs = Q x Q/2
Ch is the holding cost/unit Ordering Costs = C, x D/Q
Such that C is the ordering cost Therefore, Total cost = C. + C
EOQ is found at the lowest point on the total cost curve. Here the order size optimises the cost of stockholding with the cost of acquisition. Given by –
Safety Stock and Service Levels
We may run out of stock because of a re-supply delay or higher than anticipated usage. If we can predict demand then we merely place EOQ orders on time. Represented by the figures below –
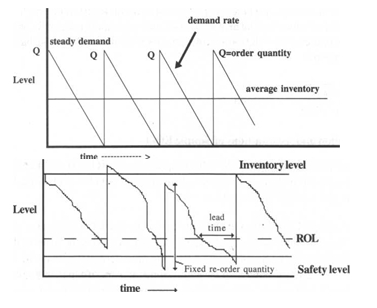
MRP and JIT
JIT originated in Japan. Its introduction as a recognized technique of working is generally associated with the Toyota motor company, JIT being initially known as the “Toyota Production System”. Within Toyota, Taiichi Ohno is most commonly credited as the father/originator of this way of working. In his system waste was eliminated by just-in-time – items only move through the production system as and when they are needed. In this system inventory (stock) is regarded as an unnecessary waste as also the need to deal with defects. Some of the sources of waste are – overproduction, time spent waiting, transportation, processing time, inventory and defects.
JIT Outline Points
Japanese industry works just-in-time, Western industry works just-in-case. JIT is also known as stockless production or lean production. JIT is a suitable production system when –
- Steady production of clearly defined standard products.
- Reasonable number of units made.
- High value product.
- Flexible working practices and a disciplined workforce.
- Short setup times on machines.
- Quality can be assured, e.g. zero defects either through good working practices or through a cost penalty.
JIT Philosophy
- Based on elimination of waste in its many forms
- Based on the belief that ordering/holding costs can be reduced
- Based on continuous improvement, always striving to improve
Elements of JIT –
- Regular meetings of the workforce
- Discuss work practices, confront and solve problems
- Emphasis on consultation and cooperation
- Modify machinery
- Reduce buffer stock
- Expose problems, rather than have them covered up
- Reveal bad practices
- Take away the “security blanket” of stock.
Kanban
Kanban is a signal or message or communication, e.g. wave hands, shout, send a card, electronic signal. It is primarily used to control the flow of items though the production process.
MRP
Material Requirement Planning(MRP) is a product oriented computerised technique aimed at minimising inventory and maintaining delivery schedules. MRPrelates the dependent requirements for the material and components comprising an end product to time period known as bucket over a planned horizon on the basis of forecasting provided by marketing & other input information. The system sets a schedule so that each raw material, assembly and part that is required for production will arrive at the correct time simultaneously to produce the final product that appears in master production schedule.
It is also said that Material requirements planning (MRP) is a ‘Push’ system and JIT is a Pull System