Introduction
Warehousing is the major component of physical distribution. Warehousing management has two distinct and equally important parts: (i) the physical job of creating and running the network of storage points, and (ii) the managerial task of controlling inventory levels without sacrificing service levels. Though interrelated, they require separate and detailed discussion. We shall, therefore, devote two independent sections to the subject. In the first, we shall deal with the warehousing aspects and in the second, with the inventory management aspects.
Designing a Warehousing System
In most cases, products flow from the factory to the consumer through a long winding chain, consisting of multiple tiers of warehouses and multiple tiers of marketing intermediaries in designing a warehousing system, the following basic questions relating to this flow become significant.
- How many warehouses should we have?
- Where should we locate them?
- What should be the size or capacity of each of them?
The Cost-Service Tussle
When we look closely at these questions, two interesting, but conflicting, points emerge. Salesmen and channels always plead for greater convenience in delivery and consequently more warehouses. But, maintaining a large network of warehouses is a costly proposition. Thus, there is an inherent tussle between cost and service in warehousing decisions.
Warehousing to be tackled as Part of the Physical Distribution System: While designing a warehousing system, the fact that warehousing is a part of the overall distribution job should be borne in mind The warehousing design should fit smoothly into the overall distribution design, which includes physical distribution elements like transportation plus channel arrangements, which will be discussed in the succeeding chapter.
Warehousing, a Partly Fixed and Partly Adjustable Entity: In most cases, it may be apt to view demand in a given territory as consisting of a constant component and a transient component, which is to be added to or subtracted from (mostly added to) the constant component. Past sale corresponds to the constant component. Changes occurring in demand in the current period correspond to the transient component. The transient component is related to change in market demand per se, or company demand (a company may lose or gain relative market share). Thus, in the nature of things, warehousing will have a constant component plus a variable component. And, there is some scope for adjustment in warehousing of products, depending on market behavior/company’s performance.
Warehousing Job can be Taken Care of in Different Ways: As regards the actual organizing of the warehousing system, different alternatives can be considered by the firm.
- Hire warehousing service from public warehousing agencies
- Own the god owns and manage warehousing through company staff
- Entrust warehousing to C&F agents/stockiest/distributors
- A combination of the above
Each alternative has its associated merits and drawbacks. Decisions have to be basically situation specific. FMCG (Fast Moving Consumer Goods) firms usually transfer a large part of the warehousing task to their C&F agents.
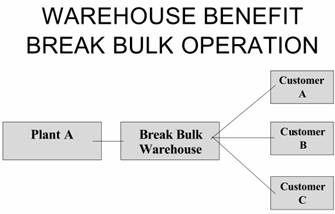
- Determining the Number Location and Size of Warehouses: Determining the locations and capacities of the warehouses is the crux of the task. On this depends the firm’s customer service level, its competitive advantage in distribution and its inventory cost structure. While one might point out that it is the inventory turnaround that primarily determines inventory costs, the fact remains that the costs are also influenced by the locations and spread of the inventories -at how many places and in what sizes are stocks kept. Moreover, inventory turn- around itself is partly the outcome of the manner in which the inventory is spread.
- Determining the number: The optimum number will depend upon the nature of the product, the size and geographical spread of the market serviced by each warehouse the current and potential sales in the territory, the extent of seasonality of demand if applicable, the level of peak demand, the trade patterns, the number of distributors/retail outlets to be serviced by each warehouse, the acceptable order-execution time, the possible speed of replenishment of stocks and the cost involved in operating warehouses. Future requirements and pattern of competition are also relevant factors in deciding the number and sizes of the warehouses.
- Choosing the size: The decision on the size of the warehouses must be taken in alignment with the decision on their total number After a firm assesses the sales potential in each warehouse territory, the question to be decided is: What is the optimum inventory holding needed for realizing the sales projected for the territory?
Warehouse size and costs are inversely interrelated. So, as a general rule, small-sized warehouses are uneconomic compared to larger ones. At the same time, if the sales projected are small, warehouse size has to be small. Customer convenience and channel service will call for a large number of small-sized warehouses spread extensively all over the marketing territory. There will also be the additional consideration of future requirement. As a general rule it can be said that by reckoning the volume of sales and the desired market share in the area covered by the warehouse, and by applying the factors of transit time and peak season demand, the optimum warehouse capacity at a given location can be worked out’.
- Choosing the exact locations: Choosing the exact locations of the warehouses is as important as choosing their number and capacity. The locations must be suitable in terms of market factors and availability of transport facility: Rent rates, commercial suitability of the location, implications of local levies, etc., have also to be looked into. Above all, availability of suitable go down space has to be considered.
- Improving Warehousing Effectiveness: Warehousing effectiveness can be improved by adopting scientific methods and by taking the support of IT. In the larger context, however, warehousing effectiveness depends squarely on right policies of physical distribution.
Scientific warehouse layout in itself facilitates warehousing effectiveness. The layout/design must be suitable for the product(s) concerned and the nature of storage and in-out operations.
Warehousing effectiveness also improves when the handling and movement of items within the warehouse is minimized. This applies especially to large warehouses and products involving extensive storage, receiving and issue operations. Every time an item is moved within the warehouse, it means an opportunity for damage to the item; and each lifting of the item fatigues the package.
Systematic stocking of items is another factor. If the items of high demand, with high frequency of in-out operations, are kept in the front and the relatively slower moving items in the rear, it will facilitate smooth operations and also help reduce the overall costs of warehousing. It is such matters of detail that make the real difference between poor and good warehousing.
Elements of Inventory Costs
ü Interest on capital tied up in the inventory ü Warehouse rent ü Staff salaries ü Insurance ü Rates and taxes ü Stationery | ü Postage and communication charges ü Administrative overheads ü Costs of handling, unloading and stacking ü Loss due to damage and deterioration while on storage ü Cost of order processing/record keeping/accounting |
In many cases, warehousing as a whole becomes inefficient on account of unreliable sales forecasts. When actual sales show great divergence from the forecast, any warehousing plan naturally goes haywire and its effectiveness suffers a setback.
Apply for WordPress Developer Certification Now!!
https://www.vskills.in/certification/certified-wordpress-developer